|
Post by 4real on Oct 8, 2011 16:40:49 GMT -5
Thanks C1...yes have considered it and experienced it too. Aluminium like this will always oxidise giving you that dull sheen evidenced by the raw parts there.
As to mixing materials, it is kind of a necessity...the strings are steel while the fingers are aluminium...this and the salty air I live in might be expected to have some problems, but I suspect that I'll change the strings often enough not to have anything 'eaten away'. After all, bigsby tremolos are often aluminium.
Mainly, I need a good light strong material that is easy to work and cheap...aluminium is great for that kind of thing.
If you see that strat type bridge pictured above, I built that about 8-10 years ago and has been sitting around in a box without any protection for qyite a bit. The aluminium is attached to the chromed steel bridge piece, the axle there is the same SS rod I will be using here. There is no sign of oxidization there.
I am proposing using fine brass washes between the 'fingers' at the axle so that they don't rub against each other...yet another metal that could turn a little green.
The hardened set screws could be a problem, you don't want the threads to oxidise and get lose, vibrate around or detune while playing...or just fail! Hence, adding in the sizeable matching material nut into the channel. This will be eventually epoxied in (providing some kind of barrier between materials) and give a bit of support to this crucial set tuning screw.
I think I have catered for strength and solidness. I upped the string retainer for instance to a 3mm chunk of metal that goes the full depth of the 'finger' and half set into the sides and angled to retain the ball end under pressure and with movement.
Unlike a tremolo, these things will not be in constant motion, unlikely even to be used within a song (I still retain some skepticism as to their accuracy, the upper standard tuning should be stable (I have yet to settle completely on the rear 'latch' design) but the lower one may need some 'tweaking' The oversized set screws though will provide for some fine tuning without affecting the latched standard tuning, so this should assist in not having tedious tuning sessions between tunes that always screws with your performance (possibly why I never explore such things as a rule). The tuner in the guitar should help there too...just in case.
But structurally, I don't think there will be any problems...unless I were to paddle out to see in the thing!
....
I'm getting kind of excited about this thing, even as I work through the options of having it work through trial and error.
Glad you like art deco...this guitar is definitely going for a modern neat but slightly 'steam punk' kind of vibe to it (al little oxidization on the aluminium will just add to that kind of 'futuristic history' kind of thing.
The sketches are in advance of the project, but things change when working out ideas from scratch. The have to function but also be ergonomically and aesthetically pleasing.
All my guitars have a tiny bit of tortoise shell material on them. This one looks like it will have more of that vibe (the black plastic back already has a kind of textured Bakelite vibe to it). The catches that will hold the fingers 'up' in the back will have this material on them, probably the side pieces at the rear that will hold it all together will have a similar vibe.
I'm kind of glad that I stopped work on the bridge for a bit. I had really 'committed' myself to this one design and had been kind of forcing it to work...possibly not a good sign. I took a day messing with making such a thing and it was getting harder and harder to 'make it happen'...
So last night after working this thing, I am thinking a whole new approach that will have a very similar kind of vibe to the tail...aluminium and tortoiseshell.
The best I can think of using for the saddles now is more aluminium...not the hardest wearing of materials but again easy to work and I've seen guitars use such materials before. Perhaps it will require cleaning and a bit of petroleum jelly ;-) in use (I tend to oil my strings and fretboards against corrosion these days anyway...kind of relates to the 'wash your hands' thread).
The trick is to make something that intonates properly, as this is hugely important for this style. They won't be adjustable (other than to file off the leading edge a little, and slightly move the bridge about). With my experiments with the mousetrap bridge, I have located pints that seem to be pretty accurate and it certainly plays better than most acoustics with a straight bridge in this form. How it works out when I have the correct radius...well, there might be a bit of tweaking there.
So...the end 'concept' is something that looks 'natural' and not 'out of place' a bit old time futuristic relic, kind of a cheap vibe but with far superior functionality. So, the plastic back, the arched top, the fender neck, the thumb-wheel controls, the side tuner/preamp, the natural rubbed matt finish of the top...the old authentic gibson HB's cover was gold but significantly worn down to a dull nickel...the tailpiece idea and style...should all form something functional and have that kind of vibe where things don't look out of place and this is the kind of guitar that has been around for decades, yet never existed...or so I hope.
Even the tape head pickup if it comes off should add to this. This will be small and close to the bridge, the casing built of wood the colour of the top and not look like I'd stuck a midi pup on there. I'm not relying on this working, nor would use it al the time, but the idea is kind of cool so it is worth playing around with. however it turns out, there is plenty of space above the top to surface mount any such device as well as test it without any modification. I will make a discrete channel under the bridge to allow the wires to pass into there and down the piezo systems wire in anticipation.
The intention there is to put tiny DIL switches into the actual pickup to select which of the heads is connected to the separate mono output and effects chain. A single volume control will control how much loud this signal is in relation to the rest of the guitar. I am aniticipating this to be kind of subtle.
Like a quiet string bass doubling the lower strings, or a light higher octave above the melody...obviously there are other options, like a bit of a tremolo, chorused, delayed or even distorted sounds on selected strings if I wanted to go that far. I already have some cheap digital effects that could do this job and more so it is definitely worth experimenting with. Perhaps someone will take the idea further, maybe I will myself some day to make something midi compatible.
...
Anyway....the project is taking a while and evolving as it should, working out even better than I anticipated. The whole "vibe" of it relates to my musical direction and audience anticipation. To your average person, it will look like a fairly basic but classy old instrument, pretty much an acoustic. My strat does a decent job in with this style, but the 'look' of it...the idea of a solid body even, seems to throw people off.
There are a lot of acoustic pickers working in this style already, Tommy Emmanuel is a classic example of this, having put his telecasters aside to reinvent himself as the new acoustic Chet Atkins (no offence to Tommy, nor to Chet). I'm looking for a more 'jazz' like vibe but accessible arrangements of modern classic songs. This kind of 'future retro' instrument I think will be up to performing the task and give the right 'impression' and marry the instrument to the whole 'solo guitar' feel and look of things.
I guess what I am going for musically, and with this instrument (which by the way, matches the look of my silver-faced fender amp very nicely) is a sort of "pianola thing"...you know, contemporary songs picked out with melody, harmony and independent bass lines (the hex things would highlight this effect especially) but with a bit of a non-offensive MOR sensibility that you could appreciate as background music or as a 'concert'.
It will take quite a bit of work to get all that together, but the anticipated venues would be restaurants, wineries, seaside/street-side cafes, local art galleries, sunday markets...that kind of thing. If that works out, perhaps I might add a singer, but that ups the anti quite a bit as then I'd be needing a compact PA and split the profits (when there is some distance involved, you got to consider petrol money ;-)).
There is just something cool about the idea of walking into a place with a guitar and amp and just playing without a lot of fuss.
But besides that, this instrument should be pretty bullet proof, great for taking with me when away from home, makes a fairly decent if quiet acoustic sound for practice and such. The set up is a bit different from my regular guitars, heavier bass strings, but still have an electric feeling neck.
The whole thing is a bit of a custom 'concept' guitar, but I have the ability to at least make another should it show promise and perhaps do even better with the next one. Knowing what is needed would certainly make things move a lot faster, at the moment the majority of time is being spent coming up with alternative approaches, sketching of mocking up ideas, researching possibilities and supply of components, waiting for them to be shipped in as required...all that kind of thing.
Thanks for the interest though, it is turning from a fairly basic idea into something quite unique and special I feel. The electronics side of thing, the possibility of excessive noise and such is a concern. A buzzing electric instrument would for sure spoil the whole 'illusion' that it is trying to create I feel.
I seem to have those basses covered and coming up with a few more 'twists' to help with that, but the proof will be in the end result and I've not had much experience with active electronics in the guitar signal. This is not a guitar that you could 'shield' so everything will need to be done with shielded cable and perhaps housed inside some kind of small aluminium grounded enclosures hidden inside some how.
|
|
|
Post by 4real on Oct 9, 2011 16:20:05 GMT -5
Here's a quick pic that might have people thinking of possibilities..though of course it might not work or sound a bit...well...crap, who knows... 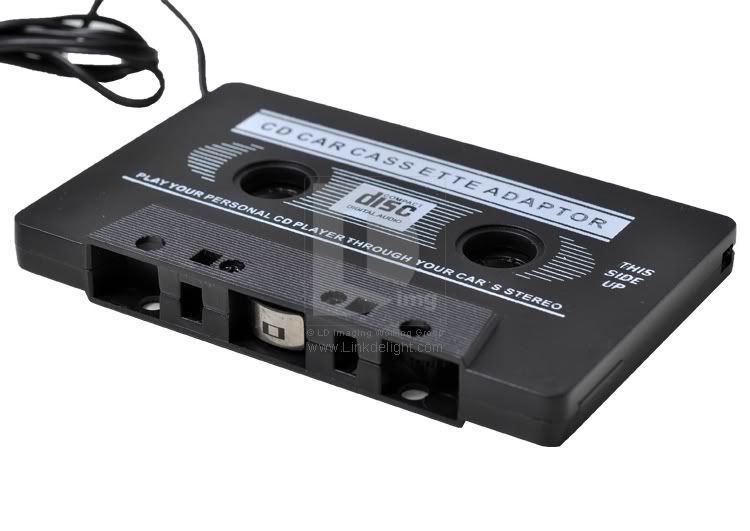 A cheap consistent source of tiny pickups...cassette heads! Obviously they will require pre-amping as they are low impedance and probably a way to magnetise the string just above them...but I believe that they will at least produce a 'signal' given that is their purpose and set right next to the bridge the strings movement is not so wide nor the alignment change. Untill I actually get them in hand, I cant even be sure of the dimensions either...but measuring the head in my cassette player here, it appears to be 11-12mm wide...happily just about exactly the distance between strings at the bridge of most guitars so they just might fit perfectly...stranger things have happened LOL.  How one might combine them in various combinations, optimise sound quality and keep them noise and distortion free and generally produce a simple device is yet to be seen. I have a couple of cheap digital effects...zoom and korg things...these can do quite a bit in terms of processing like basic harmonizing, compression NR and eq as well as the general range of effects...the korg AX1G has in particular a very convincing tuned sitar sound btw. So, while the signal out might sound a little 'plain' the power of these quite inexpensive devices these days may well be able to create a decent effect, especially in my application which is to shadow the guitars original signals (adding depth and variety in the background) of selected strings. ... So, this week...it's on with the tuning mechanism and bridge...this will allow the strings to come off and the pickup fitted, the piezo and such fitted and those kinds of things. I think this morning I have finally found a good way to construct the bridge, almost entirely out of aluminium which will be interesting to see how this will sound and wear. It can be a good idea I think to let ideas sit for a bit and contemplate other option than that 'pet' idea one started off with. It's a tricky thing making whole components from scratch like this rather than something 'off the shelf' but it is kind of the only way here if I want piezo and intonation and fitted to this kind of guitar...and relatively cheap. Fortunately I have been able to scrounge a few bits of material here and there from my boxes of scraps. The idea about the bridge is to maximize the string sound and not the top and handling noise...as John has shown, you can get quite a good sound out of the piezo buzzer, but they do tend to pickup a lot of the body sounds (which might be a good thing) while these under saddle things should pickup far more of the actual string saddle vibration. Well, at least that is the intention. At the very least the system should provide access to an onboard tuner and produce a sound and a handy battery compartment. The box for this unit is silly big and I may in fact be able to locate some of the electronics inside it to keep things neat and accessible and close to the power though, it is likely the way John has devised these preamp modules they would be better located right on the pots themselves rather than having wires going everywhere...not to mention the difficulty of getting things inside the guitar and if using thumbwheels..not being able to just screw the pots in place...hmmm
|
|
|
Post by 4real on Oct 10, 2011 2:12:49 GMT -5
