|
Post by 4real on Sept 23, 2011 1:25:09 GMT -5
Hi here GN2'ers, been a while...getting the build a guitar itch again...hmmm So...this is a project that has been 'in the basement' for a while and an experiment that might lead to another project down the line. I have some typical electro acoustic pre-amps and under saddle piezos here, some even have tuners and balanced outs. So the project is to mount a single HB like neck pickup (looks like a filtertron copy, though I might use a full size HB...decisions not made yet. I am thinking of ways that the pickup might be mounted under the saddles of a strat on a tremolo bridge. I was thinking if I were to mount it perhaps under a thin aluminium plate this might suffice to transfer the vibrations regardless of the intonation adjustment. An alternative would be to use and arch-top like straight acoustic like bridge perhaps...it is an unusual project guitar. So, there will be the usual piezo preamp set into the upper side, but I need a way to add in the Mag pickup (ensuring impedance matching), some kind of mix control, basic tone (on the mag only would be best) and master volume. I am assuming some kind of buffer for the mag pickup might be needed...any thoughts? The guitar would you believe is a true acoustic hollowbody, the neck an old strat copy. IF I use the fender bridge and springs and all, might be the only archtop around with a fender style trem, springs and all inside. I am playing quite a bit of 'fingerstyle' and working on building up arrangements. I've been using my strat quite a bit but for various reasons this is not ideal (even if I like it) and some of them aesthetic. The idea is only to add in a bit of the acoustic sound to give a percussive edge and harmonic complexity over the body of the mag pickup. The guitar should look ok, certainly unique...but I ahve in mind another twist perhaps later down the track that people might have an opinion on. It occurred to me that a lot of the bass lines are primarily on the low E and A strings and that perhaps there might be a way to make a 'two string pickup' for these strings and a separate 'out'. The intention to run this as a separate 'out'...by perhaps running this signal into a 'pitch shifter' from a cheap digital multi effects unit, I could create something of a 'sub bass' an octave lower to give everything a bit more 'depth' and might sound ok is used subtly. As there is going to need to be some electronics in this guitar and internal room doesn't seem to be much of a problem, I was thinking about using a pair of tiny transformer coils, perhaps rigged to be HB'ing under the lower strings as a low impedance pickup system...perhaps people could think of a better way, critique the idea or offer up some other input. Ahhh...here is a pic that I took a few years ago when I first started getting ideas for it... 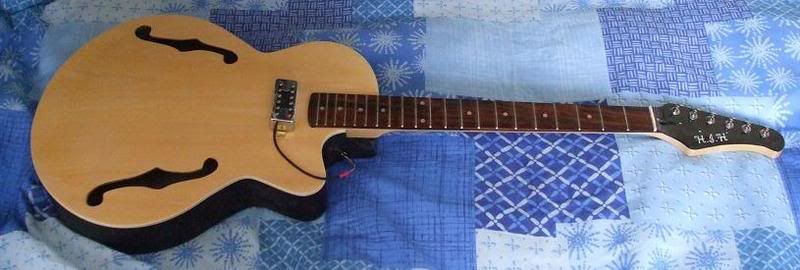 The whole project will be using parts that I already have, I found a better neck than this one and is strat like 21 frets. I don't know if these guitars are still about, I was giving them away at one point and have about 3 left I think. I took off the fake flame coloured finish to reveal a natural 'blonde', the back and sides are ovation like plastic. If I go the trem route, I will need to mount the springs and such and have an access plate on the back with will give me access to inside. The bracing will need to be altered for the bridge. I'm not completely sure if the top will take a strat like tremolo bridge, but the springs will be mounted to the body some how and some timber added to secure it obviously. It would not be a necessity to make this quirky choice but it would be good to have at least the intonation adjustment. I could use a conventional archtop straight bridge but there is no intonation adjustment and would require mods anyway...so in two minds there.
|
|
|
Post by JohnH on Sept 23, 2011 3:50:57 GMT -5
The up in this thread was was somewhat similar: guitarnuts2.proboards.com/index.cgi?board=schem&action=display&thread=4595Its not quite the same, since it had an active mag pup. In your case, my thought on the electrical aspects would be to feed your mag pup to its own passive volume and tone control, then take the output of that to a Buffer (another of the same circuit as in my thread linked above), then the blender module. It'd work great! (promise) John
|
|
|
Post by 4real on Sept 23, 2011 4:01:47 GMT -5
Thanks John, looks very similar to the kind of thing I was looking for, didn't find it on a brief search.
I might well want to do this with an acoustic and some other projects.
I figured I would want to make a simple 'buffer' (is this what this circuit is?) for the mag pup, perhaps with tone for that, then a master volume for the whole guitar before the output (would a 10K-25K pot be more appropriate for this being 'active'). A 'blend would be a good option too. Obviously the piezo preamp has volume and extensive EQ, but I was not thinking of having the two connected through that.
I am still umming and ahhing about the bridge though. Be a shame to cut into the guitar for such an experiment even if 'cheap' I think it could actually sound quite good plugged in and made to look 'presentable'. A more traditional bridge and tail-piece might be the go and be more amenable to things like dropped tunings that I sometimes use...hmmm...no hurry on this one, but if I like to know what I am getting into before starting a project
thanks for the help though, you are the man lol ;-)
|
|
|
Post by JohnH on Sept 23, 2011 15:21:48 GMT -5
If you want a master volume at the end of the circuit it can be a lower value than on a passive guitar, but not too low to avoid loading the output too much. If you only want to drive standard amp inputs or stompboxes with this guitar, then you could use 100k. But I think it is good to be able to drive line inputs from an active guitar, particularly if there are piezos involved, since they sound good through PA systems. In that case I would suggest a 25k volume pot (in place of R4), change R3 to about 10k and delete R4. Current draw will rise to about 0.6mA on the output stage - still not too bad. The other way is to use a 100k pot, followed by another buffer stage. Personally, I wouldn't see the need for a master volume if you have seperate piezo and mag volumes plus a blend control. On my piezo-strat I have just the mag volume and blend, no piezo volume either.
I think the piezo element location is a subject for experiment. I suspect there may be big tone and output differences between locating it where vibrations are travelling through the element causing changes in pressure through the piezo itself, as against a similar position but where the piezo is just riding along with part of the guitar, but not getting squeezed by sound waves. Eg, attaching it to a floating working trem block would be quite different to having the piezo locking the trem block and having vibrations transferred through it to the body.
cheers John
|
|
|
Post by 4real on Sept 23, 2011 17:30:05 GMT -5
Thanks John...I will need to do some further research and experimentation.
The Piezos are as per that link to the acoustic guitar implementation and has it's own active tones and volume, what I am seeking though is to have a master volume, it is important to be able to turn guitars 'off' I find.
A blend and master volume and perhaps a mag tone control would suffice. I like to keep things 'clean' these days, so might use small knobs on the side near the acoustic preamp and a master close to the strings to control dynamics, possibly the blend control.
I was considering using an opamp kind of thing to buffer things, especially if there are going to need a few buffers and such to implement. For some reason I have found J201's hard to get in Oz though I might have some around somewhere.
I am hedging more towards an archtop like bridge today...hmmm...both options have challenges to fitting the piezio which is a straight under-saddle kind of thing, especially as I am fussy about compensation/tuning and will have to construct something either way.
I think the way to proceed will be to get the parts to all fit generally well, adapt the neck pocket and such for the strat neck, then set the guitar up as an 'acoustic' with a pickup fitted. See how I might adapt a traditional bridge, then wire everything to a cardboard forma and test things like pots and such. Fitting everything into such an acoustic is not too hard for space, but it can be tricky to get into such a guitar without a 'sound hole' to reach into.
The guitar will generally be built for this solo 'tuck andress' kind of thing so looking for a bit of a percussive edge and acoustic qualities, but a jazz like smooth body to the sound. I am learning from "Jake Riechbart' at the moment who uses a small amount of piezo to his magnetic sound. I don't imagine that I will want to alter things too much while playing, but it is conceivable that I will want to alter the tone of the guitar (acoustic/electric balance) between songs.
The 'extended bass thing' is an interesting one but will be easier to experiment with with a functioning instrument. I can think of several ways to make a small low impedance pup and as it will be only to create a subtle low 'double' to the low strings I suspect that tone quality will not be too much of an 'issue'. Impedance matching will be though, so perhaps this little buffer will work for this too.
Anyway, feel better knowing you and the GN2 have got my back on some of this and I certainly feel more confident that this will be possible before I start hacking into my guitar.
If it works out ok, I have a similar proposition for my old epiphone acoustic perhaps and I have in the closet another LP and wanted to experiment with adding a similar system to a Khaler trem...I could use the one I made earlier in the year to test out the concepts perhaps.
thanks again, pete
|
|
|
Post by newey on Sept 23, 2011 20:12:22 GMT -5
My in-the-works Stealth Strat project has some similar design issues, although a bit different. My piezo will be body-mounted, both piezo and mag will be buffered, more or less per JohnH's design. I specifically elected to separate the piezo from the trem as I wanted a std Strat trem and John convinced me to not put the piezo on the trem for the same reasons he discusses above. As far as the separate output for the 2 bass strings goes, if it was 3 strings instead of just 2, you could probably adapt an existing mag pickup- I'm thinking of the pickups from the Fender XII, or maybe 1/2 of a P-bass pickup. IIRC, the old Gretsch stereo White Falcon ('60s vintage) had the 2 channels split between the top 3 strings and the bottom 3. That was a filtertron style pickup, so those exist as well.
|
|
|
Post by JohnH on Sept 23, 2011 21:20:27 GMT -5
Pete -OPamps are obviosly great for creating all kinds of useful circuits with control of gain and tone where needed. the main reason I go with JFETs in guitars though is that you can make a high qaulity circuit with very little current draw, way under a mA, whereas opamps tend to need several mA. For buffers, the JFET type is not critical - Ill have a look around the aus suppliers to see whats available - i tend to use 2N5457 for everything.
John
|
|
|
Post by 4real on Sept 26, 2011 20:26:23 GMT -5
Thanks for the replies...been away, but keener to make this happen.