Ok...well a little progress today...this stuff takes hours and a few false starts...but getting there. Today it was working on the bridge, this (like the neck socket earlier) is a crucial element in the way a guitar will play and on this guitar everything is pretty custom. If one could just buy an appropriate bridge that could adjust intonation that obviously makes everything a lot easier... So...some pics then.. 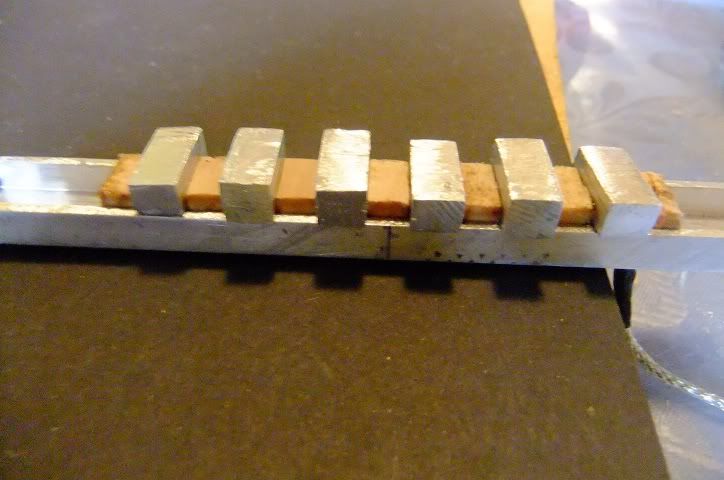 I started adapting the bridge plate I was using...then realized I could do better than try and fix the slight faults and start again...much better. I decided/dreamed of using some 6mm wide aluminium as the saddle pieces since I found a few inches of the stuff, cut off from when I built a boat many years ago (there is a lot of little things like that in this guitar)...After much measuring and considerations I determined the spacing required to be 5mm and as luck would have it, this is the thickness of my mousetrap wood...cool, easier to work than aluminium...you can see the aluminium used to perfectly space the pieces. The piezo was lined up perfectly and angled to be roughly in line with where the strings should land above. 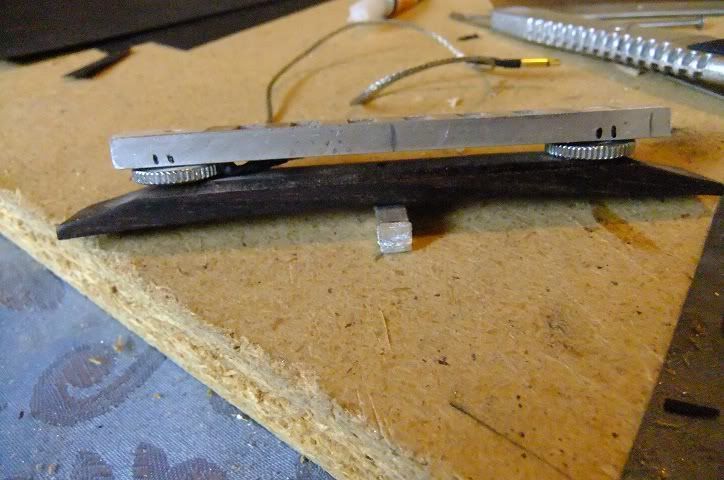 Here is a side view mounted to the bridge plate. By using this aluminium channel I can create a very stiff structure and space below for the piezo lead...this will eventually be hidden below exiting through a central hole into the body. You can see the piezo element diagonally under the spaces, this was wedge in place with thin strips of wood (thank goodness for tongue depressors...the perfect height) that leave the 'bumps' of the piezo a little proud of the bottom there. ALl this stuff is held in place with a bit of superglue and fitted reasonably tightly. 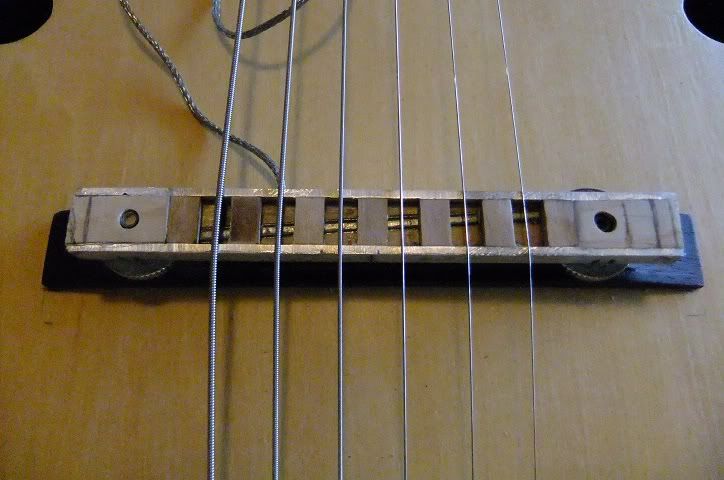 I had to widen the space between the bridge posts to fit the piezo clear of the height adjustment screws..the individual elements on the piezo had to line up perfectly...this is a little wider than your typical electric but for various reason I want to maximize this spacing and it does fit quite well. With finger-picking styles, it can be good to have a bit more space between the strings under the right hand. I might eventually replace the bridge to maximise spacing at that end...my tele is like that. For some reason asian copies always have fairly skinny necks...go figure. Even a squier is about 2mm narrower than a legit fender...who knows what the standard is in mexico. If I ahd my way I'd have guitar made with an even wider neck, but that's me...long fingers! I also measured the width of the cassette head in my deck and it is exactly 11mm wide...so they should fit perfectly if that experiment works. Poking about downstairs I finally found some of my strong rare earth magnets which should be ideal for what I have in mind for the hex thing...but it will be useless if the things wont fit under the strings or have to rebuild a bridge that takes two days to build again and risk the piezo...planning can not be underestimated...but I think I have all the bases covered so far. ... 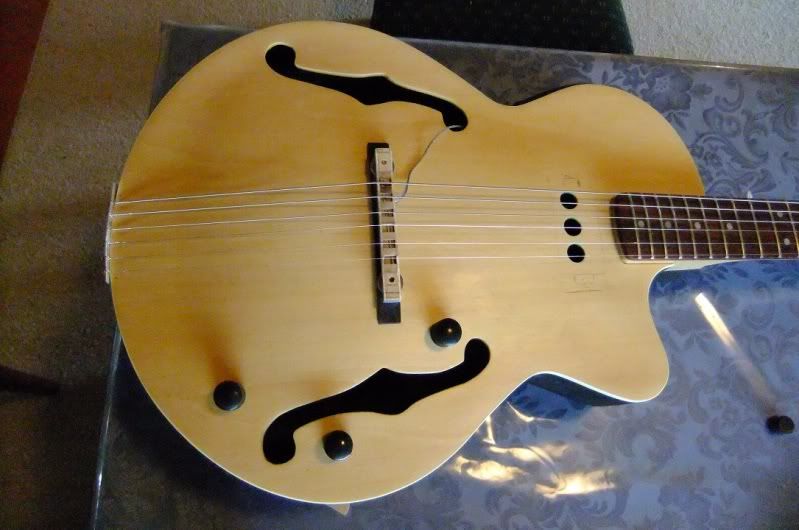 So, the whole guitar with the strings lined up and...look what I also found, these very classy looking black chromed tele knobs...where did they come from...and three of them...hmmm Although the thumb screws are a cool idea and still exploring that option, I don't think this looks half bad (matches the black plastic back LOL)...opinions anyone? I have been thinking I will wire this old HB to 4 wire and hide a hidden series/parallel switch in there since the parallel sound on my LP worked so well (a bit of a lighter sound) and perhaps a thumb-wheel control for tone to darken things up. I actually use the tone controls a lot these days and this guitar I suspect will be naturally very bright and certainly I am expecting that from the piezo system...so being able to darken the electric sound I think will be important to the versatility of this instrument. So, I have a piezo in a bridge plate and the strings seem to line up well. The strings will each sit on their own slotted aluminium pieces that will be filed to radius and back to the guitar intonates perfectly. The bridge looks a bit 'industrial at the moment, but it is at least perfectly lined up and a workable unique solution devised. Under the screws is quite a bit of aluminium block, the wood is very thin on top as filler. all these wooden mousetrap bits will be covered with tortoiseshell that is quite dark and will match the kind of color of the rosewood below and set off the aluminium...and of course shaped to suit the eventual look of the thing. The plastic will also feel a lot better than cold aluminium. If the hex idea works and is small enough, it might even be able to be attached to the side of this bridge system so it will ride with the action adjustment...I suspect that the heads will need to be extremely close to the strings which is fine if very close to the end of the strings...if not, well I have a plan B regardless LOL. Building the bridge like this will help I think in the construction of the tuning mechanism which will likely be similarly tedious even though the first template for them and general idea is mapped out. Like the bridge, there will be tortoiseshell highlights on the catches and side ices so the two should match well and give something of a vintage vibe. ... OK...so that's it for today I think...best to have a break and come back to it before I shape it and make the bridge pieces which will be kind of tricky. The bridge pices will be a slightly looser fit and slot in and glued with PVA over super glue. This will not only allow possible removal and adjustment as needed but a bit of 'spring' so that the vibrations are transmitted to the piezo below. Although there is a bit of 'wood' in this, the piezo element actually sits on the aluminium base, so the entire string to piezo and below is metal. The whole project is going pretty well I think and getting better all the time. It is always a bit nerve racking as things progress, the mistakes that can be made could destroy a vital component (like the piezo) or some other 'bad decision' (the old bridge plate was a little short...this one I made slightly longer to have a little play with it). I'll be really glad when I get to cut out those holes where the HB pup goes, I have no idea what they were thinking there, but they do detract from the look of the thing. My old gold HB should look great and I have a flame maple PUP ring from JG that will blend right in with the colour of the blond top.
|
|
|
Post by 4real on Oct 10, 2011 5:30:24 GMT -5
Well, as the sun has set here, 'construction work' has had to stop for the day...possibly a good thing as I keep finding ways to refine the ideas... But, it is probably time to start thinking about the electroncis side of things. I've just been reading the 8 pages of adventures over here... guitarnuts2.proboards.com/index.cgi?board=acoustic&action=display&thread=4567&page=8Looks like treguiers, JohnH and the rest of the nutz did a fantastic job ironing out the problems there...which hoefully will have save this project a similar fate. The end result seems to be these circuits... guitarnuts2.proboards.com/index.cgi?board=schem&action=display&thread=4595In many ways the scheme for this project is very similar...except for the active pickup power in that instance. However, would appreciate some checking and clarification of these ideas. * The mag pickup (a gibson PAF HB) is to be wired for a parallel switch and tone control...I anticipate that these will be well hidden (along with a power on switch) in the F-holes) * The piezo is already pre-amped and EQ'ed and has it's own volume control...I will need the blender module to blend this signal with the HB -- will the HB need to be buffered here, or does the blender serve that purpose? * I do require a Master Volume, sounds like this needed another module with some modifications there -- ? So, a bit of clarification on this would be appreciated so I can source out and order the parts. ... For the Hex pickup idea...this is still up in the air, but I have had some experience with the PreCHAmp kit and have one handy... www.jaycar.com.au/productView.asp?ID=KC5166This is a very cost effective design and with this guitar of course, plenty of space to fit things in it. In looking for the circuit, I came across this which provides for some gain and distortion control (I don't want any distortion of course)... www.aronnelson.com/gallery/main.php/v/evilpaul/PreChamp+Mods.png.htmlThe un-modded circuit looks like this...  So there is an idea there for a basic pre-amplifier for the Hex device. Some of the ideas here borrow from my old Hex sustainer drivers and various commercial pickups...or at least how I suspect they work. Although this will come along after the guitar is finished and the device tested, the concepts needs to be planned for. An overview of the proposal is in this not too well drawn paint diagram...  The idea is pretty simple. The tape head is aligned as close to possible to the bridge (the sensor is very small so you don't want the string to swing outside of this field. The head consists of a horse shoe shape with a coil below and a small gap which senses magnetic fluctuations. To the outside of the head, a bar of magnetic material (say steel) will be directed up towards the string directly opposite the head sensor. This will magnetise the string directly above the sensor. the fields of magnetism will be drawn back across the head and down. By having all poles the same direction, this should provide some degree of separation magnetically. For my application, I am considering mini switches, one for each head (all grounds stay connected), tiny DIL line switches could be built into the pickup itself simplifying wiring to a shielded mono out. I'm not sure if a single simple amplifier is the way to go (probably enough to test the idea) or will give a decent sound as the quality of the sound from such a device is a little unknown (it could of course be processed a bit outside the guitar) or how things will combine...perhaps there will be unexpected effects from simply switching in extra coils in this naive way and more is required. Any thought on this aspect of the project would of course be appreciated and could lead to other applications of such a pickup idea I am sure. The tape head idea is certainly the cheapest and easiest device I can think of so far to produce such a result...these things look neat and shiny, cost $1 each and are very compact. Magnetising the strings is not a difficult nor expensive proposition and I am reasonably sure they will produce "a" sound. If very keen, and a bit of recording equipment...one could make a bit of a guitar synth with separate outs. There is free audio to midi conversion (getting better in terms of response) that I have played with a little. If one were to record or have 6 audio inputs, each could drive it's own VST synth of choice...if one were so inclined. I could conceivably make use of such a system for recording but the proposed implementation would not allow separate out signals...but if one were so inclined, there is some potential there...if it works!
|
|
|
Post by newey on Oct 10, 2011 5:47:05 GMT -5
I think the knobs look good. If one is to be a master volume, or a blend for piezo/mag level, I think it should go on the bout, Gretsch style- but of course trickier to wire up there on a hollow body.
On my Stealth Strat, JohnH has convinced me to use a two channel buffer/preamp- the mag pup gets buffered on one side of the equation, the piezo gets a bit of boost, then the two active signals get blended together. JohnH has a circuit for this that I've redrawn, I'll be posting a copy soon if it vets out OK. It looks to be quite similar to what you would require here.
For my purposes, the mag/piezo blend will be preset with a trimpot, since the idea is to keep it "stealth", but of course a regular pot could also be used.
|
|
|
Post by newey on Oct 10, 2011 5:50:56 GMT -5
BTW, if you're still inclined to use thumbwheel pots, pre-made Jazz guitar pickguards are available with the thumbwheel pots along the edge, underneath. Can't think at the moment where I've seen those, but they're around as replacements for old Jazz boxes. Of course, not sure if the look of a pickguard is wanted or not, but it might be an easy way to go as far as mounting the things.
|
|
|
Post by 4real on Oct 10, 2011 6:01:17 GMT -5
Thanks Newey...I'm impressed by your project...
I think the knobs look cool too, makes pot selection (different values), longevity, fitting and use a lot better.
I like to have a volume control close at hand, so that will be that one. With a guitar like this I would anticipate that feedback if unattended would be certain!
I'd like the on/off power switch so that the tuner could be used even when not plugged in...this guitar is not the greatest acoustically (lacks bass) but sounds surprisingly good.
So does that mean...tone and parallel switch for the mag...a buffer for the mag, into the blender with the pre-amped piezo...then to another buffer for a master volume...then out?
Recommended values for pots?
I'd hide the tone, S/P switch and on/off switch in the sound hole.
The second control is a blender and I can see that being used quite a bit for different sections of songs perhaps, or between songs at least.
The third control is for the hex system master volume. If that doesn't work out it could be omitted or sub-ed for the tone control
I did try putting the knobs in the obvious places but didn't like them there myself on this guitar...nor have I found that gretch location ergonomic, except for something like a selector.
I think more those aesthetic things will become cleare when the hardware is on the thing. The pup and tailpiece changes things quite a lot and possibly no longer worth pretending it is an 'acoustic' once fitted up...but that can be left till last and we can vote on it if you like.
...
Oh, well I seem to find a way with these things as far as mounting them. After wiring and testing everything, I thought everything could be built into a shielded box and glued to the top so the controls just peak through. I have found various sources (amazon have them for $3.50) and seem to have traced the manufacturer which have a range of options and even switched versions and thumbwheels that are numbered. Considering the cost of a pot and knob, it is quite cost effective and might suit many projects in 'nutz world'. They are not just trimmers with a wheel on them but they are pretty small.
I doubt there will be any kind of scratchplate, but the F-holes are kind of cartoon-ishly large IMHO and one can easily reach inside to adjust things with barely any of the dial visible against the black guts of this thing. I will try one for the tone control. plus old slide switches for the 'series/parallel option'...
Who knows, perhaps one day I will spring for a full hex system so I can play into a synth..or more attractively perhaps, play directly into guitar pro for transcriptions and such.
The concepts on this guitar may well turn out so well, I might make another some time with even more bells and whistles and even more accurate manufacture...but this is taking a lot of hours and likely to be the only one of it's kind ;-)
...
Oh, and in anticipation of needing access, I'm pretty much sold on a reasonably size plate on the lower back side for a range of jack sockets that will also provide access to insert the circuits and controls required. That way I can have a few outs or add and subtract things at other times should they prove useful
At present I am planning on a strap button stereo socket that will secure the tailpiece as well for a direct out. I could see the usefulness of a stereo out for the mag and piezos...and likely another out for the Hex...potentially some special socket system that will provide all three to a break out box and a single cable.
There is of course a sizeable hole cut out for the tuner in the side and I ahve kept this piece in anticipation that it could come in handy ;-)
|
|
|
Post by newey on Oct 10, 2011 11:05:46 GMT -5
So does that mean...tone and parallel switch for the mag...a buffer for the mag, into the blender with the pre-amped piezo...then to another buffer for a master volume...then out?
In the version JohnH designed for my project, there is no second buffer, there's just 2 JFETs- one with some boost for the piezo, one to buffer the mag. JohnH did recommend a third stage, but I'm trying to keep this as simple as possible, in part because I've no experience building these types of active circuits, so this is probably more of a "tutorial mode" for me than your project is for you.
My design (which I will start a new thread on soon as this moves forward) involves using only 2 switches, which are both DPDT On-On-On types. One is now dedicated to controlling the active selections out of the preamp/buffer circuits so as to give:
1) mag pickup, through buffer 2) Mag through buffer + piezo through preamp, joined with a blender pot. 3) Piezo through preamp
The second switch is up in the air, as far as what I'll use it for. Initially, I thought of using it to be a "hard-wired" tone switch for the mag pup, which would come passively before the buffer circuit. Lately, however, I'm leaning towards using it to control the mag pickup output- so that I can have the mag pickup passively to output versus through the buffer, with a third position being an "off" or standby position. That way the mag pickup could be used strictly passively in the event of a 9V battery failure.
The blending action therefore takes place after the pickup switching, via a trimpot. This, too is open for debate but currently I'm leaning towards mounting it on a separate small piece of board in the back trem spring cavity so as to keep the stealth look. A small hole through the back plate would allow screwdriver access for adjusting the piezo/mag balance. This won't allow for adjusting it on the fly, but does allow tweaking it without the need to remove covers or destring anything.
As you'll see when I get this posted, the blend pot is a 100K linear; the piezo pre also has 2 10K trimpots to adjust the piezo circuit output.
|
|
|
Post by JohnH on Oct 10, 2011 14:34:15 GMT -5
Pete - for your set up, you wont need much extra electronics, since the piezo is already sorted out. You should put a buffer after your mag pickups (after their volume comtrol), then the blender module (ie 500k linear pot with buffer (ie as I drew it). So theres two JFETs needed, and they are not producing gain - so in fact the circuits can use most types of JFET. As drawn, they will be fine for J201 or 2N5457. With other types, one of the bias resistors might need a different value.
Neweys circuit is similar but different because he is using a raw piezo element without preamp, and does not need to be able to plug into a line input. But for you, I would think you would want that option covered, hence the second JFET stage.
The tape-head pickup is an interesting idea, and Im not sure what to expect. I suggest hacking up an old Walkman or something, and hold it over a guitar string to see what comes out. Rather than build a new circuit, you could try wiring it to a mic mixer input, which has plenty of gain, to see what signal is available.
John
|
|
|
Post by 4real on Oct 10, 2011 17:11:38 GMT -5
Thanks John I will draw up a rough scheme then to check things over but I think I get the idea and the components should not be hard to come by if I don't already have them. So, need the buffer on the mad to make it low impedance and match the piezo post preamp. Tone and such before the preamp. Another for the blender. Should I not require yet another stage for the master volume? The mag will not have it's own volume control, that was a bit of overkill there. However, I will be wanting a master volume on the whole guitar and from what i seemed to be reading from TG's thread is that another buffer is required to do that??? ... I am kind of excited about the tape head hex thing and it should not take much or expense to experiment with and no modes will be required to the guitar to test these ideas more fairly...there is a lot of room between the top and strings and no bridge pickup to get in the way of playing about. I've no doubt that the things will sense the strings in some form, can't vouch for the resulting tone compared to a mag or piezo system. It is very much related to my old hex sustainer driver things...but then, they eventually went no where, so who knows....till someone does it. Hacking a walkman...well...hmmm...I think it better to hack these cassette adaptors that will not be long in coming. It is not quite as simple as wiring hte heads under the strings and the string will need to be magnetised and each be somwhat isolated. I am pretty sure that the diagram above is the way it is/was generally done and should create that effect. It might sound quite different though, from what I can see it is sensing more of the side to side movement of the strings as the coil runs at right angles to the string unlike conventional coils...but I have found that this produces a signal. Given the amount of cheap processing available (and already have) one might find that the things make a sound at least equal to the purpose intended. Or, there might be unexpected phasing effects...but will give it a go in a few weeks when the guitar is more advanced. ... A lot of rain here, as a lot of this work needs to be done outside, that is a bit of a problem for now. Last night was a bit stormy...here's a bit of a pic of the sunset that stopped work yesterday due to lack of light... 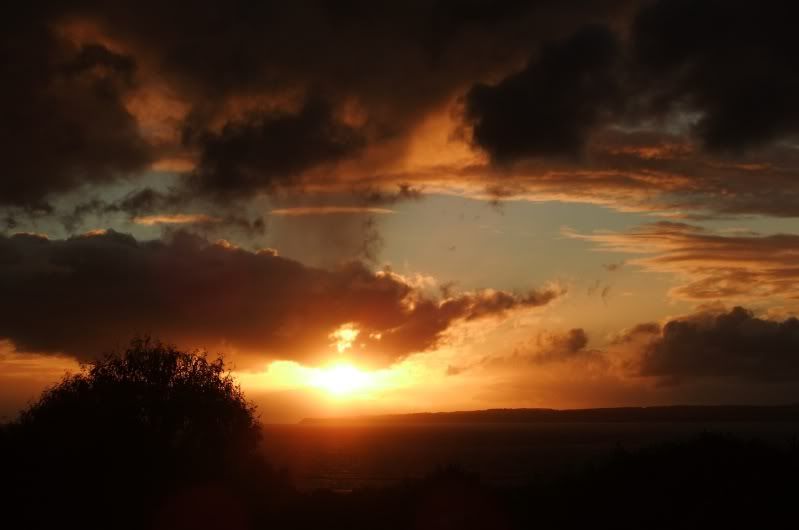
|
|
|
Post by 4real on Oct 11, 2011 5:37:45 GMT -5
Well...more storms today. These days I don't really have anykind of 'workshop' so it's the dinning table, occassionally a dingy garage with gravel floor and a few inches of water in it...or best, out in the sunshine...if there were sunshine. LOL. You definitely don't want to be hacksawing and filing aluminium without a decent vice or thinking you can vacuum things this stuff out of a carpet! However, although been a bit busy with some stuff, got some 'presents' in the mail, one was these machine heads from GFS. As this project is becoming a lot more than originally intended, i thought i'd take a budge approach but still want this kind of thing. I love locking tuners but didn't want to spring for real schallers, so went for this similar cheaper version...not as good for sure, but servicable. It makes it so much easier to take strings on and off, means you can loose the string trees, no windings around the posts to loosen with a trem and...did I mention the strings come off in seconds, great for scratchplate guitars where you need to get into them LOL... anyway... 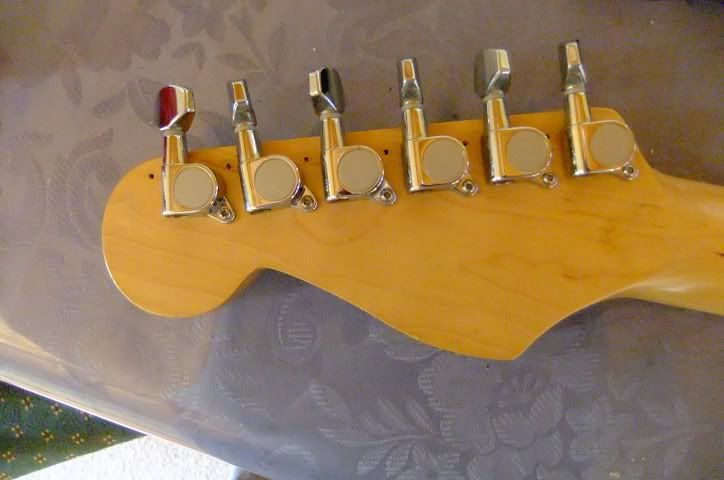 The old tuners...obviously my quality cotrol 20 years ago was pretty poor...this guitar (well neck of) has quite a bit of sentimental value...but really, these off centre tuners are a bit rough (I know I didn't have a reamer that I use now and probably used a drill bit...bad idea for widening the big tuner holes). 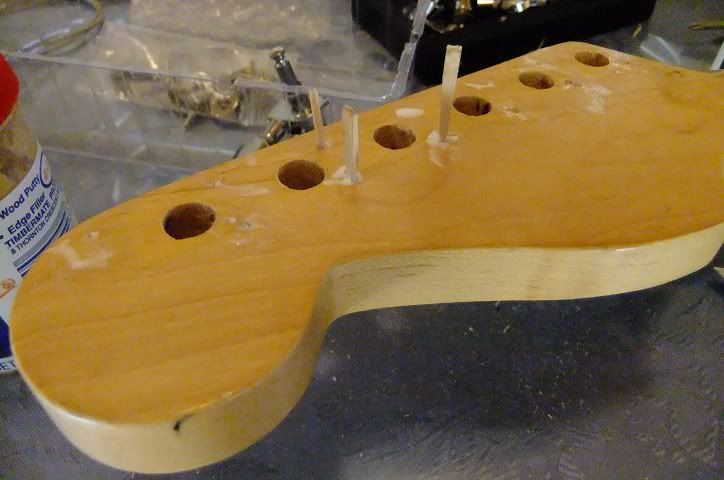 This guitar looks like it has had at least 3 different sets of tuners...so there are a few holes and all are a bit off centre, so the ' correct way' to fix these things is to fill the holes properly...toothpicks are traditional, I didn't have any so the tounge depressors do the job with a bit of glue. 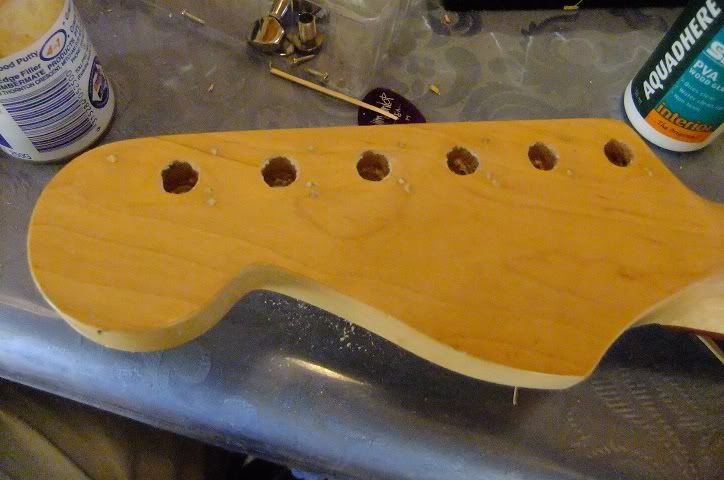 It really does not take much to do this properly, ream out the holes a bit better and line everything up...use a ruler, do not rely on the eye... 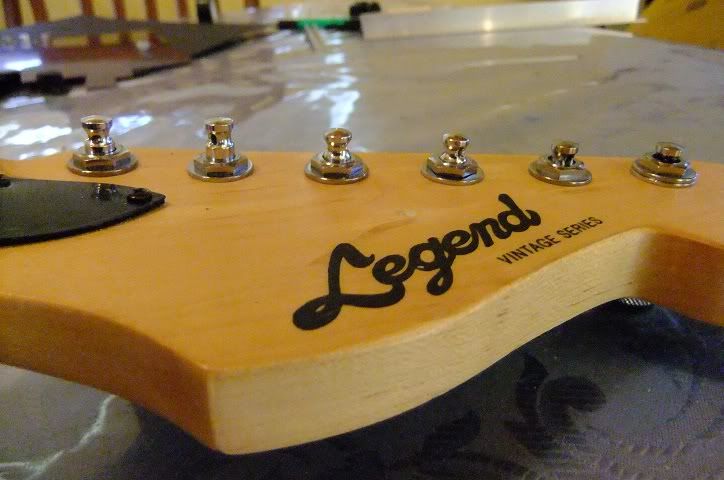 Staggered tuners...ooops, two washers on that high e, I thought i was missing one, take that off of course...use a 1/16" bit to drill new pilot holes and screw the things in line...fill the string tree hole 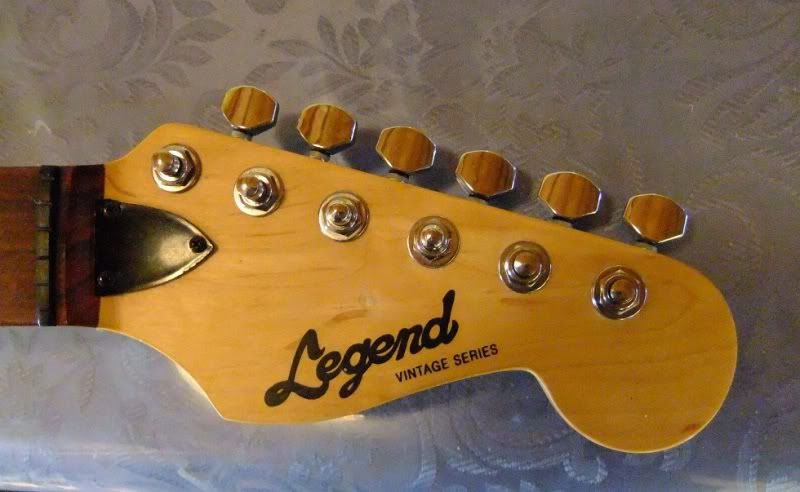 All lined up, ready to put the strings back on. With strats, staggered tuners are often not enough. On my strat I have two roller trees as the resonance behind the nut can be detrimental and I plan an alternative for this guitar. On my tele the LSR contains tiny string dampeners within it behind the rollers to fixes the problem completely...no trees required. ... Ahhh...but with the stings off, might as well bite the bullet and cut a hole for the HB... 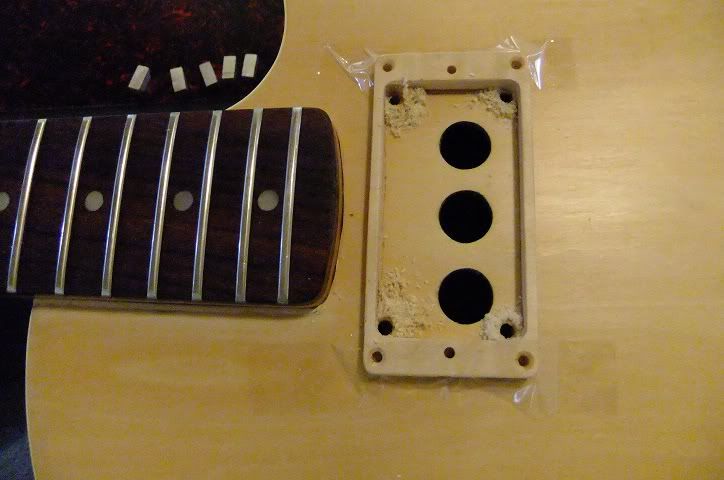 I had reinforced the top around the neck pocket and did the same behind the pup once the hole was finalized. The internal 'struts' that run the length of the guitar was missed on the upper one, but I ahd to cut half way through the other...that should be fine, but I might reinforce that before i'm finished just to be thorough. ... I did take a moment to do a little more bridge work, filing the little aluminium bridge pieces to fit the slot. Still very rough...but it did occer to me that even in this state I could test out the piezo actually works. This preamp is a bit 'cheap' and the tuner a bit hard to read ('i'd expected better than unlit LCD screen...but the LED's are bright and does work. The bridge also works to create a nice strong signal. No noise but not the greatest test as I could not tune it up with the bridge in this condition, but at least I know it works so it's all go for the bridge concept. I also was using my normal fender guitar amp and I am sure a better acoustic sound could be coaxed from it eventually. The 'power button' on the tuner console seems to turn the thing on regardless of being plugged in, so that probably saves me a switch. So, coming along..fine weather permitting, more on the bridge and then the tailpiece which is a bit involved..