I am wanting to use an undrrsaddle piezo rather than a DIY Buzzer element kind of thing. I ahve experimented with this type of thing and had some success with them in the neck pocket of a fender...but they can pickup 'handling noise' and the body quite a bit that I would like to avoid. The under-saddle things tend to pick up more of the direct string to saddle to piezo sound than the top or body. The neck pocket idea works surprisingly well, but it tends to pickup the actual sounds of the fretting hand, especially on the higher frets...
Another reason is that these things come with a preamp with extensive tone controls match to it some what and in the one I am considering, a tuner too so a nice thing to have.
The tremolo thing might be a little over the top and I now see that this might be a little much for this guitar and so am settling on a typical arch top quite high bridge and tail piece and angling back the neck a bit to accommodate it...modifying it to accommodate the piezo strip. This will be far easier to test without mods to the guitar itself and to test on the working 'acoustic instrument' before I get to ahead of myself.
I still like the idea of the trem and use it on my strat in this style. I ahve heard of the 'bug on the block' style thing working an working trem strats, but I would be concerned that it would be picking up a bit of pivot and spring noise which would defeat the purpose. I do have in mind a similar thing on another LP with a kahler. The kalers are very smooth and the cridge itself does not move so is a bit more like a bigsby in that way, this might make for a better result and easier to test the concept using my existing kahler LP...but that's a long way down the track and this guitar is really a test bed for some of those ideas.
I did not know that the Gretch white falcon had a split pickup, interesting. The idea I have is perhaps slightly different.
I am thinking of making the guitar work as normal and just adding in a 'sub bass' octave to the lower two bass strings. I think with the archtp style bridge there will be room to surface mount a very compact low impedance device well away from the neck mag or effected by string bending and such to add this lower tone to provide bass depth, or two turn it off perhaps and be fairly discrete. It is an interesting idea though given that decent pitch shifting technology that is around and that it will be only supporting the original octave of the strings themselves, delays in tracking will not be very noticeable...worth the experiment.
The first step is I think, to set the guitar up to play well as an acoustic instrument and 'feel right', probably including the mag pickup (have not decided yet between a filter tron or PAF style HB)...Second step is to add in the piezo, buffers and other controls to this working instrument. Third step is to experiemnt with this additional two string pickup device.
For making such a pickup, I am thinking there are inductors of around that size (smaller than 1cm in diameter) that could be fitted with a small rare earth magnet and produce a signal. Having two would mean that I could rwrp for noise cancellation. I believe that the early midi synth pups were in fact six tape heads. Obviously such a device would require buffering , perhaps even pre-amping, but as I am thinking of these things as more of a additional low bass thing, I am anticipating that the tone' will be less important than the subtle pitch below filling out those bass lines.
I will see what I have and can easily get, I suppose that on the net I could order just about anything and I think I may even have some J201 samples around. I do tend to neglect the power usage thing, mainly because they are low drains generally and in a guitar that will have an entire multiple active circuits and tuner and EQ in it...but great battery access. But, since there is a nice tested discrete circuit available for both buffering and blending, be a bit sill to reinvent the wheel and likely give this a go for want of a ready alternative.
Anyway, one step at a time and getting pretty motivated on the instrument given my musical direction at this time. Will also make a great 'practice guitar' being some what 'acoustic' that I can take anywhere. To the uninitiated, it kind of 'looks the part, and I actually don't find the strat head to look too out of place and so used to them now with the straight string pull and such.
I might even use it as a test for some idea I had on multi tuning things built into the tail piece so I could drop easily to dropped D at least if not other tunings like DADGAD perhaps. The need to retune has tended to put me off a little, but in the fingerpicking genre there are lots of great arrangements.
Some of the influence of this is listing ot Pat Metheney's newer baritone in half nashville tuning that gives a very low bass and 'big sound' that is lacking in standard range instruments. Not quite sure how to do the alternate tuning things, this influenced by Adrian Legg's banjo tuner things and hipshot products...but I guess that would be 'step 4'. It certainly seems like and interesting project and one that will allow the ability to support a lot of different ideas while not being too 'precious'...a working trem while doable though, might be a little much ;-)
|
|
|
Post by 4real on Sept 28, 2011 11:23:23 GMT -5
Getting more enthused on this and taken the next step. Took things apart to provide a nicer neck from an old strat copy and looked through a few draws...need to do a little more searching about...
The guitar will need a bit of modding to get everything to fit nicely together, especially neck and body join. The end of the neck is curved so that will need to be cut into the top to fit, needs a 'shim' of at least 1/4" under it (lol) and the neck pocket slimmed down a few mm's too, but all doable with the neck joining the body at about the 15th fret.
Going for the archtop bridge now, so a more traditional look...means I need to make some kind of tail-piece to suit. The body is exceptionally light, lighter than an acoustic body so may need to add some weight in the tail end as I suspect it will be neck heavy, something to consider too.
For the pickup, I found an old gibson pickup that I found in a market years ago with a metal cover and a flame maple pickup ring that was not used on another project. As I will be cutting into the top bracing bars, this will need a little support at those points.
I am working on the bridge piezo thing. The bridge I have is a non-compensated rosewood thing. I might take the top half, jut that in half, route a groove for the piezo strip and glue back together. I have an idea of putting in separate metal rods that the strings will sit on that make contact with the piezo hidden in the bridge as there is no separate saddle that these systems were designed for.
I have settled on the piezo preamp system, it has a sizeable box that includes the battery under it and so a decent sized hole in the top side is required, cant think of another guitar that this would be a good idea in installing...but being plastic (lol)...and not being visible through the sound hole...plus it will mean there will be a decent sized access hole to get to the electronics and such.
I've still not totally got my head around the electronics components but I am sure john's ideas will adapt adequately when the time comes. The first step is to get the thing to play ok as an acoustic instrument, or perhaps with the mag pup alone and work my way up from there.
|
|
|
Post by 4real on Sept 28, 2011 11:39:18 GMT -5