|
|
|
Post by 4real on Oct 11, 2011 22:52:34 GMT -5
A fine day today but pulled a really late night...but will try and make the most of it to work outside... After many hours, the bridge is so far in this state... 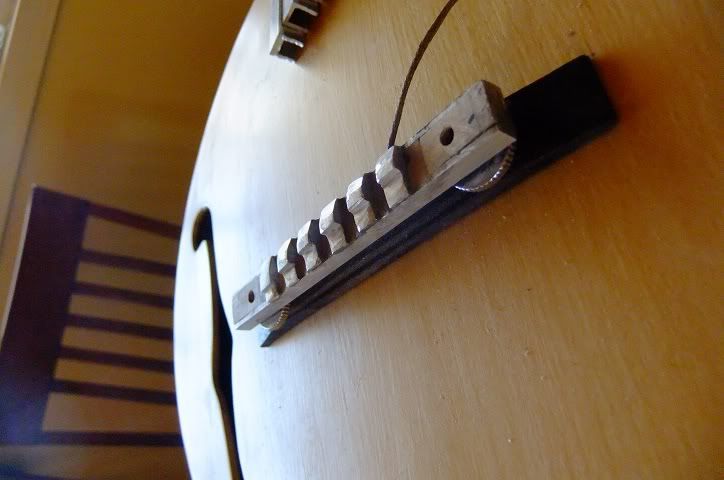 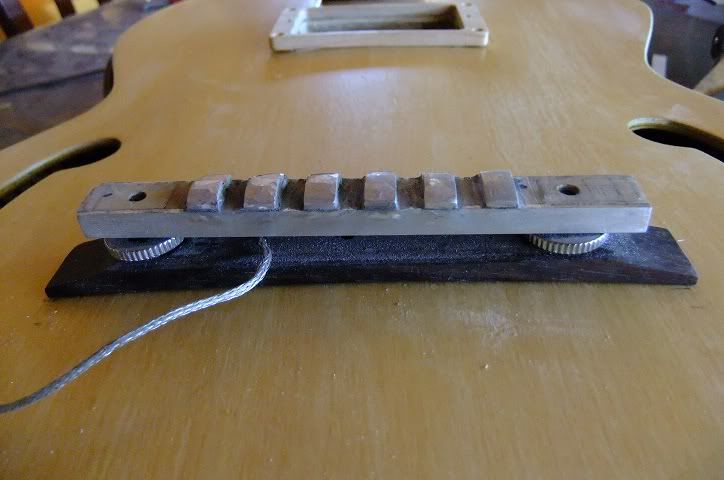 It might give a bit of an idea of what I am aiming for in this design. It's more like jewellery making really...or dentistry with a dremel tool! I was able to test it and I am getting a very strong signal from the piezo on all strings so that at least proves that aspect of the design. The bridge is extremely stiff and light, the individual bridge saddles have been roughly set to the pretested 'mousetrap' intonation...this can be adjusted carefully with the rotary tool in the final stage. Once everything is slotted, in tune and functioned correctly, this will all be 'shaped' further with a bit of an arte noveau/deco kind of thing...and all the wood will be covered in a reddish tortoiseshell that will set off the aluminium. The tail piece will have a similar vibe to match, again once it has proven to be functional.
|
|
|
Post by 4real on Oct 12, 2011 3:34:12 GMT -5
My goodness things take a long time to do sometimes...and what is with life interfering with the progress on such a fine day...hmmm Still a few crucial things were accomplished if now what I was hoping for... 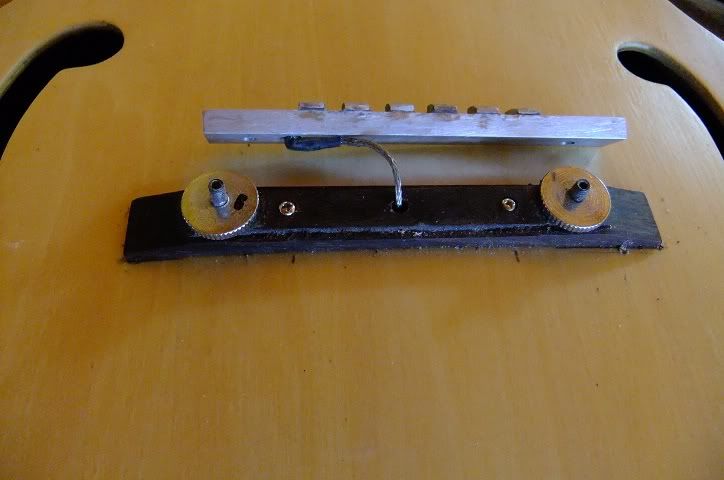 After much ado getting the intonation just right and finding the correct spot...I was not going to lose that with every string change so have screwed the bridge in place. Here you can see the piezo entering the guitar through a central hole  Here is a broader perspective...fitting the Hb...still not quite straight but getting there...these strings have been off and on so many times! I tested the grounding and the bridge does ground the strings...I wasn't sure it would but all seems well. Being metal, the piezo element and everything is completely shielded of course so that's a good thing. Just in case, the tail piece is to be grounded too I think. The bridge pieces worked really well intonation wise with all that fussing with the mock-up mousetrap bridge worth the effort after all. Each bridge saddle sets into the channel and rests on the piezo below. They are fairly tight with a little play and glued in with PVA. This fixes the pretty well so they wont be falling out with a string change, but if they should need to be replaces some day, they can be removed by gently heating them which will soften this glue. The rest of the bridge used super glue to attach things so wont come apart. Another reason for this choice was that PVA will retain a bit of 'give' and allow vibrations to be transferred to the piezo. The guitar certainly plays better with a reasonably low action and is much louder though the bass is still lacking acoustically...but I did not expect otherwise as an acoustic guitar. It actually sounds quite nice, a bit different from your average acoustic which flexes the top from the bridge. These cello like guitars move the top in a more 'up and down' motion and put very little pressure (other than downward on the highish bridge) on the top. There is the potential then in a recording situation to perhaps mic it for yet more 'flavour' or a more authentic acoustic tone than the piezo would provide. Mag Pup...This is a really old Gibson PAF style thing...backin the seventies people were taking these out for super distortions and such, I got this all those years ago in a sunday market for a few bucks. I will be converting it to 4 wire along the way. The cover is gold but suitably relic-ed and faded over time and looks the part...kind of blends into the top with the maple pickup ring. Perhaps the weather will favour me tomorrow and I can get some of the grunt work done on the tuning mechanism... The knobs are still up in the air BTW...the black/gun metal look pretty good and would certainly make pot selection a lot easier...but will ahve to see when the rest of the hardware is on what looks best. Nothing is final till you put a hole in the top...
|
|
|
Post by asmith on Oct 12, 2011 10:19:19 GMT -5
This thread is very, very Nutz. I love it. I envy your patience and motivation. For the record - one vote from me for the hidden wheel switches. I'm fond of that idea. That isn't, however, to say I think the teleknobs look ugly. They don't.
I was unsure about the humbucker at first. I had assumed you were going to keep it under the soundboard a la Ninjewey's StealthStrat. I've come around to really liking the very jazzbox vibe it gives off.
I'd be interested to read your thoughts on whether the piezo being attached to a lump of aluminium makes a tonal difference, if a lack of bass is an issue. Are you keeping the Art Deco bridge?
|
|
|
Post by 4real on Oct 12, 2011 16:16:39 GMT -5
Cheers...the thumb wheels are a nice idea but might be a problem for this esoteric wiring...will have to see when the hardware is complete to see how I feel about the look of the knobs. There are a few advantages to that kind of scheme...it's not so much that things are stealthy (it has to operate and play well first) but it is a guitar that lends itself to that. I did track down the manufacturer distributor though if interested ins uch things as they have a big variety and are the same as sold at stew mac and others. They are not just trimmers with knobs on. Some include switches, some are numbered, quiet a few values and tapers... www.shokaifareast.com/Products/Pots/Thumbwheel/thumbwheel.htm ... The piezo seemed to be working very strongly. The unit is branded an ET 4 and the tuner worked well though tricky to read (the LED lights though were very bright but the screen a needle on grey unlit LCD)...I got it and have a few others out of asia somewhere for very little. Have a few others including fender branded fishman but this oversized thing seemed to be an obvious one to use for this project. The sound was very strong and quiet it seemed and plenty of bass electrically...perhaps too much but not a good test (just wanted to make sure it worked before spending 3+ days on this bridge idea! I was hoping to get primarily the 'string sound' over the top to avid handling noise. It is a little less 'noisy' there than acoustics often are but it did pick up a bit when you tap the top and all...the bridge was not built then though. This is a cheap plastic backed, ply top guitar so do not expect much as an acoustic. Certainly the acoustic sound with electric strings lacks bass, but that is more the ability for the top and box to produce it. It is not a bad sound as an acoustic though, I think a l lot of that was the new neck joint and solid working of things and as things progress the acoustic sound ust keeps getting better which is a bonus. It does sound like an acoustic guitar though, no a semi solid. ... Aluminium has been used for bridges before, has a tonal quality and probably were similar to brass I imagine. It is likely a superior material to the kind of cast zinc that you normally find in budget bridge saddles. It was surprisingly tough, working with a rotary toll and grinding blades I broke a heap of them and wore them down so I think they will be tough enough and better than my previous choice of plastic and will look a lot better. The bridge is very solid to which is something that you don't always get in this kind of guitar, because of the tuning thing, I need it to have zero wobbles and such. It has been nerve rarking to build as it is not 'adjustable' but I am fussy about tuning, in the style this guitar is built for it is even more crucial. So a bright sound with good harmonics to the string vibration which is a good thing, but the bass is there too and very true...the electronics will bring it out a bit more. ... There is an aesthetic at work here that I am trying to bring out. It is not an acoustic guitar as such but I do not want it to scream 'electric' and have purists run or reject things by that (tis style of play is dominated by the tommy emannual crowd, jazz players at best). There is very much a steam punk thing too, but not in a 'relic-ed' way, though it will wear well and have the feel of something old in many ways. I'm not sure if it is deco or noveau ... you know there was a kind of era where there was polished aluminium and looking to a future of shiny aircraft and sticking wings on cars and all that. So there will be elements of that and 'futuristic' feel, but from the past. The Hb looks good, the maple ring really sets it off and blends in and even the old colour of it matches the colour of the top...going for that pat metheny 'only neck pickup' thing common in jazz plus keeping it well out of the picking hand's way. I was working last night with paper templates and look like I will be using a similar 'airline' like staggered motif on the body end of it despite it taking a lot more to make it. The use of tortoiseshell on the bridge (which will be shaped and subtly curved and the aluminium smoothed and polished now that it is in tune) and on the tailpiece to match will also give it an old 'radio' like vibe. The bridge looks very 'flat' at the moment...no need to get too far into aesthetics till it functions as desired. But the material is built into it and will be revealed with shaping. It will have a few more curves in it once 'sculptured'...but that will have to wait I think. Although the body is plastic, it is quite an attractive thing and not a 'bowl' typical of ovations...it is slghtly textured and jet black...has a kind of Bakelite kind of look/feel to it. Not too thick and the guitar looks very 'long' with the fender head on it and the super long string length and the longer scale, but in a good way...as if it is flying forward or something...the strat type head is a relatively compact thing but even that as that 'futuristic' vibe and does not come off as just sticking a fender neck on it and out of place (like a fender head on a flying V say). There are a lot of advantages to the fender head for tuning and trem guitars of course too. ... So, yes, the deco/noveau 'imagined future' vibe will remain and extended where possible. Thumbwheels will keep the clean look of it and will have to see how the thing looks before we get to that...will post some pics and you can make a comment on that. I tried a few knobs on it that I thought might work...but the black ones certainly look better than all others including 'old time-y' chicken head and radio like things, aluminium or speed knobs. I actually use my controls a lot, so having a volume within reach would be a good thing, perhaps volume swells and such. Because the back and sides are so black, so too are the F-holes...strikingly so...and I think that is in part why they look so good there. I have been musing that one day I might even want to put more on this guitar (I tink i am really falling for this guitar and the concept). For instance it would be super cool to have a full on midi hex pup on it...particularly for transcribing...playing into GuitarPro and the like...or to trigger samples of a real string bass rather than a processed signal as I will be doing next. There is a lot of room inside the thing of course, and any 'synth controls' would be good if completely hidden with thumbwheels perhaps at a different time...but that is a big maybe. The 'Tape Head' hex thing will also look the part I believe (at least it does in my head). Will ahve to see how it works and soucnds like of course. If I have to though, I'd be prepared to wind coils with a look a bit like my tele's driver which has a similar vibe. In fact there is a bit of that 'look' o all my guitars from the tele's aluminium bridge pickup surround covered in tortoiseshell or my LP's roller truss rod cover...so that might give clues as to how things are going in my mind aesthetically. ... hmmm, lack of sleep has got me musing... For me, while I love the look and feel of a lot of classic guitars and other stuff, I don't want that kind of thing to overcome function. That's why I am not keen of the 'retro cool' bigsby fetish thing...my first guitar had one, but really, they are shocking tuning and every other way IMHO. Far exceeded by the fender fulcrum thing...the kahler is not bad in it's way too and very solid (if heavy and expensive). The tailpiece though does have a bit of that bigsby vibe, but it has to work first and I am sure that the concept could be improved and some refinements I ahve in mind borrows from it. On the tailpiece, I am anticipating that this will improve things a bit too...far more solid than the single screwed scrap aluminium holding the strings on at the moment for set up. The aluminium plate being used is about 2mm thick, this will be doubled over the top (so 4mm there) and also have angled pieces to secure the axles and such. Sting changing might be a bit of a bugger, hopefully that will work out ok...I never break strings unless working on them and I want to keep it that way. So, not too heavy (fortunately the light body (the whole guitar is lighter than my electrics) but very solid and should correct the neck heavy feel of the guitar at the moment nicely. So with all those layers of aluminium screwed together and support pieces, filler and such the strings should be secured very solidly off the back of the guitar and free from the tops vibrations or affecting the top in any way. The 'fingers' will look like an old traditional version but the strings are actually fixed at the very end of the guitar and when looking closely, the fingers will seem to 'float' over the strings, as they in fact do. I've drawn up a heap of variations on the concept but it is hard to know what will definitively work till things are tested and such...again, no point getting too far into aesthetics till the function is right...this is not just a 'retro cool' thing, everything on this guitar must work and have a purpose or left out. String changing might be finicky but I think it should be ok...or will make it so. The big thing will be the rear catches that allow for the dropped tunings. These will hang off the back of the guitar slightly (ok, that is largely an aesthetic thing lending even more to that floating and 'forward motion' look of the thing...though it does give me a little more room to work with). The rear catch thing is key though, several ideas will work, but as john pointed out, you don't want the things to be possible to unlatch ever unless that is the intention. They also form the key to how solid the strings are being held and so the whole tuning stability and solid tone of the instrument. There is a lot of pressure on a string which will provide the 'spring' necessary, but the back of the finger under this pressure needs to solidly be connected to the base plate in the default tuning. So, tricky but I think i have an idea on that. I am making things a little 'over large' so I can experiment a little if things don't work out. However, I have a disturbing shortage of some scraps of metal that I am using. I used to have a whole variety collected over the years and I think I left them in my brother in laws shed 3oo kms away...LOL...so just have to make do and not waste anything. Part of this project is to use existing parts that i have, not collect more! Ok, well looking like another fine day, a few administrative things have unfortunately arisen, but will try and get as much progress done as possible while I can and the sun shines so we can get to the wiring side of things and the 'bigger' picture can be seen I am glad there is some interest, I think there are lots of cool things in this project and in the end, the work might encourage others to prototype some of their own ideas beyond the wiring aspects. It does not have to be as far as fabricating things which is incredibly time consuming, but there are a lot of aspects of set up and construction that can be worked on to make significant improvements in an instrument. A lot of this is an exercise in this kind of thing and hopefully the end result will show that even a plastic guitar is capable of making a great sounding and unique guitar, regardless of the bells and whistles. ... Just looking up a few images of the kind of 'style' that is influencing the 'look and feel'...  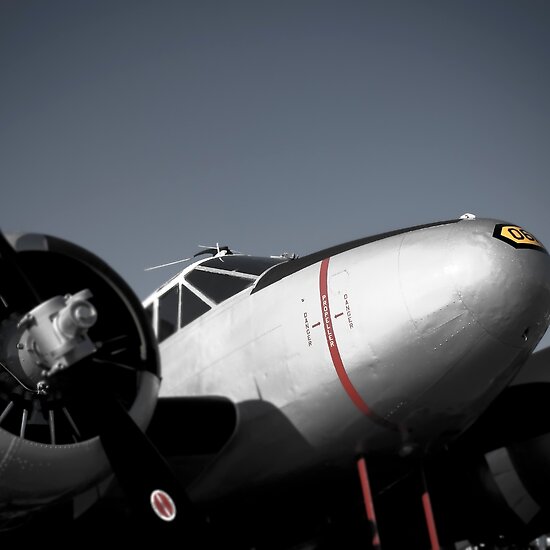 a great one for original 'art deco' custom guitars is the slide specialist (and very good gutiar player and blues influenced sideman) Rick Vito (king of hearts is a nice album, worked for fleetwood mac for a bit)... he has a signiture guitar with reverend (a company that already has that kind of vibe and unique construction techniques)...  but he always played a range of guitars he designed himself that were even more 'deco'... www.earth-music.de/cms/cms/upload/Kunstler/RickVito088.jpg[/img]I'm not going that far though....but was always fascinated by his aesthetic there...he has a love of that era. I am hoping though to get a bit of that kind of feel in the instrument, and in fact, in the music and vibe that I am working on...so that will be a cool thing to do, or at least a valid experiment.... Thanks for the interest, encouragement and khama is aways appreciated of course...