Oh...and another thought, I looked up pitch shifters to see what might be available and found this for only $59... www.cranbournemusic.com.au/cstore/930087000486.html Could be an interesting toy to have and I assume it can handle polyphony and an octave down...anyone any experience with these things? It makes one wonder if a pup for the lower two strings is 'enough'...I kind of envisaged a control to fade in this little pup to add 'bass' but perhaps I should think 'bigger' and make a full on 'hex' pup, have a switch to select the number of strings selected and run the whole thing through this. Potentially you could create some interesting 12 string effects perhaps by doubling everything an octave up, or use it in 'intelligent mode' to double at various intervals within a key...interesting. Either way, seems to be 'affordable' if or when I get to experimenting with this kind of thing...hmmm
|
|
|
Post by 4real on Sept 29, 2011 8:12:03 GMT -5
Slowly working out the neck joint on this thing, coming along slowly but should be able to make a nice neat fit eventually so that the neck will look like it belongs and fit snug and at the right height. Cant seem to find the appropriate materials about the house, but I think I have found something that will do the job. Meanwhile, been considering the tailpiece. Cant for the life of me find the bits that I thought I had (will turn up after I have made an alternative no doubt). Since I look like having to make something, I thought I would attempt to flesh out some ideas for this tuning mod and run it by you guys and see if you have suggestions. As this is an arch top guitar, there is a fair height to the bridge above the board and a long way back behind the bridge to play with...so badly drawn in paint (new computer, no proper drawing program doh!) this is a thought... 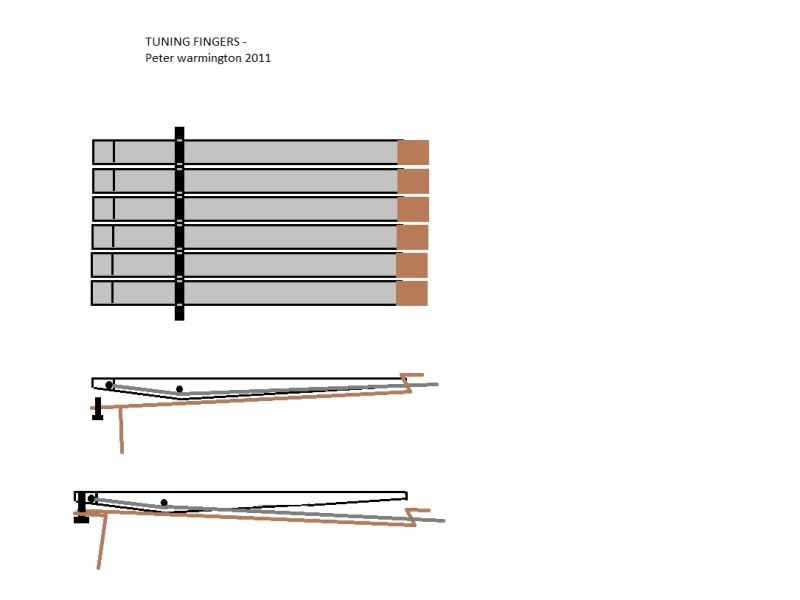 So, to explain...there are six "fingers", one for each string. They 'see-saw' on a pivot and probably an aluminium channel section to accommodate the string beneath it. These sit on a bass plate that is attached to the back (strap button) of the guitar in the usual style and overhang it a little. An allan key bolt is used to adjust the lower tuning, or throw of these fingers. The end features a 'catch' that springs and releases when pressed. The string tension provides the overall 'spring' to the mechanism. When pressed down and latched, this will bend the string over the pivot, hopefully enough to affect 2 semitones of throw. The lenght of the fingers should allow adequate leverage to bend the string, but I suspect too long and there will not be enough 'pull' so might be tricky. The effect then, is to have the guitar tuned to standard tuning with all fingers down and latched. If one were to choose, you could have all adjusted to give a tone throw down (though there are other possibilities). But in this scenario, you would have standard tuning with all down; release the low E to get dropped D tuning; release the low E, high E and A strings to get an open G tuning; release the low E, high E and B strings to get DADGAD tuning; release all of the fingers and you would get a kind of lowered baritone like tuning of standard a tone down. So, any thoughts, problems and such...approaches to making such a thing, materials to use and the like? Will the neck flex so it will need finer tuning regardless making it kind of obsolete? Perhaps there is some other mechanism or approach that might be considered for a similar effect. I have not really been considering this so much as a performance tool, changing tuning mid song or anything, though I suppose it is possible. This guitar though might be the best candidate yet for such a device, there is a straight string pull from the fender style neck (probably upgrade to locking tuners anyway) and lots of room and height behind the arch-top bridge, the guitar will be neck heavy anyway, so such a device back there will only help in that department. I do like things that are 'neat' and not look too DIY these days and it will be tricky enough to make one I think. Presently I ahve a few materials, some brass plate, aluminium plate and I suppose I could buy some more aluminium for the 'fingers'. I suspect that I will not have to 'pull' on the string much to realize a tone of adjustment. If you measure off from the nut and tune down a tone, I figure this is a decent indicator of how much the string will be required to move...a couple of mils at most. Similar mechanisms such as the fine tuners on a floyd pull the string in this way, but there is not the leverage on those bolts to practically move them by hand. EVH's D-tuna exploits this kind of thing though I am not entirely sure how I might do a similar thing without requiring an adjustment screw of some sort to control the 'throw' required. Anyway, would love a bit of feedback on how to make such a device practical...pete
|
|
|
Post by 4real on Oct 1, 2011 2:49:24 GMT -5
Making some progress on this thing...there are tricky things to do before getting to the wiring stage. Ordered some locking tuners as I do like them, GFS has some that look ok on a budget...sting me with the post, but they should work ok. If I am going to be messing with the tuning, I should trat this like a trem guitar and it certainly makes it easier to take the strings on and off a lot. Might try flat wounds on this guitar...less 'squeak'... ok...so a heap of things that I ahve yet to work out how to do...the bridge with pizo strip for an archtop...maybe some compensation for the scale...hmmm...and of course the tailpiece...and the electronics. ... 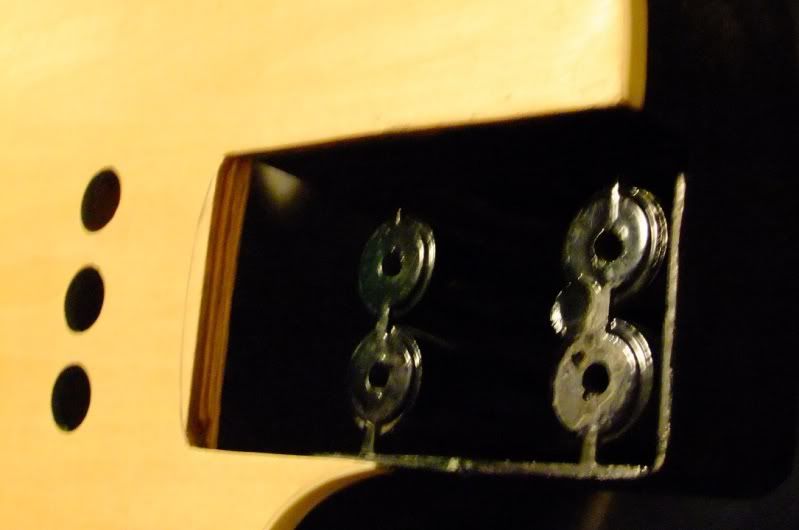 So...the above shows the plastic body's neck joint as it is...not built for the new neck at all...I reinforced the top with some tongue depressor things I got from a craft shop... 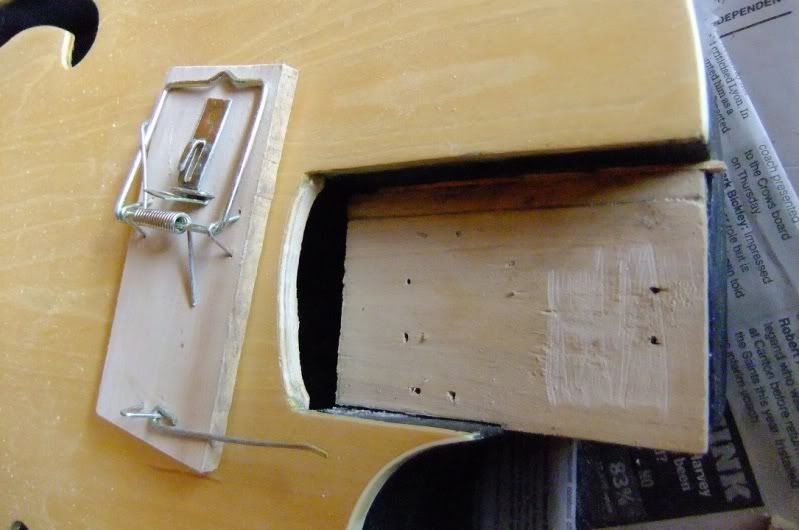 Above you can see the substantial neck socket plate...not finding anything great...turned out these old mouse traps have the right thickness...so for want of anything else...perfectly serviceable. 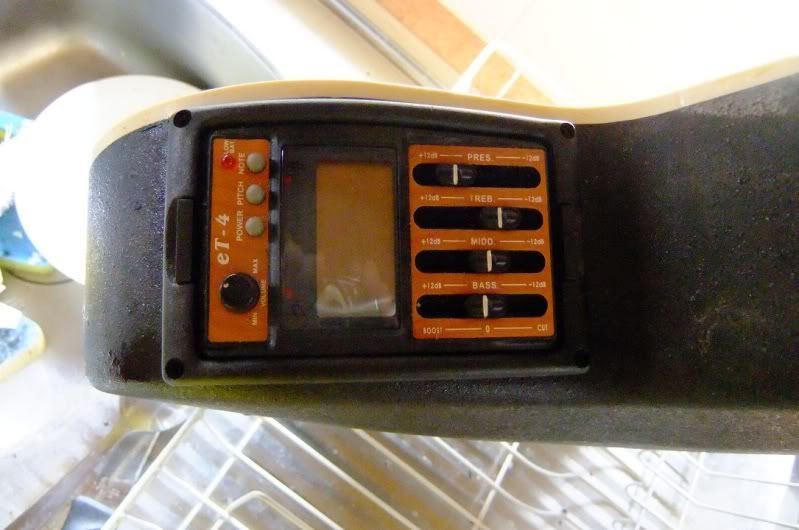 The piezo preamp tuner box fitted into the side...it's a little overly large, giant box under that...but it fits and cant think of another project it would be used for. It will not make the most of the sound anyway, that being the Mag pickup, just to give it an acoustic edge to the sound. Having an onboard tuner and a lot of space behind the bridge makes it ideal to play with tuning mechanism...and space inside to put the electronics required and experiment further... Ok...well neck setting at the moment, perhaps fit it and the Mag pup tomorrow...
|
|
|
Post by 4real on Oct 1, 2011 21:59:16 GMT -5
It takes a bit before a project gets to the wiring...but things like neck joints are very important...on this project the neck is completely different from the original and the neck socket built for it... Ok...so, yesteray after a lot of sanding and filing and shaping of mousetraps and tongue depressors...this was epoxied onto the plastic body. This morning I got around to the tricky part of drilling the approriate sized hole in the right place and in this case, the right angle as the new neck socket has quite a bit of a back angle so the strings will eventually clear the archtop style bridge. So, here are some pics of the end result... 