|
|
|
Post by 4real on Oct 13, 2011 17:43:47 GMT -5
Got a bit of work done...though tings are likely t intrude over coming days at least...still, the sun was shining and good to be working outside... here is an overview of the guitar at this time...  It plays well acoustically and in tune (the most important thing) and the piezo and mg pups are install though of course not wired. There is a simple elegance to the guitar that I hope to keep, but the tail-piece might change the look a little and it is still a little 'raw'. Everything seems to be to 'scale' and i think the headstock suits it ok even if it might seem a little quirky, perhaps the colour of it matches is enough...parker is charging 30K for their archtop with the parker head LOL. 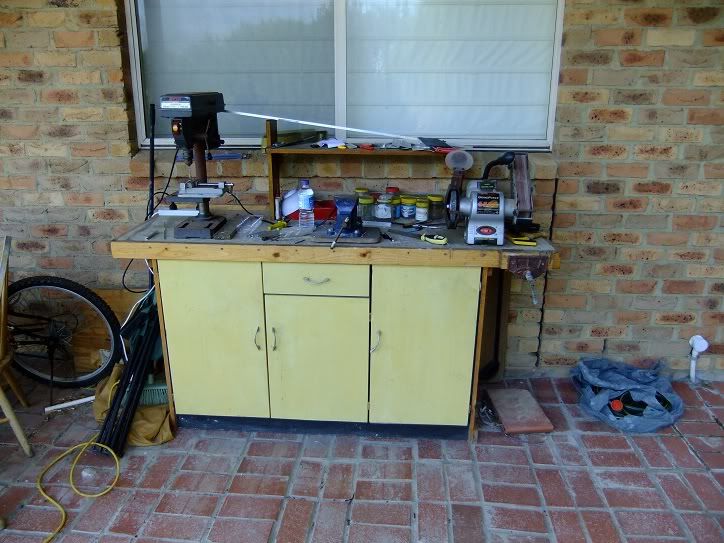 It might be encouraging to some that I am forced to work outside these days and at the mercy of the weather a lot of the time. I do have a drill press which is needed to accurately drill these kinds of things. A grinder with a sander on one side which is really useful at times...and a decent heavy vice. 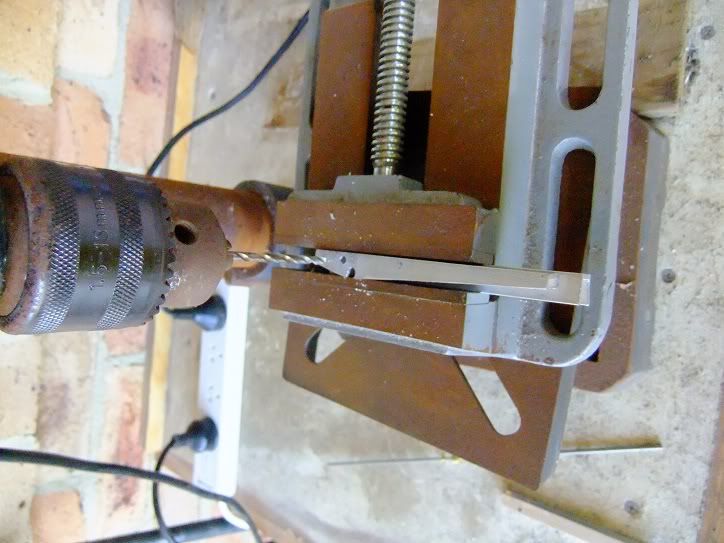 I'd made a template for the 'fingers' a few weeks back, so used that to methodically drill the holes in the 10x10mm channel sections starting with the most crucial 'holes' #1 the axle hole #2 the rear tuning bolt #3 the guide hole for making the string retaining slot. 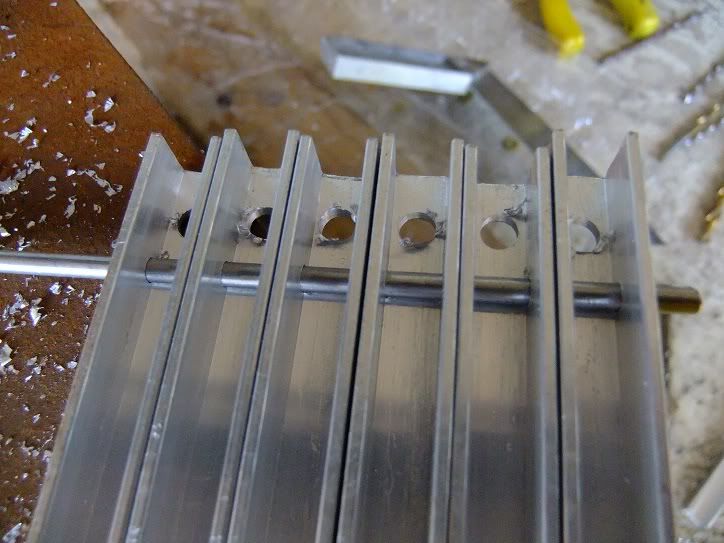 Testing with the axle material 1/8" SS...all lined up, level and working. 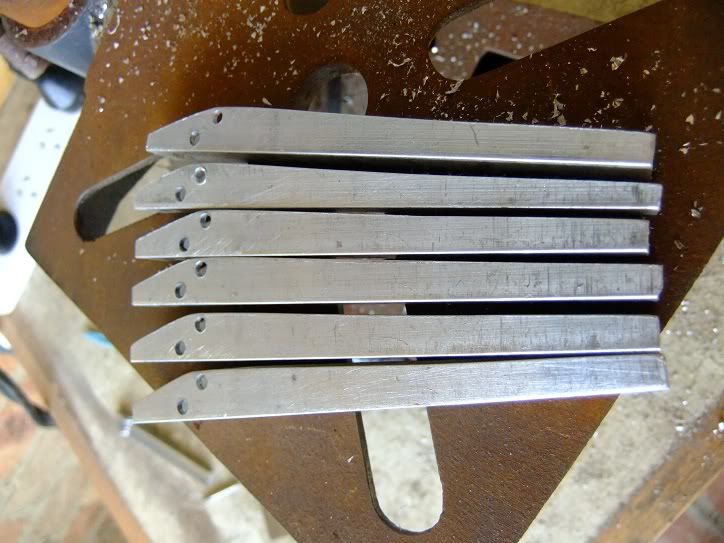 Many hours later, with hacksaw and file...the shaped 'fingers' are emerging. Aesthetically these will be different lengths (after everything is tested ok, so at present they are all as long as practical and cut down later. 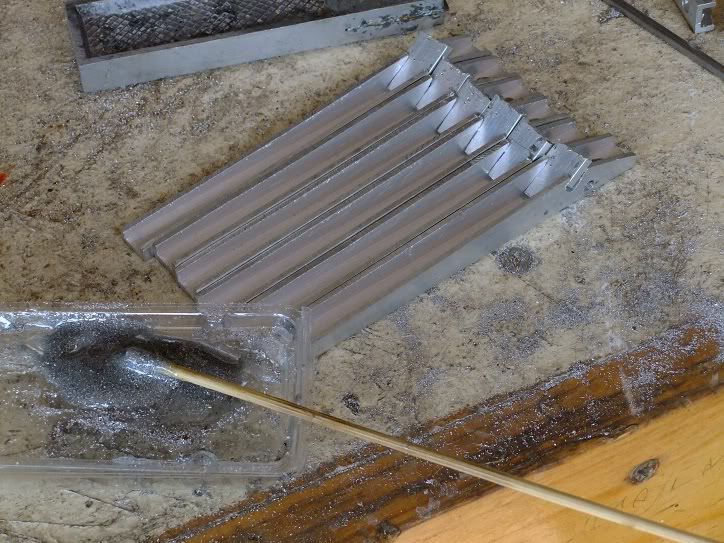 I'm not entirely happy with the string retaining mechanism, nor quite the execution, so some 'repair' is in order...mixed some 2part epoxy with some filing dust from the aluminium work and glued and filled the pieces shaped to fit into the slots and all the way to the bottom of the section all of which will distribute the load and be solid and light. 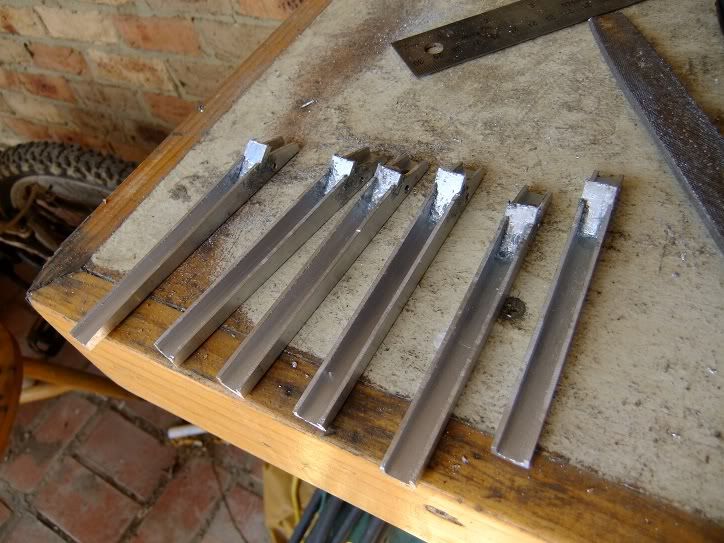 Glued in, the excess will be taken off and cleaned up and the whole thing should become solid. The intention of the angled piece is that the string ball at the end will try and ride further into the slot and not 'pop out' under strain or movement...it need to be a fair angle as these fingers will move and one needs to be sure that the string will always be held in regardless of the changing angle of the things (which could be a bit). .... So these things need to be cleaned up and slotted, the string retaining things shown to work and all is well at this stage. All of this is 'prototyping' and tedious, a lot of insecurities...it would be easier to try and replicate something that exists and is known to work even if more elaborate in design. In fact, I am sure this idea could be refined in many ways, perhaps by people with more skills or different ideas. I have chosen to try and pull directly on the strings, but one could attempt to bend them, or wind them onto a spindle. EVH's D-tuna is a great design that adapts the find tuners of a Floyd but there is a bit required there (including a floyd LOL) and it could be a tricy thing to adapt to all strings...hmmm ... One of the big "doubts" I have is the manner of locking the back of these fingers so they are securely held "up" in the default standard tuning until released. Perhaps people have some ideas...here is the sketch of how this is supposed to work with one idea that I ahve doubts about now. 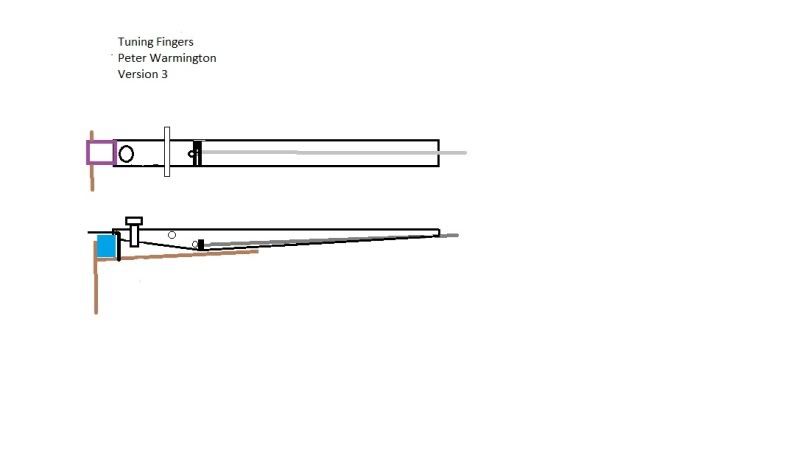 What ever holds up the back of the finger ultimately holds the tuning and the solidity of the string. The axle-ed fingers are light but very strong, the string retaining (sloped on the real thing and almost over the axle now) is quite strong and solid...there is no play to the axle and all will be held solid on a thick and well secured base attached to the rear of the body (not the top). But this "catch" is the key regardless...plus it needs to be practical in use and hopefully look good...hmm. Part of the aesthetics is possibly blinding me to ideas so fresh minds might be useful on this. I do have a look in mind...you know, ohhh, that would look cool...but that is often disastrous. I had the same experience on the bridge, 'fell' for a particular strategy and just kept at it regardless of the problems it posed. Changing that completely and rethinking yielded a much better idea and swifter progress...the end result I am sure will look even better and certainly works better in transferring vibrations to the strings. ... But taking a leap of faith that things will work out, with what time that I can devote today and the weekend (this work has seriously been taking all day and really is largely hacksaws and files...grinding these things are really not a good idea, proper metal working people would use proper cut off saws, if it were a commercial product, I guess things might be cast to shape, stamped and folded or CNC'ed or something. I have a few restrictions here as well as some of this (beside the 10mm channel) I am just using tiny scraps of material from past projects that I bothered to bring down here and I am resisting buying more for cost and the threat of accumulating more 'scrap' LOL. Part of the project is to make use of a heap of stuff that has accumulated and just cluttering things up and makes moving a nightmare...much better that these parts become a useful instrument. ... Anyway...I have a paper pattern for the rear fixing and top plate...I am tempted to make it completely, though the prudent thing to do would be to 'rough it out' and not get to married to a 'design/look' till the thing is tested and I can see how things look in reality so everything blends and lines up....hmmm...good advice, I think I will take it! So, making a strong stable bass to build the tuning mechanism to is the next step...and cleaning up the house and putting things away again against the spring weather should it turn bad.
|
|
|
Post by 4real on Oct 14, 2011 5:54:31 GMT -5
How dare real life interfere with my progress with this thing...hmmm So, today I was able to clean up the tuning 'fingers and even gave them a light 'polish' and looking good, pretty much 'precision'...this is crucial to this idea working, there can be no slop or play or non-alignment. I was also able to cut and bend the plate which will hold all this on the guitar. I discovered that I could bend the plate more accurately and easily than I imagined. It is plenty strong enough requiring quite a few hammer taps to achieve this result. I may in fact attempt to make a tray (similar to a deep tele bridge 'tray') by multiple folds rather than try and join angles and such to a flat plate...hmmm I am still working ut options for the latch thing. I found some clothes pegs here, unfortuantely only three, which have a flat spring steel that is idea...hmm, wonder where I can find more...perhaps something else I also had to go to town, busy as...its MOTO GP weekend and the island is invaded by over 10,000 bikers...if you have the GP on TV, you will get a good look at the island not far up the road from my bit of coast. While there I explored the hardware and bargain shop. It is always good to explore these places to see if there are things that might give me ideas or could be hacked to use. A few things....hmmm...but not entirely solved any problems yet. One thing I found is a set of three trouser hangers for $3...LOL...but wait, chromed flat steel...the ideal material to make these hex pickup magnetic pole pieces. I could even use them after for their intended purpose...or take off the clips to make some nice handy spring clamps x6. The catches are a real pain and only testing ideas can solve I suspect...problem is that any modification or parts made or making new parts takes hours and hours if not days and I really don't want to have to go through all this again. The preferred option should work as a kind of 'push button' that will swing away and release the 'finger'. It will need to be sprung so that it will pop back into place when the finger is returned to pitch. I seem to have a way to string it ok, trickier than a normal guitar but doable. I have planned a string retaining axle that will keep the strings an even angle over the bridge. I had concerned that the lower tuning would not only loosen the string but change this angle adversely. These kinds of bridges rely on tension over the bridge. I am also considering making a new bridge base. This is not necessary, but have wondered weather a 'blonde' bridge will match the pickup ring and general black/blonde look. No hurry though, get things working first. I will only get around to wiring the thing and deciding on things like thumbwheels and such later. Although a good idea, one distributor got back to me and said that these would not only cost a bit, but a minimum of 10x of any particular value required...hmmm...perhaps not. .... I did take one pic 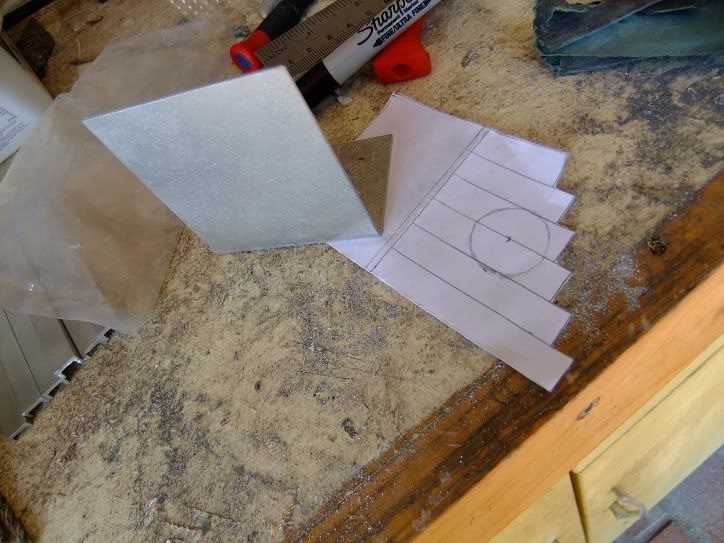 This does not look like much, just the neatly bent plate, but next to it is a proposed paper pattern of the rear which will match the pattern of the fingers, all being well...let me know what you think. 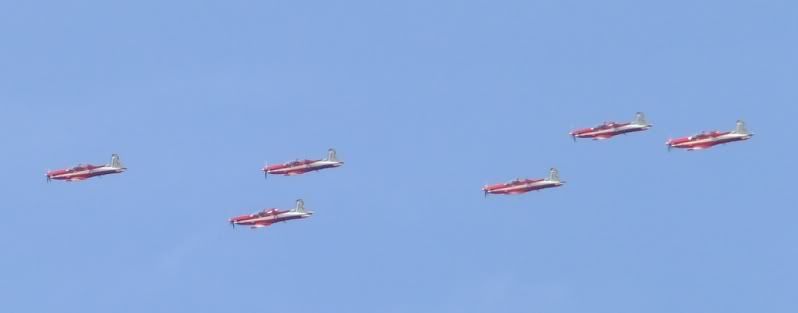 My house was buzzed a few times by these guys...my goodness there is a lot of money in bikes and sport generally
|
|
|
Post by 4real on Oct 16, 2011 3:06:07 GMT -5
GF over, week end and the moto GP on the island, so no work on the project but noticed that I had not shown a few details in some of the pics. 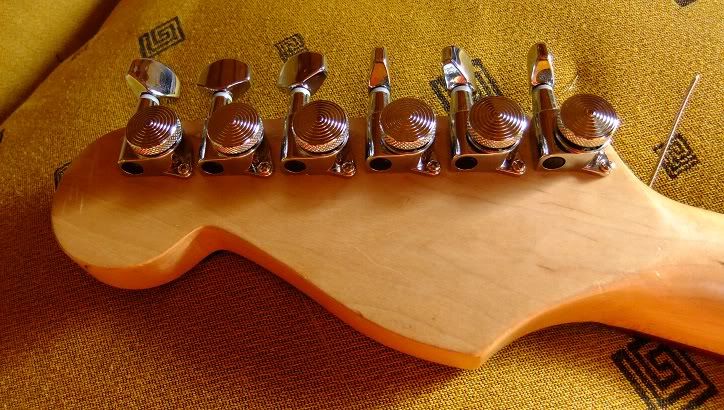 These are the back side of the "grover like" staggered locking tuners from GFS which are a little cheaper the real things...I prefer schallers as on my other two guitars but probably cost twice as much. I'd consider anyone to consider the many benefits of locking tuners, my tele strat and LP have them and it is hard to go back. Don't be fooled by wilkinson's so called locking two hole tuners btw which are considerably cheaper and nothing akin to these kinds of things. The look of these will fit well with the 'vibe' I am going for this guitar too. 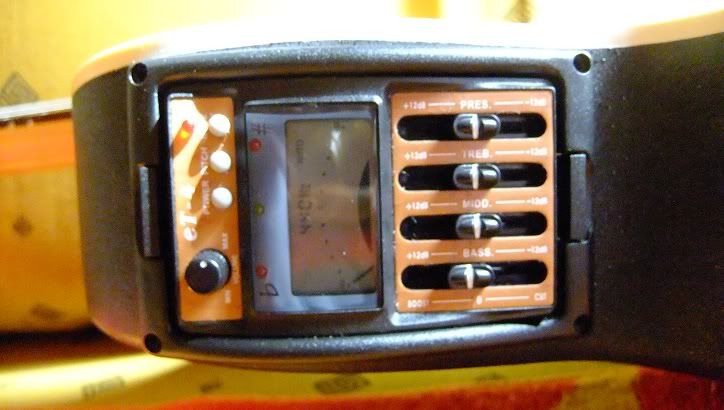 This is a side shot of the upper bout and the piezo tuner/preamp/eq system. It is nothing fancy, the tuner needle perhaps difficult to read but easy on power, the LED lights give a very clear indication when things are in tune anyway. I am sure there are better systems about and this is hugely 'oversized' but it was cheap and I had one, so it needed to be used. All seems to be working well enough and from the audiences point of view pretty well hidden where it belongs. ... So, with any luck, will continue on with the fabrication of the tuning mechanism...it's come a fair way and had some more time to think and worked out what should work and made paper patterns and such. I should also got some work done on some of the aesthetics too...perhaps the bridge will be finished off for instance...and if the tail piece works out ok should be able to make a final decision on the controls and such. No sign yet of the tape heads yet, but I am really keen on the idea musically and can imagine how things might sound with the music I have been working on. I can't be sure that this is going to be the idea way to do it, or in fact it will work at all...but musically it has quite a bit going for it I think so if the first idea does not quite work, perhaps it will lead to making other approaches to achieve a similar thing.
|
|
|
Post by 4real on Oct 17, 2011 16:57:05 GMT -5
So....hmmm....problems... Was looking good... 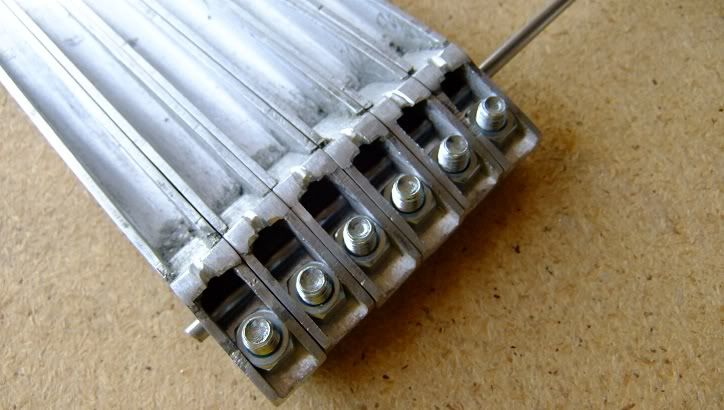 neat on top... 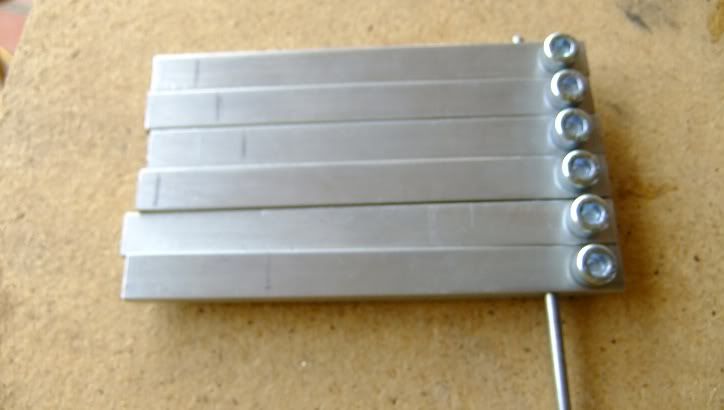 proved I could build things even though metal work is not my 'thing'...  Learned I could 'fold' things accurately which was nice... 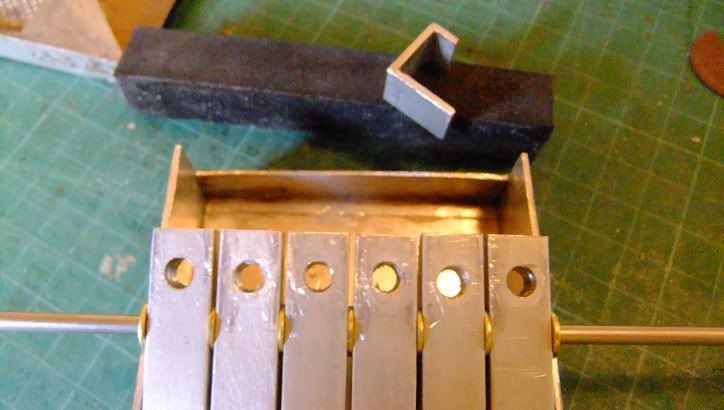 And everything fitted together accurately... ... But as the president in the 'fifth element' said..."I have a doubt"...doh! I've been encountering several problems...the latching thing was always going to be tricky and while I have an assortment of ideas there, it seemed the only way I would be able to really develop them would be to test them and to do that, I would need to build something...though perhaps the more sensible thing would be to make a testing rig and do things rough in advance. Before getting to that stage though, string the thing was getting hard and these 'hook' string retainers started in tests to be 'unreliable'...if the thing is going to have strings fly out of it, that is a serious problem right there. Most of the principles are sound and was looking good, but when made to be low profile and 'stealthy' the problems with things got more difficult. It will in fact lower a string by a tone though, so that's something! So, perhaps a total redesign is in order, maybe even an entirely different approach...even tried looking at some patents, but was hard to find other stuff that does this kind of thing with details of the mechanisms. It did occur to me that with the piezo, the changing of tunings may well produce a big 'clunk' as it is released to a new tuning...this would not effect mag pickups, but the piezo do make the body a bit 'alive' so a smoother thing might be in order...something like an asymmetric cam perhaps, or look closer at the D-tuna thing and use some spare strat bridge parts to see what might come of that. Hmmm...any ideas? ... So, perhaps I will leave that for a bit and see if I have some better ideas So, will perhaps get to work on finishing up the bridge and fitting of things...spent the evening playing the guitar and playing with the tuning and intonation. GFS locking tuners, hmm, well, they ain't schallers....they run smooth but are a bit loose, tightening up the tuner buttons seemed to help a lot for stability. The nut needed a few of the groves widened and the bridge needed a few adjustments. I think the strings which were a budget brand could be better and are getting a bit tired from being off and on repeatedly, so have ordered a good set for when things are set up finished...a lesson there also, strings matter. The guitar is being set up for a particular gauged set...be aware that if you want to 'try' something like this, not only will your intonation be a bit skewed (on this guitar the intonation is permanent, so needs to be built to the gauge...but the nut too will likely need permanent modification. The gauge I am using is 10-52 (10,13,17,30w,42w,52w) so is more like an acoustic kind of thing (in fact heavier on the bottom than I generally play on my acoustic). The A string is as thick as many low E's and sat high in the nut slot and was binding too...easy to adjust, but there is no going back LOL. The guitar is being designed for a fingerstyle thing, hence the thicker gauge in the bass. Also interesting is the frets on the thing. This neck has fairly jumbo frets which are pretty good. In recent years, I have generally used lower frets...connected to a tuner you can really see (as well as hear) how much the string frets sharp under excessive pressure. In this style of play that involves some fretting gymnastics, it is kind of hard to have an even pressure with some chord formations...perhaps I should have gone for an even thicker gauge, but I like the feeling and sound of the lighter top strings and definitely don't want to go to a wound third. .... A few things on and the weather is fining up, so perhaps I will be entering a frustrating time with the project for a bit...a little tinkering perhaps. I intend to keep it in playable condition so that I can get used to the guitar, it is nice to play and through that process get some more ideas perhaps. Still waiting for the hex thing as well, hopefully that will go well as I am really excited by some possibilities there and can 'hear' it while I play...so with some luck that will go a little smoother. It could be that the tuning thing will be postponed for some time with a better fixed tailpiece devised while I wait for, or tinker/test out alternative concepts.
|
|
|
Post by newey on Oct 17, 2011 17:20:18 GMT -5
Yeah, there's a lot involved here and discretion, as the saying goes, is often the better part of valor. Why not shoot to get this playable with a standard tailpiece, and work on the hex pickup? Then, beg/buy/borrow a cheap test mule for the tuning fingers concept, to sort all those issues out rather than trying to do it all on this one guitar.
|
|
|
Post by 4real on Oct 17, 2011 17:50:09 GMT -5
Yes Newey, quite right...the project grew, as they do. It is always possible, especially with this guitar to go back and tinker with things. Awaiting the hex things and there are still some other stuff to do, wiring, circuits, bridge stuff...wiring the pickup for 4 wire and aligning it better....the finish on the top...lots to do ... Perhaps I might have to investigate further the hipshot trilogy...might be easier to buy one even...there is a beautiful looking chromed one on their home page (probably a custom job)...they have one now for drobos that might work... 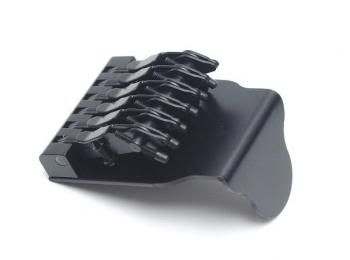 Details are sketchy, no vids by anyone of the thing in use or even much in the way of reviews...works by an elegant cam method and allows for 3 selected tunings per string. Sent off to get details, ust in case I cut my losses and go this way if that keen...days of work making something half as good, might be better to cut my losses on this kind of thing. Extravagant on a 'plastic guitar' but there are some on eBay far cheaper than the RRP from the manufacturer. www.hipshotproducts.com/The chrome one is in the gif that cycles through another pic with the leavers activated...  gives a sense of the 'size' in respect to a strat ... The tuning idea is a good one, I have always avoided anything but standard tuning and likely will favour that play, but perhaps with this new style of play, a change in tuning may be something to explore
|
|
|
Post by gumbo on Oct 18, 2011 5:05:36 GMT -5
4real..
FWIW, on my multibender Tele I ended up getting "Jagwire" stainless (pedal steel) strings from the shop on the Steel Guitar Forum...
...found that they coped well with the 'on and off' life, and one can buy them individually, making up the set that one wants...fairly cheap, VERY nice people to deal with, and AMAZINGLY FAST shipping to Oz..
HTH
|
|
|
Post by 4real on Oct 18, 2011 5:45:41 GMT -5
Had a few other things to do today, so not much work done. I had been having a few tuning hangups so put in some playing time and made a few adjustments. The design of the bridge is good and is working for that and with the piezo, but no point tarting it up while adjustments are still required. The nut needed some careful slotting adjustments (keeping in mind the recent 'broken nut thread' as a warning...so that's committed me to the heavier gauge string...ordered a nice new set of d'addarios for when everything is finished as cheap strings hurt. ... I have been intrigued by the Hipshot trilogy and is the only other thing out there that does the kind of thing I am seeking for the guitar (in fact a theoretical 726 tuning variations possible and a huge range, more than any guitar should reasonably be asked to handle). That they now make a 'drobo' tailpiece version fits well with this guitar design and new ones can be ebayed for around $170 so....thinking...thinking...made some enquiries... I also eventually found the PDF of the instructions which gives some light to the mechanism... www.hipshotproducts.com/files/all/faq443feb346780c.pdf It is similar to the kind of concept I was tying but back to front and a bit of a scissor action and clever latching cam that have three settings...a bit more solid and stable too. Hipshot are a small hand built enterprise with some interesting products...they are promoting i see a piezo bridge system that does not require preamps or batteries and will mix with mags...designed by Ned Steinburger, go figure. If I do this kind of thing, it will likely be the only archtop acoustic with such a substantial piece of hardware attached to it...luck the thing is so light and a bit neck heavy at the moment...need to get some dimensions and such. ... As it has had some plaing and gradual adjustments in the process, the action is medium high, like an acoustic but not too hard to play (an adjust ment to the truss rod helped a bit, knew I forgot something there  )...good clear notes. I was getting some sharp notes in the lower frets and some tuning instability...but that seems to be largely gone now. I had been and still might do a nut replacement and try some kind of nut compensation, the style of play this guitar is built for incorporates a lot of fretted and open notes. I might attempt a 'shelf nut' made from a spare tusq LP nut from the LP project that is black and didn't suit...so may as well use it. This wider nut would allow it to overhang the fretboard a mm and then be filed back to compensate for low fret tuning irregularities...but things have settled in a bit more and staying and playing in tune a lot better now...some of the problems may all relate to the dodgy string too, so it may not be necessary at all. ... Although I have always played in standard tuning, I can see a lot of potential and access to some amazing transcriptions that this guitar is kind of aimed at...like this kind of thing in open G... This may give some idea of what this guitar is aiming for, radially different from the kinds of playing I have been doing. This guitar works as quite a nice quiet acoustic as is, surprisingly good for what it is made of (plastic and ply) but will have a combination of a jazzy mag pup for body and a piezo for high end, and archtops tend to ahve a different kind of sound than a flat top acoustic regardless. Even a tune like this, you might imagine the lower strings having a 'sub-bass' shadowing them from a hex output. Possibly not required on this arrangement. You can also see why the tuning and open string things are so necessary, especially with open tunings. Of course, perhaps some tunes like this might benefit from a harmonised upper strings, who knows what might come from such an idea. There can be no doubt that the intention will achieve a huge range and variety of sounds. The tuning thing can even be used to sub for a capo or drop the entire guitar down to avoid playing such arrangements in too many similar keys. So, this evening I tested out a few dropped tunings. The guitar has an unusually long (fender) scale that make it feel very 'tight' in standard tuning. Dropping strings down to open G gives a sweeter sound but without that 'slack' feel and sound. The intonation was perfect regardless, perhaps even slightly better and just fooling with it opened up a whole bag of new sounds and ideas, so a good composing tool too. With the locking tuners and setup though, it really is not hard to slacken off the strings and a multi-tune bridge may seem like over-kill and probably is (like many of my projects) but it would serve a purpose and allow seemless access to such sound so I am more likely to play it and really open up this guitar in 'performance'. So, things are likely on a bit of a 'go slow' for a bit and the project will likely take some time to 'complete'. Even after all the work is done, the guitar will need to be completely taken apart and refinished, there is a light protective finish, but it is going so well that it deserves something better. It will still maintain an 'old' lived in feel and look and I believe I could fit something like the hipshot in with the overall look without being too intrusive. The black will match the back and sides and knobs and other features of the guitar and a little tortoiseshell always tends to 'blend' things well I have found  .