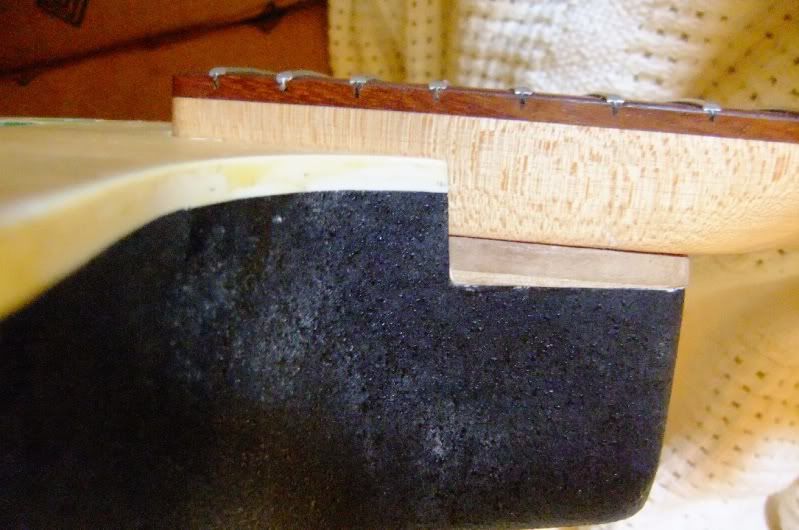 The neck 'plate' epoxied in with the significant angle and height required to fit this strat style neck into this pocket 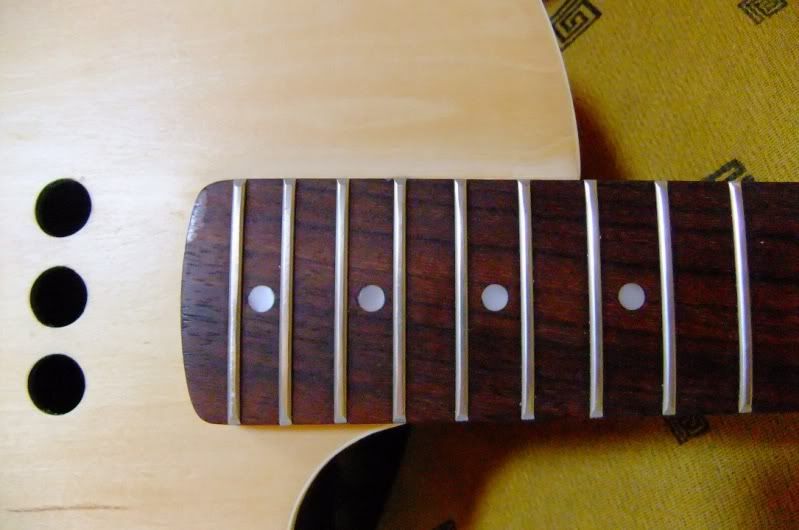 On the upper side you can see a 'togue depressor' shim carefully sanded and fitted to provide a perfect fit and support for the new neck...the wood is a very similar shade and once the final finish is on, should blend in pretty well there 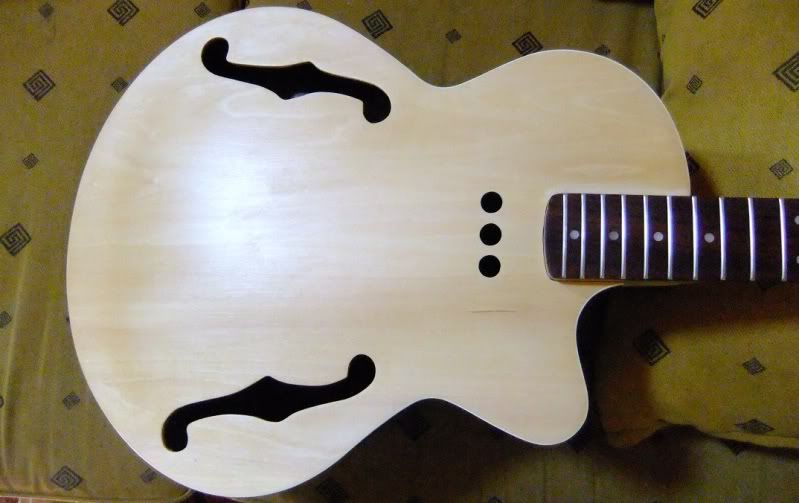 The end result is a nice tight fit, well screwed in (being careful to get the correct hole diameter and angle (used a drill press), adding candle wax to the screws and especially, to make sure the depth is at least as deep as required but short of the bottom of the fretboard. Mess this up and there is a chance of popping off the entire fretboard, go too far and one could drill right through! There are still some little inaccuracies there in the curve, these will be filled before finishing with a touch of plastic wood so it looks 'perfect' before finishing. The guitar will remain this kind of 'blonde' pine and the top is roughly sealed...another coat might darken it up a little, but I am actually going for a matt finish that will be perhaps a little 'lived in' in time...it is after all a plastic backed guitar. Despite the construction, I am not expecting much in the way of an acoustic sound, just enough to practice with perhaps....the gibson HB in the neck position and a touch of piezo will be the real sound of this guitar (requiring quite a bit of electronics and fiddling around to make a piezo style archtop bridge (still haven't solved that one as I would like some intonation compensation I suspect but the strip is solid). ... I took a trip to the hardware store this morning and got a couple of metres of aluminium channel 10mm wide for $6. This will serve to do something about a tailpiece and experiment with the tuning device. The bridge will be next though, a temporary string retainer will be mocked up for holding on the strings. That way I can align the pickup and cut that hole out. The piez system can then be tested on it's own and the mag. There will be a lot of active electronics in this guitar, but considering an aux direct out for the mag, just in case something fails and it can be used passively from that output. There may in fact be several outputs involved so it can be used in several modes. The bass pickup idea has kind of expanded too...will take some experimenting and only after all is playable, but after seeing how cheap one can get a harmonizer, it got me thinking of a range of possibilities. It might become a pickup per string device with some kind of mini dip switch perhaps to select which strings will go out. By doing this one could not only do the octave down on the lower strings (of choice) but perhaps do something like an octave up only on the high strings, creating an odd 12 string effect...not to mention the other effects one could add into this 'channel' only affecting tunings of choice. What I am considering is a small low impedance array of pickups (kind of like a syth pup) with a preamp to boost the signal and a switch that decides which of the six pups are on. It should easily surface mount, a bit like my sustainer driver, near or as a part of the bridge mechanism and be fairly stealthy. I am considerate of noise, but I am not that worried about the sound quality as anything that device would be used for would be to add a 'tinsel' to the basic guitar sound... Anyway, as always, one needs to start with a good working guitar that's fun to play...
|
|
|
Post by JohnH on Oct 2, 2011 15:55:27 GMT -5
The guitar is looking very sweet indeed. I read your description of the tailpiece idea -a couple of times - I think I finally got it. The principle seems fine and from what we've seen you do before, you are probably the one to make such a thing work. If I was building it (with my minimal metal work facilities), I would have a hard time making the latches work so they don't go 'pha-tang!' during playing. The stiffness of the fingers will be the key ie making them very stiff, and have the latching in the form of a sliding element on each finger rather than relying on the fingers flexing.
In case you are interested in 'prior art', the EVH D Tuna works on one string of a trem:
cheers
John
|
|
|
Post by 4real on Oct 2, 2011 16:58:01 GMT -5
Thanks john. These ideas have been floating around for a while and years ago I tried various ways of doing it, I have a strat type thing where the tuning mechanisms were built into the tuning block and was a kind of push button affair...but, so small and tricky to make and possibly unreliable..just to adventurous as an early prototype. The D'tuna is pretty neat, same kind of mechanism, I don't know how adjustable it is and you need that EVH down only trem thing to make it work right, probably his string guage (there does not seem to be too much adjustment in it). It does show that you don't have to move a string much, but there is a lot of pressure. The concept is more like a poor man's, slightly better looking ;-) and less invasive hipshot trilogy... store.hipshotproducts.com/cart.php?m=product_detail&p=35Although, looking at this version, it doesn't look too bad and $230...well, perhaps not my budget or for this plastic guitar. In this guitar, no trem and a lot of space for leverage and such. I redesigned it as I fell asleep last night, got some paper and pen and made notes in bed...so it is evolving to something...I moved the latch things to the rear so the fingers can just hover over the strings. I've worked away with aluminium sections for a while...light and strong, relatively cheap and easier to work. An inverted U chennel, 10mm wide and deep should be the right kind of dimensions...will allow the strings to run through them, the sides of the U section cut and filed to shape. Yes, perhaps something that slides and is sprung might be the go...good suggestion. I was having trouble thinking of a material that would be easy to work and be springy enough. A good cheap source for spring steel is a cheap scraper from the $2 shop. but it is amazingly hard to cut and wont take to hard bending without cracking...hmmm...will have to think about that, sounds like a reasonable option. The fingers will be a long way from the bridge really, but that might be a risk. The bridge is my next problem, the piezo element is a stiff straight length designed to go under a saddle on an acoustic...so tricky, especially if I want the guitar to intonate well...not quite sure how to proceed with that. Seeing the guitar together with the neck though and feeling it in my hands for the first time, the piezo preamp in the side...it is coming together rather well... 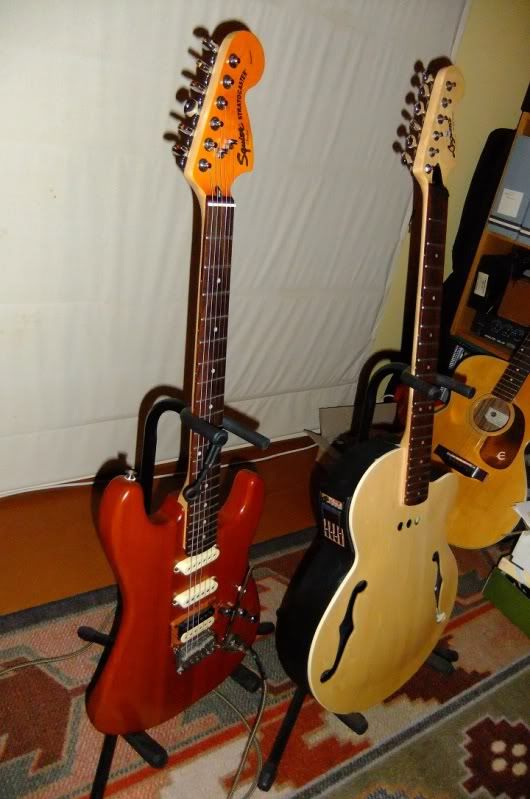 You can see that it is almost identical in size to my strat only thicker which can be a good thing...the better strat style neck (Legend was some kind of aria brand I believe and it is quite a nice neck to play) and with some mousetraps and all, is fitted perfectly and looks like it belongs. Have ordered some locking tuners, so they are on the way, might not need that string tree on the neck, so built as if for a trem. Thinking a string gauge of 10-52...might eventually try some flat wounds to stop squeak. I usually play 10-46 but the bass strings are a bit flexy for this new style of play, so perhaps something a bit stiffer and acoustic like. I found a nice jack socket, strap button part in my boxes, so that might make a nice direct out for the mag and hold the tail-piece on well. I suspect I will want to have a bunch of outs, perhaps mounted on a plate to provide better access inside and to tinker further with it. At this stage, really looking to be making a great playing guitar, but I can see the electronics side of things is fast approaching. The cover on the HB had been removed, so I might convert it to 4 wire, perhaps some kind of spin-split-tone control...but things are reasonably complex as it is. I think I will need a few of these buffer stages, one for the HB, one for the blender...if I do the extra Hex thing, some kind of preamp with gain...hmmm...not my forte. Having a tuner in the guitar though, that will be a fun thing and ideal to test out such a tuning mechanisim...but this bridge, hmm...be a shame if the tuning was compromised too much, it is kind of the point to be in tune after all...thoughts?
|
|
|
Post by 4real on Oct 2, 2011 21:35:17 GMT -5
A quick sketch of Version 2 of the tuning idea...some refinements 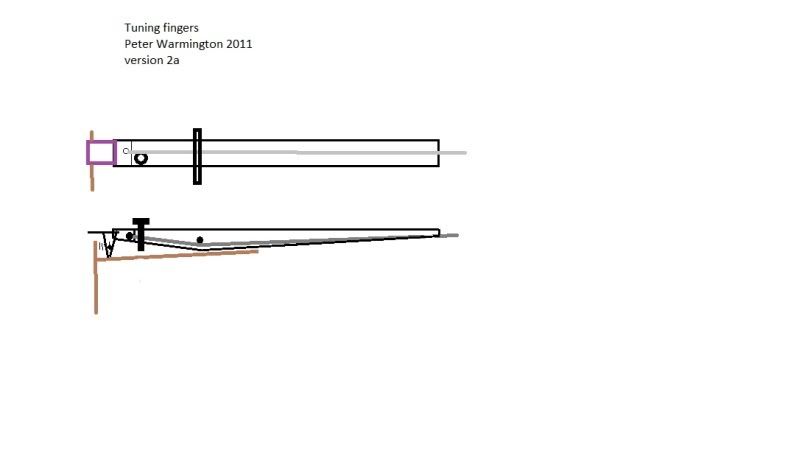 In this version, the locking mechanism has been moved to the back and the adjustment tuning screw set to one side (so as it misses the string beside it) from the top (so the mechanism no longer is required to sit over the edge of the guitar). This screw is to tune the lower note by limiting the 'throw' of the tuning finger. The fingers can hover free over the strings without a bass plate, making things smaller and easier to build...the bass plate in this version only needs to be able to support the axle and such behind it. Taking John's good comment there, I have thought perhaps a hinged catch might be better, with some kind of spring (this could be as simple as some neoprene rubber) to keep it in place. This means I can keep working in aluminium and not have to worry about complicated bends. I think such a mechanism could not move unless intended. By moving it to the back, these locks are holding the fingers 'up' from behind and the string pressure holding it down there. In the previous version it was trying to hold it 'down' and required a lot more strength and 'twannng' potential I guess. This would look neater, more reliable and smaller and is more of a 'winner'. Working out how to get the string in there and out still needs to be refined. I've not been able to work out exactly how much this mechanism will release a string, but taking fine tuners as a guide, something like this should offer enough throw...well...one hopes. ... The bridge is still a puzzle...seems my guitar all have different intonation patterns despite all having the same string gauges...hmmm Perhaps the best thing to do is to find some kind of thing to hold the strings at the rear...this will enable me to line everything up...the perhaps make a mock up bridge and use some wire and move that and the bridge around till I get the correct intonation...or close enough. Marking these points, then perhaps something will have come to me that will enable them all to sit on the individual piezo elements...then build a bridge around that. I am hoping to keep the original archtop bridge bass at least as it is well curved for the guitars top and looks good (rosewood). The height adjustment screws are too close together though for the piezo so it is likely to require them being moved further apart. Some more aluminium channel perhaps to make a bass that will span this without collapsing might be the go there...hmmm...it's tricky, have not found a bridge like it commercially or any stock compensation patterns drawn out with dimensions. The G string will be plain, so that is different from traditional acoustic bridges. I do note that most acoustic guitars have straight bridges (this kind of guitar benefits from being able to move the bridge about a little) and this might be easier. In fact, my kahler tele has almost a straignt pattern on it...a slight Z between the top 3 and bottom 3 strings.
|
|
|
Post by 4real on Oct 2, 2011 21:51:12 GMT -5
I found an old bridge that I had been working on years ago, will be savaging at least the SS axle rod in it. It also illustrates the kind of materials I will be working with (aluminium channel)... 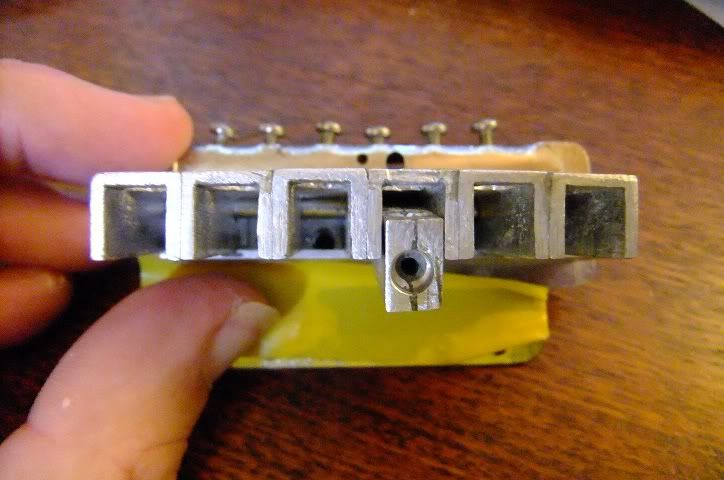 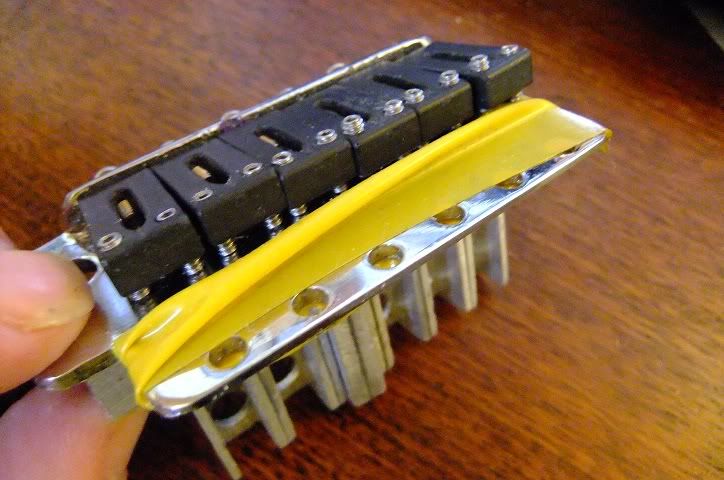 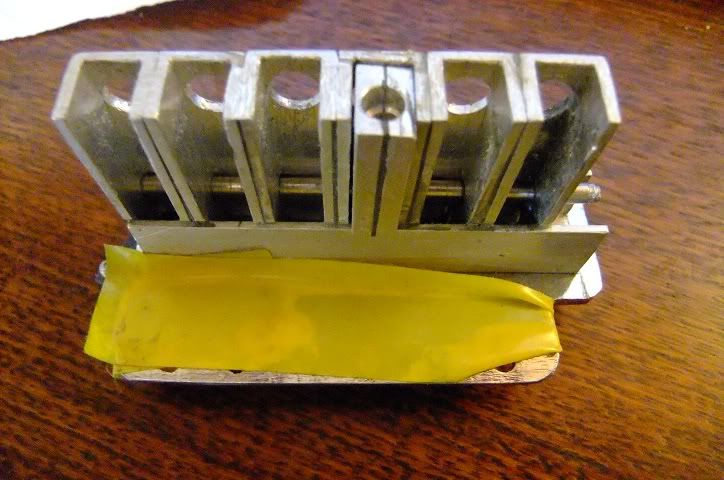 This had a weird mechanism that involved sliding a ball bearing behind the string holding mechanism...so there would be small push buttons just behind the string saddles. It was also supposed to work with a trem...so perhaps a little adventurous. It did provide enough throw, but the mechanism was tricky and might not have been practical or even work with the kind of precision I might be capable of. Having a working trem is just asking for trouble too...the changing string tensions might be a bit much...perhaps I was thinking that the trem would only dip down like EVH's... So, have been thinking about these kinds of things for some time, but this is the best chance to get it out of my system and on a guitar that can make use of it.
|
|
|
Post by JohnH on Oct 3, 2011 0:13:23 GMT -5
I've not been able to work out exactly how much this mechanism will release a string, but taking fine tuners as a guide, something like this should offer enough throw...well...one hopes. OK - its harder for the wound strings, because weight and stiffness are not directly related to the properties of steel, but for the plain strings - steel is steel is steel. Of the top three plain strings the first string is the one that will need the greatest length change to drop two semi-tones. My numbers tell me that to go from top E down to D will need a slackening of its length by 1.6mm. Maths are available on request if you wish. John
|
|
|
Post by 4real on Oct 3, 2011 0:22:26 GMT -5
Thanks john, that seems to correspond with marking the string at the nut and using a tremolo to lower the pitch also...not quite as precise and I may yet need some maths...have been having doubts about how much throw I will get out of this kind of simple leaver.
I need 20mm from the ball before it hits the axel/piviot point and so there will net be a lot of angle there. I considered a 'scissor' kind of mechanism, but this would reverse the 'throw' which makes it trickier...at least the first one that comes to mind...maybe somethig like that though would give leaverage without the 'finger' sticking up too far...bit like the mechanism in one of those adjustable vice grip tools...hmmm...
I might need to mock up a string (sounds like a high e is the go) to a tuner and a piece of pine and test one 'finger' before I get too...involved...unless there is something in the maths that can work out this kind of mechanism...hmmm...
It is though, only 2mm, a very small distance...must be a simple way LOL...thanks john, already your thoughts on the catch have made me consider an easier and better idea for it...
|
|
|
Post by JohnH on Oct 3, 2011 0:32:52 GMT -5
BTW, that calc was for a 0.01" string. (and EDIt: its only a 1mm movement needed for 2 semitoness) The other one that may need the most travel is the 4th string, because it also has a small wire core. You could make a quick check by taking a tuned up guitar, and seeing how much turn of the tuning machines is needed for each string to drop two semi-tones. Im guessing it is the 1st string but it might be the 4th.
J
|
|
|
Post by 4real on Oct 3, 2011 1:59:54 GMT -5
Ok...so got a little time to mess with a bridge idea...not as elegant looking (yet, at least) as the original...had to move the adjustment 10mm further apart so that the piezo element would fit in and a bit wider.
You can see the piezo strip there, below it the original wooden bridge piece.
I cut a section of aluminium channel down so it is very stiff and allows room under it to pass the piezo wire through the centre of the bridge plate. This kind of U section, even when cut down like this makes for a super stiff but light girder...a smaller section will be used for the tuning mechanism/tailpiece...All going well, the eventual "look" of the bridge and tail will match in some way.
I might be able to rig up something with this to work out where the intonation points should be if I string up the guitar temporarily.
Then I will need to find something to shape something nice in timber around it with this as the bass plate...I think i might be able to fins some small jarrah of cuts somewhere for a darker redish wood.
What I am thinking is to use individual saddle pieces for each string made of some kind of 'rod, that is guided to the piezo elements by a drilled hole from the intonation points...will be tricky, but provide an interesting 'look' all the same.
The aluminium thing looks like it might be something of a theme on this guitar.
This is one cool project, a little frustrating and is going to take some time, but there looks like quite a few 'innovations' will come out of it all. It looks to be one of the 'cheapest' guitars I have made, putting some use to a bunch of spare parts and amking a lot of the rest out of scrap and old mousetraps LOL
...
JOHN...thanks for the update, it corresponds to my guestimate and marking strings and retuning them,,,or messing with a trem. I still ahve my doubts as to how much throw I can get out of this particular version, I have plenty of time to continue contemplating things.
|
|
|
Post by 4real on Oct 3, 2011 4:36:59 GMT -5
Refining the tuning idea, getting a bit simpler and this is always a good thing KISS and all that... 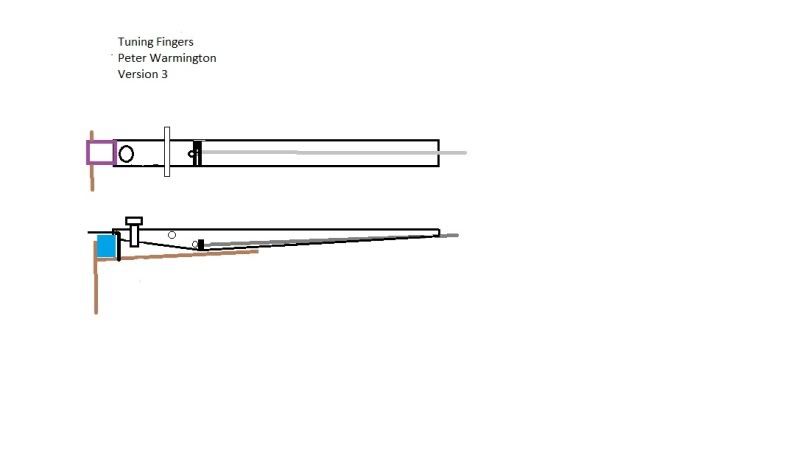 In this version the axle of the finger is moved to the top and the string anchor point is moved forward and hooked at the bottom of the lever. I think this will produce a bit more forward motion and lift the string up a bit as it swings. This also leaves the back end of the lever clearer for the tuning screw. The 'lock' at the back is a bit more refined and completely supported by some kind of rubber 'spring' so it wont move or vibrate unless it is pushed to release...at least I am confident there....hmmm I will probably incorporate some kind of 'damper' in there so that the strings behind the bridge doesn't resonate too much. The main concern is that there is enough throw...2mm is not much but it would be disappointing to do that much physical work to build this ting to just be able to put a guitar instantly 'out of tune'. Geometry is not a strong point obviously. Appearance wise, I am thinking that there will be some 'art deco' touches to this with a modern edge. ... Electronically, I have three matching knobs that will follow the aluminium scheme I think. I am still thinking a master volume, a mag piezo blender, (possibly and HB tone/split control...maybe mounted off the top) and ideas for the HEX device are still peculating and perhaps a control for that (a volume) might be a good idea. I might have to find a place for a dip switch or some other control (open to suggestions) to select what coils will be active. A likely place for auxiliary controls like these and a variety of output jacks will be on the lower back side, probably on a plate to allow better access to the electronics and internals. despite all the controls and pickups, tuner and such...I think that it still should look pretty 'clean' as has been my 'style' in recent times.
|
|
|
Post by 4real on Oct 4, 2011 2:28:32 GMT -5
Well, got a little bit of time to muck around with this thing...and mousetraps, is there nothing they can't do? 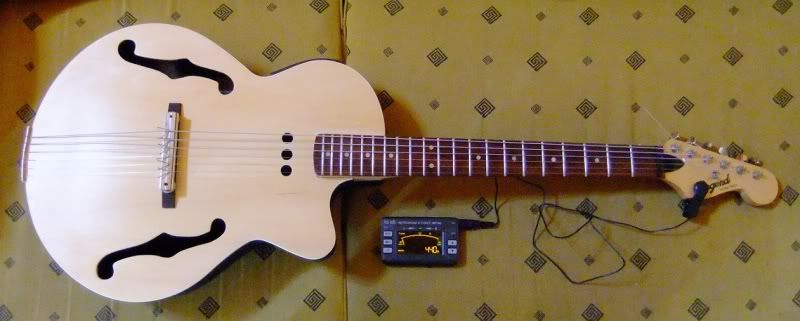 I made a temporary string retainer to hold the strings on the rear end. and glued a few mousetrap scraps to fit on the aluminium bridge plates...having moved the bridge pins apart another 10mm. 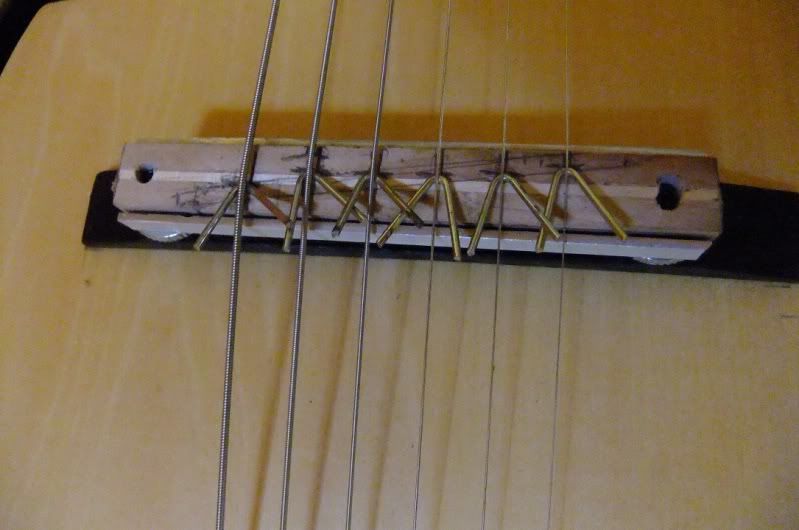 I used the wire staples from the mousetrap as bridge pieces and moved them back and forth with a tuner attached to the headstock. I moved the bridge pieces till it tuned open and fretted on the 12th fret...I was also able to test it on various frets and it seems to be good across the board. Then, marked the positions to establish this intonation pattern for these string gauge and this guitar. Not entirely accurate but most likely slightly better than the straight as is typical. 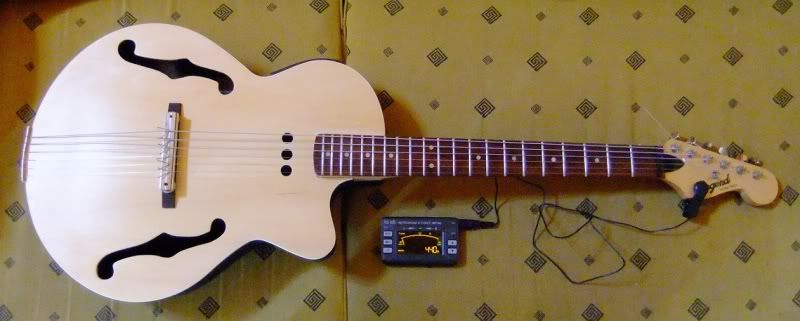 So today's 'progress'...can actually play the thing, very quiet acoustically but that's not really the pint and a propper bridge will hopefully improve things, not the 'sustain' of an electric but perhaps it's acoustic character will come through. Having the strings on allows me to line up the HB pickup...it's a bit wider than the string spread...and not at all lined up with those weird holes in that position...not sure what they were thinking there...it was advertised as a 'bluegrass guitar'...whatever that means. Having the strings on it may give me more of an idea of how to work out some kind of tuning mechanism, so they will likely stay on for a bit while I work out how to make the bridge too. For the bridge, I have in mind individual poles set on slight angles so that they land on the piezo element beneath which is roughly in line with these points. Most likely make a mock up with the mousetrap stuff till it's right and try and duplicate it in something better and sample it into something more attractive and comfortable. Not sure what the best material will be for these 'poles' I have a really tough stainless steel rod or some ABS plastic rod for instance...they need to allow the strings to roll over them without hanging up. So progress and coming along...
|
|
|
Post by 4real on Oct 5, 2011 19:57:49 GMT -5
The project at the moment... I've built a temporary string retainer and bridge, using some mousetrap scraps and even the staples to make bridge pieces to determine the intonation points... 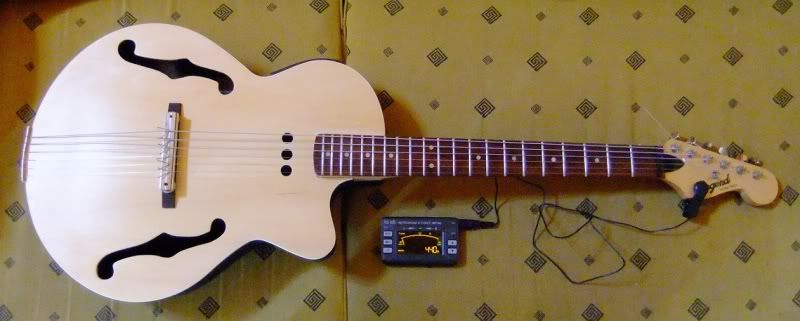 The thing is kind of playable in this condition and it works surprisingly well, not a lot of volume but enough to practice with, a nice electric feeling neck and a compact body that feels nice in the playing position. I'm getting used to the no frills look of the top without controls, the piezo system is built in to the side, but there will need to be controls...so... Was thinking, has anyone experience with thumbwheel pots and/or a supplier of such things? It would be kind of cool to hide such pots in the soundhole there. I am looking at three pots I would think, perhaps 4. One would be volume...so I can at least turn the whole guitar off... Another, the blend between piezo and mag Possibly a tone control for the HB, thinking about this one Potentially a volume control for the proposed hex system pup. ... For the hex concept. I was thinking of incorporating a tiny dip switch with six switches (anyone know where to get this kind of thing, or a pair of three?) so that one could select how many and which coils would go to a single output. The concept for this device is similar to the hex pups made for midi guitars...small and compact and unobtrusive just in front of and surface mounted, or possibly attached to the bridge itself. It will likely draw on some of my early hex sustainer ideas (I once tested these as a pickup and they did produce a signal, though would need pre-amping), small wound coils or perhaps modified mini transformer coils or winding them myself. I've expanded the concept from just doing an octave down on the ower two strings to being able to run any string into an effects chain like a harmonizer. One could perhaps use a chorus effect or delay only on the to string which might be a cool effect, so if having to build such a device, might have to go all the way with it! ... The bridge has so far been going ok, but is tricky... 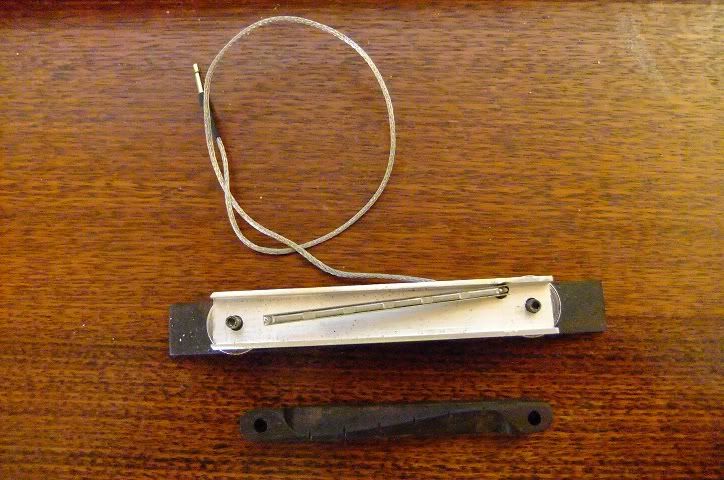 I moved the posts on the original bridge's bass plate to make room for the piezo strip on a cut down section of aluminium channel...the wire will pass through a hole under the bridge and into the guitar. 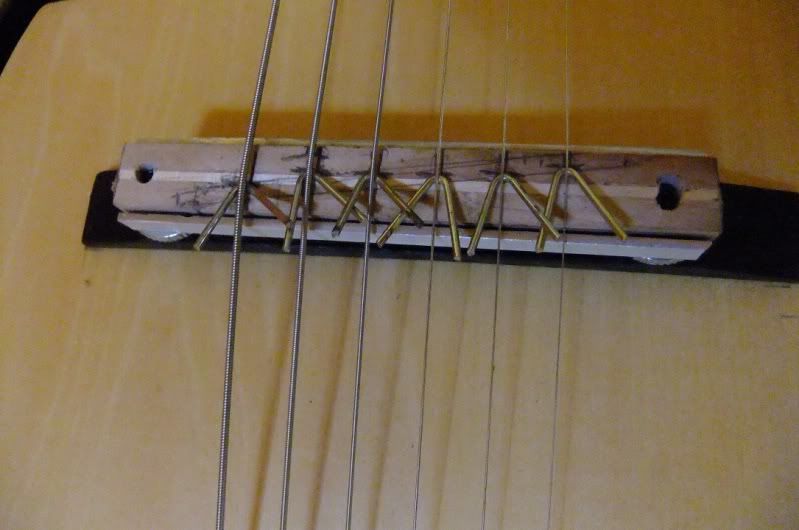 This detail shows how I found the intonation points, moving the wires till the intonation was correct (not quite the pattern I was expecting, but these strings are heavier than I would normally use. The trick is to find a way to have these points on the top of the bridge land on the straight strip beneath. Some kind of saddle material is also required. I was thinking these ABS rods I found in the Sunday market here on the weekend (10c for a packet of them). Otherwise I have some SS, which will certainly resist wear but I wouldn't want to risk string breakages or have the strings hang up with the tuning proposal.
|
|
|
Post by 4real on Oct 6, 2011 7:30:03 GMT -5
Not much work on this today...but a bit of thought... Back in 1977 roland came out with the GR500 guitar synth... 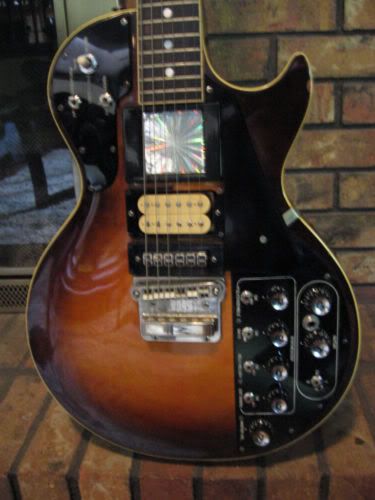 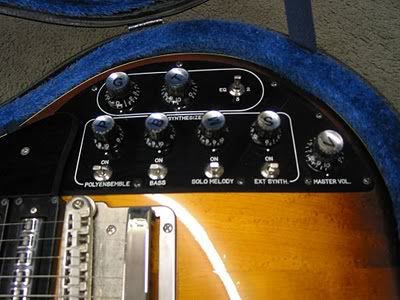 Looking at older technology can often be good for the basic DIYer some times. If you look carefully at that Hex pickup (before midi, this provided separate outs) these things were made from 6 tape heads! Got me thinking, cassette heads would be even smaller (this was pre walkman I believe) and available in abundance I imagine. Anyway...I think it may well be worth experimenting with. The output would certainly be low and so would require a preamp no doubt. With my idea, there would be a simple spst switch, one for each 'head' so that strings would be selected for a single output to be processed separately and 'shadow' the real guitars sound. Does this look like reasonable approach? If it requires the strings to be magnetised, this could be arranged with small magnets near by or set on the bridge in some way. A source for such components may well be those cheap car audio cassette adapters (I actually use one in my car) perhaps...that way one could assure a consistency of heads to make a prototype. While my particular application for this kind of thing is a little unusual, it does point the way to making other things possible perhaps...hex distortion or the like without having to even wind coils...these things should be pretty compact, so I imagine something could be built in to an HB enclosure perhaps for such an application. For mine, I will be wishing to disguise the thing to keep a clean look to the overall guitar...though it does have a bit of a steam punk ethic. I also found a few places where I can get thumbwheel controls in 500K log....is such a control suitable for the blender control? If successful, the electronics could perhaps be housed in some kind of shielded bok inside the guitar and affixed so that only a little portion of the control knobs are visible to the side of the lower F hole...giving the impression of an acoustic guitar even as it is filled with electronics of all sorts. I have the basic design idea for the tuning thing, but not having a workshop is holding me back a little there. The bridge needs to be completed and I have found that to be a bit tricky too. I found a bit of jarrah, but it is a very hard wood to shape into the bridge base and to fit the piezo strip and have the bridge pieces make appropriae contact while still being intonated correctly.
|
|
|
Post by newey on Oct 6, 2011 19:05:30 GMT -5
Between 1968 -1970 or so, Hammond Organ was marketing an early guitar synth system which I believe was 6 individual magnetic coils- (which is pretty close to a tape head anyway, come to think of it). Called the GSM ("Guitar Sound Modulator") it featured a modified Ovation Hurricane fitted up with a separate hexaphonic pickup over the bridge. The only good photos of the guitar, also showing the Innovex/Hammond "GSM" unit, were from this French site so some rudimentary translation is required: Condor GSM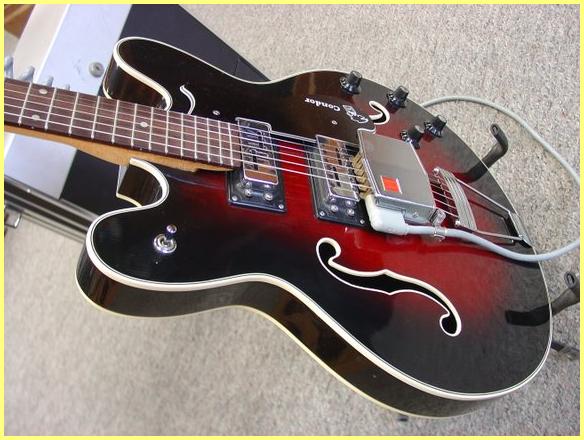 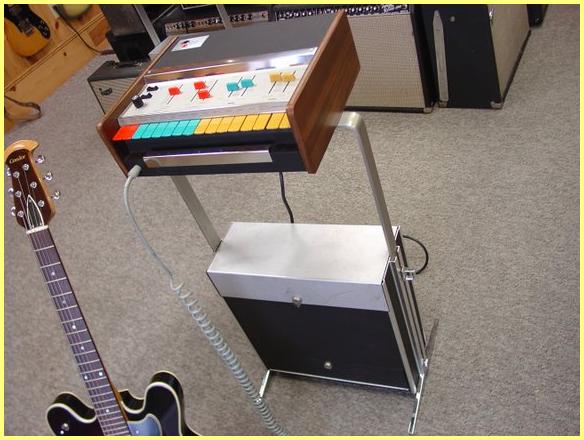 A friend of mine, lead guitarist in my middle school garage band, had one of these, so I played it a lot back in the early '70s. It made a series of organish-sounding synth sounds. The "sitar" was cool but sounded nothing like an actual sitar, but I remember the oboe and bassoon sounds were pretty good woodwind imitations. It also has a "2 string Bass" feature which made the 5th and 6th strings emulate a bass, while the four high strings were whichever effect you had selected on the other buttons. It could do multiple effects, too, but that stuff quickly got pretty noisy. But as you said, old technology might be good for some ideas. The clunky pickup cover thankfully was removable, and was the first thing to go back in the case, just like everyone did with their old Tele "ashtrays". And the hex pickup, as can be seen, had each string running through the middle of a looped coil of some sort, sort of like those "horseshoe" steel guitar pickups from back in the day. I recall that to get the action down to a reasonable level, we had to removed the TOM thumbwheel adjusters and set the hex bridge flat on the bridge posts' base. Also note the gray cable that connects the hex pickup to the synth unit. There was a separate 1/4" jack for the 2 mag pickups, so you could run into two amps as well. The synth unit was also a stereo unit as I recall. In those days, these were sold through Hammond Organ, who had a network of retail organ stores in the 1960's and 1970's. It was an odd fit for the organ salesmen to be pushing these units, these shops would be 90% organs, with just a few guitars hanging in the back, mostly Framus and Mosrite IIRC. They mostly sold console organs to old ladies. These didn't sell well and soon went off the market. I remember my friend got one at a great bargain after they stopped distributing these. The guitar was at least a decent Ovation, although labelled as a Condor, and he paid less for the whole thing than Ovations were selling for. AFter the synth unit finally bit the dust, my friend played the guitar for years with the regular TOM bridge it was designed to have.
|
|
|
Post by 4real on Oct 6, 2011 22:06:06 GMT -5
Thanks Newey, that's an interesting bit of history that I was not aware of.
I am guessing like many things this was always going to be a novelty and never really catch on.
The kind of hex thing I am thinking of is really for a particular and subtle purpose and style of play and used sparingly, so needs to be a bit discrete. I fossicked around yesterday for various bits and pieces including contemplating winding the coils, but for 8 bucks (for 6 including post), I dare say I can wait and see how these tape heads work out.
Still fussing over the bridge, a bit busy just now to work on it today and probably for the weekend. I have pretty much the tuning thing mapped out and hopefully will work ok. One problem is finding an easy way to string the thing up.
I am thinking of using neoprene dampers on both the headstock (when the locking tuners arrive) and somewhere in the tailpiece or bridge design to block out sympathetic vibrations. This is smething that is often overlooked. They advertise things like locking staggered tuners as not requiring string tree,s but this is a bit false. Without them these resonances can have a detrimental effect on the tone. My strat required roller trees and even my LP with kahler has rollers. The tele was the only guitar that really works without them because of the LSR roller nut having tiny dampers just behind the bearings. With this guitar there is a huge amount of string behind the bridge...on the high e, from the bridge to the end of the 6 in line tuners...it left little string left over in fact...that is a lot of string.
Anyway, those details will work themselves out eventually. If I had locking tuners on the thing, I'd have those strings off in a flash and be working on fitting the mag pickup and perhaps the bridge...but they need to be on a while longer while these things are planned out.
Hopefully next week I will get a bit more of the mechanical work done, perhaps strip it down and refinish it a little and get around to ordering some components for the electronics work.
I'm fairly convinced now that the thumbwheel pots are the way to go for this guitar, making the thing super stealthy...I can easily get 500K log pots I've found, but perhaps the blender would suit a linear better.
I'm considering converting the HB to 4 wire and using the tone control to also split it perhaps...will have to think about that...the parallel sound from my LP was very successful and might be a better effect and noise free. I have found a few slide switches and these may well also fit into the sound holes. I'm considering a power off switch too, as I tend to keep my guitars plugged in quite often. I might even have a power off to the hex things if I go that way because the preamp is likely to draw more power than one would hope for and is not likely to be used that often. I'm pretty sure that a lot of these things can be worked out and tinkered with over time...where as, if I drill a hole, that hole is forever!
|
|
|
Post by JohnH on Oct 7, 2011 6:03:36 GMT -5
Its all looking great!
i think thumbwheel pots could be cool - and I agree that a linear pot is what you need for the type of blender that I draw. 500k is a good value if you have a buffer stage after it, and I think it is good to have one.
John
|
|
|
Post by 4real on Oct 8, 2011 2:56:25 GMT -5
Thanks John...suspect I will need your help and other GN2'er's eventually with the electronic side comes up...even a lot of this stuff... So, got a little bit done..tedious work and I don't have a workshop thesse days splitting my work between 3 places and two flights of stairs...I guess it will get me fitter...LOL So... 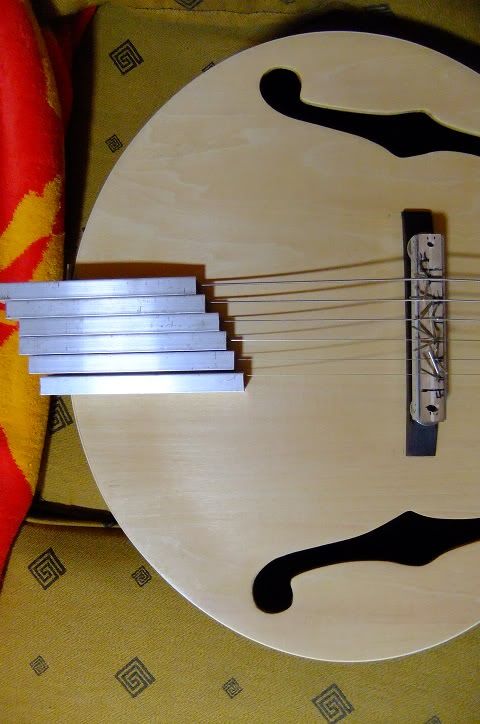 This pic shows a tentative kind of 'shape' to the fingers...kind of a familiar art deco kind of thing. This is purely aesthetic (an important consideration) but the high strings are likely to have a bit more tension so the leverage might be a good thing. 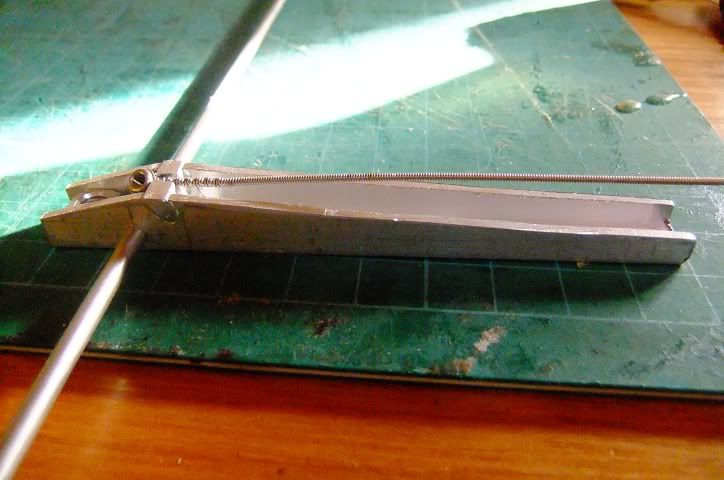 I pretty much made a prototype "finger"...the first one is tricky, this will be used as the template to make the final 6. You can see that this is made from 1.5mm wall 10x10mm aluminium channel. This make it very light and thin and allow the string to fit inside and provide a nice shiny finish that will age well. There is an angled piece held by the sides (eventually epoxied in) for the string. I expect to be able to string the string by lifting the 'finger' to the fullest extent and inserting it in that slot. This should hold the string in well enough under tension. The axle is a 3mm SS rod, quite stiff and strong and will wear well. Behind this is the quite large (5mm) adjustment bolt that will tune the throw to the lower note. I elected to use a steel nut cut to fit the channel. You want this to be string and not move with vibration. They will also work as fine tuners when tuned down if required. So far so good, I am hoping that it will provide enough throw, it seems to be just enough (about 2mm) and perhaps they can be filled down to give even more throw on the strings that might need it. The platform that holds it all together is in mind, but yet to be fully planned out. Then there is a piece that will hold it on to the actual guitar. I'm thinking of using a strap button/output jack which might be the direct out for the mag pup in case the electronics fail or something...good to be prepared. Perhaps I will want to run things in stereo...I am kind of thinking of having multiple output sockets for various options perhaps...or some kind of switch... ... I am kind of liking the idea of the thumb wheels, it will certainly give a nice appearance that it is an acoustic and that can be a good thing. I've ordered some tape heads to see how that might go, but that is an add on thing after all is done with the guitar...and perhaps may not work, so not banking on the things.  An interesting thing that I found is this "power gig" guitar controller, they seem to be going relatively cheap...but not down in. This has a standard sized hex pickup in it and might be of interest...shame one can't just get that part, but I suspect there will be second hand ones about soon enough as the game seems a bit lame!~ Not sure what those metal pieces are next to the coils...you see this a bit in hex pickups of old. Perhaps it helps focus the strings to the individual coils or are there to magnetise the strings. I am anticipating doing something similar and hopefully more compact and not noticeable. I'm not expecting a great sound even, though I would be concerned about noise and hiss, in my application this is just to run a sub bass or some kind of doubling in the background to make for a 'big' sound and more range for solo guitar stuff and only on selected strings. The bulk of the sound will come from the guitar itself and anticipating most of this to be from the mag pup. It could make for some interesting arrangements, using capos and preserving the bass and adding range to a style that is restricted in range
|
|
|
Post by cynical1 on Oct 8, 2011 10:18:26 GMT -5
I like the design for your tailpiece. Now that I see it I like it even more. I've always had a weakness for Art Deco designs, and this got a sincere "whoa, cool" when I saw it this morning. One point I would make, and it's from the heart, have you considered the effects of Galvanic (dissimilar metals) corrosion? Long and short of this is it's the oxidation and premature failure of designs due to dissimilar metals being put in direct contact with each other. I saw this all the time in the packaging industry...and they employed degreed engineers... What happens is you place two metals in direct contact with each other and you witness accelerated oxidation or corrosion at the point of common contact. I looked up the engineering details this morning, as I haven't had to deal with this in decades. The criteria widens depending on the environment the device or assembly is put in, but in a normal to controlled environment the span is still somewhat broad. The Cliff Notes on this are based on what's called the "Anodic Index". Every metal has a rating on this index. The balancing act comes in when you mate these metals in their environment. Here's the skinny in a chart. METALLURGICAL CATEGORY | ANODIC INDEX (V) | Gold, solid and plated, Gold-platinum alloy | 0.00 | Rhodium plated on silver-plated copper | 0.05 | Silver, solid or plated; monel metal. High nickel-copper alloys | 0.15 | Nickel, solid or plated, titanium an s alloys, Monel | 0.30 | Copper, solid or plated; low brasses or bronzes; silver solder; German silvery high copper-nickel alloys; nickel-chromium alloys | 0.35 | Brass and bronzes | 0.40 | High brasses and bronzes | 0.45 | 18% chromium type corrosion-resistant steels | 0.50 | Chromium plated; tin plated; 12% chromium type corrosion-resistant steels | 0.60 | Tin-plate; tin-lead solder | 0.65 | Lead, solid or plated; high lead alloys | 0.70 | Aluminum, wrought alloys of the 2000 Series | 0.75 | Iron, wrought, gray or malleable, plain carbon and low alloy steels | 0.85 | Aluminum, wrought alloys other than 2000 Series aluminum, cast alloys of the silicon type | 0.90 | Aluminum, cast alloys other than silicon type, cadmium, plated and chromate | 0.95 | Hot-dip-zinc plate; galvanized steel | 1.20 | Zinc, wrought; zinc-base die-casting alloys; zinc plated | 1.25 | Magnesium & magnesium-base alloys, cast or wrought | 1.75 | Beryllium | 1.85 |
[/TBODY] [/TABLE] While I don't know the exact metallurgy on your components, I highlighted the ones that might apply in red. So, why is any of this important? Here's why, according to several sites that put in more succinctly then I: "Normal environments, such as storage in warehouses or non-temperature and humidity controlled environments. Typically there should not be more than 0.25 V difference in the "Anodic Index". Controlled environments, such that are temperature and humidity controlled, 0.50 V can be tolerated. Caution should be maintained when deciding for this application as humidity and temperature do vary from regions."Plating common surfaces is one way around this. And a chrome plated CR steel rod will be stronger the a stainless steel rod...just for reference. And SS square tubing can be machines or bandsawed into a channel. Watch the I.D. and O.D. of the tubing and it will fit together nicely. We used it in actuator assemblies all the time for the food processing industry. Finally, SS polishes up much nicer than aluminum. A polishing tip on SS, aluminum polishing rouge compound polishes stainless better then stainless polishing rouge. One pass across the web of the channel and two passes with the web and it shines like a mirror. But after all that, I really like your design. It think it mates form and function very nicely. Very clever. Happy Trails Cynical One
|
|