|
|
|
Post by 4real on Oct 18, 2011 6:18:36 GMT -5
4real.. FWIW, on my multibender Tele I ended up getting "Jagwire" stainless (pedal steel) strings from the shop on the Steel Guitar Forum... ...found that they coped well with the 'on and off' life, and one can buy them individually, making up the set that one wants...fairly cheap, VERY nice people to deal with, and AMAZINGLY FAST shipping to Oz.. HTH Cool, thanks G...my idea worked, but the manufacturing to perfect it is probably not worth the candle when this thing already exists. I'm not sure that I would ever use any 'extreme' tunings and the guitar is set for a particular gauge of string 10-52 but for sure I suspect that I might need to explore what works best over time. I have to say though, cheap strings are a bad investment...budget name brands (if not fakes) are ok, but no name strings are at best weird for some reason. I am pretty sensitive to tuning, a lot of this stuff really only works if the tuning is right (as opposed to some R'nR where it does not matter so much). ... This guitar has some interesting unintended effects in it I've discovered...because the string is so long behind the bridge, it is possible to push down on a string and get quite a convincing 'b-bender' effect (also can be done at the head as there is no string trees). Having gone all fingerstyle this year, I got fingers free to play it too. One thought I had, if this guitar was not already over burdened enough, was to make a small aluminium 'lever' attached to the bridge to make such effects a bit easier on the finger tips....perhaps even a stop screw to get a positive throw to another pitch. ... I know you have an interest in the hex thing, the tape heads are still in the mail and was forewarned that it may take a while. I found a preamp kit that will at least suffice to test the things so we will see how they sound. I also found some chrome plated flat steel wire would you believe...a trouser hanger at the $2 shop...well three...so I can make lots of stuff from this material. This material will be necessary to create the magnetic field in the strings. I also found the rare earth magnets that I was looking for that are very compact (I have a local supplier) and will easily do the job hidden below the tape heads and should generate a decent signal. So, the design is well advanced, at least in concept for this guitar and should not take too long to test out now the guitar is playing and all, one the parts arrive. The final project though will take a fair while to fully complete, it is the nature of these things, but at least the project is playable and still generating some excitement for me, despite frustrations and is a good sign. Thanks for the tip, will look into it, though stainless steel strings are hard and can lend to some heavy fret wear perhaps, not a problem on steels... ... I thought of you today while researching the hipshot in this application and came across this great steel slide player (the drobo here also features the kind of hipshot trilogy that I am considering), Pete Drake... that and a few great slide players might have me explore that direction too with this guitar...I am not the greatest slide player and there is a limit to what one can do in standard tuning after all, but this guitar has a sufficiently high action and heavier strings that would allow for that (in fact the bridge has height adjustment if I wanted to get real fussy). This guy shows that in the right hands, one can do some lovely things even in the solo guitar format...interesting bar and technique too...
|
|
|
Post by 4real on Oct 19, 2011 3:27:23 GMT -5
Ahhh...still spring time but it felt like summer... So, while a little disappointed that progress was not quite as I had hoped and looked like being more difficult and substandard compared to the only product that does anything like it. I may well continue with the ideas, it at least will need a complete test-bed and work out...so we will see how that goes as if this guitar 'works' it may eventually be replicated in a more streamlined version...one day, maybe...high hopes. It certainly plays nicely... ... while the 'drobo' model is the obvious choice for a 'tailpiece' I received the measurements and it would stretch 4" from the back of the guitar...more than half the distance to the bridge...hmmm. An alternative and perhaps better might be the lapsteal model... 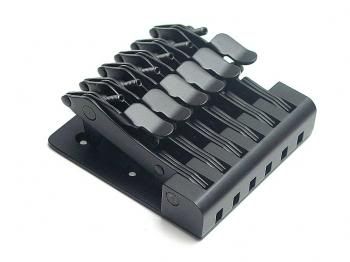 This would have to be mounted onto a tailpiece plate, but would be shorter and allow me to do a bit more with the design to tie everything in. It would likely be more versatile if I wanted to use it in a different project I suspect. .... No parts come in, so besides playing the thing, I took some time to go for a swim/surf for the first time in the season... 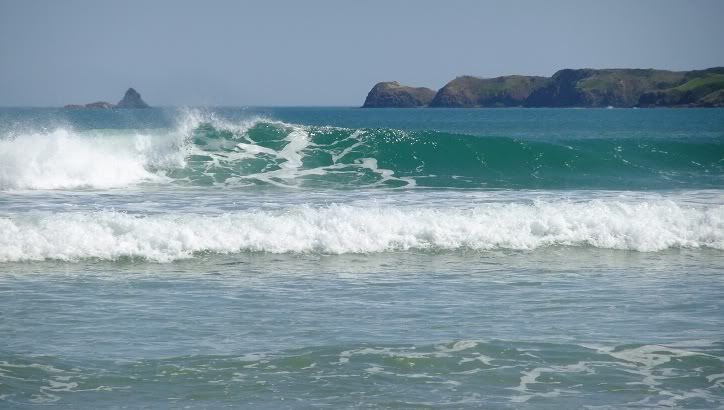 Smith's Beach with 'pyramid rock' sicking out of the sea in the background. This is the home of a 3 day rock festival on the cliffs above, known as 'pyramid rock' ~ what else would you call it! Some "house work" was required
|
|
|
Post by 4real on Oct 21, 2011 7:01:25 GMT -5
Some busy stuff going on...but... Got to do a bit of work on the project and perhaps this will give more of a sense of the direction it is hoping to go aesthetically... This bridge has taken a long time... 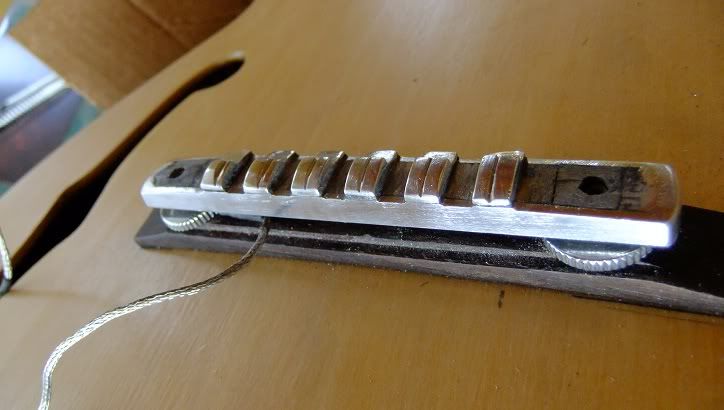 Above is the replacement for the mousetrap version, shaped a little and about ready for the aesthetic treatment and polishing... 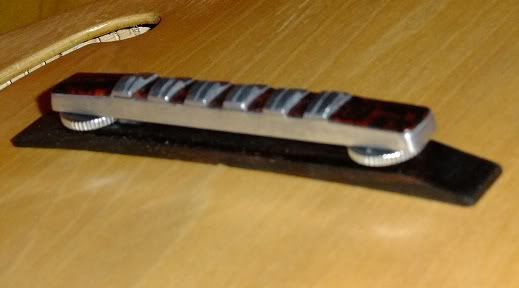 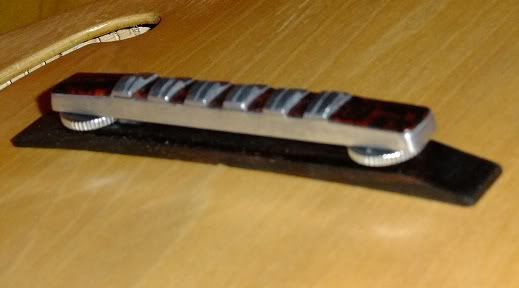 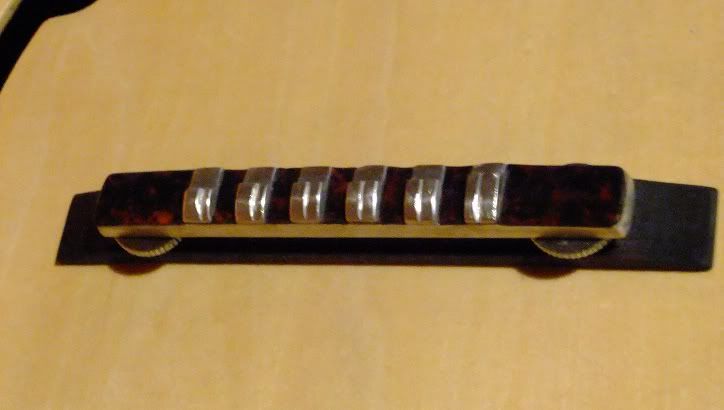 Looks like something out of the 1920s LOL...like a hair clip or the dash of a nice jag...pleased with the design and the end result. I think it was worth getting to know the guitar and play with the tuning to be sure it is right before finishing it to this kind of look, anything could have gone wrong (and did with the original design completely scrapped and this the second incarnation of the bridge) but it worked out well in the end. ... Finally found a demo of a trilogy in action and is mighty impressive in this demo of open tunings that just happened to use a trilogy... web.me.com/shenoweh/Lesson_primer/Open_tunings.htmlUnlike my DIY tuning dropper, this design has a smooth action between tunings and seems to work well on the right guitar... Tonight's sunset after a rainy day... 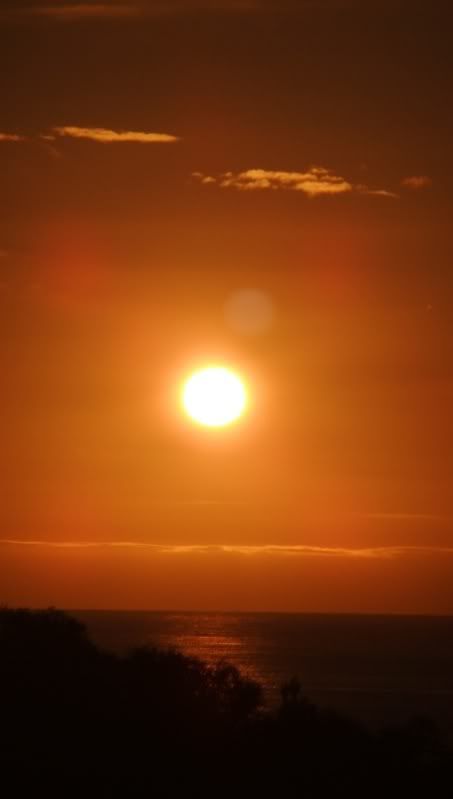
|
|
|
Post by cynical1 on Oct 21, 2011 9:58:42 GMT -5
Man, that bridge really came out sweet. It's probably academic and after the fact, but the aluminum could be heat treated to harden it and thereby extend its effective service life. There are two ways to do this with aluminum. The first is the use high heat and immediate quenching. The other is to use a slightly lower heat, but for a longer period with immediate quenching. Both of these methods will significantly harden the aluminum for your bridge application.
This has been a very interesting thread to follow. Very inventive and original. I'm really curious to see how the whole tape head module works out.
I'm already in line for the next episode...
Happy Trails
Cynical One
|
|
|
Post by 4real on Oct 21, 2011 17:18:19 GMT -5
Thanks C1
Hardening may be something for the future, it would make the material a bit tricky to work with and brittle. Aluminium has been used before but although 'soft' I think in htis application it should be ok...harde wearing perhaps than a lot of plastics' that are commonly used, but I taky your point.
The bridge was built with the saddles being held in with PVA that will soften with heat so they potentially they could be removed and rebuilt, just in case.
It also has a reasonably high (acoustic like) action, especially on the low strings which is intentional, so room for wear there...and the saddles high enough above the bridge body to allow room for reshaping.
There is of course a basic 'height' adjustment to the bridge...it was built to the action desired at the lowest position, so that some wear could be compensated for.
The bridge and the nut are weak links in tuning stability thing so likely the slots might need to be lubricated...perhaps a petroleum jelly/graphite kind of thing (if not too messy).
Otherwise, each 'saddle' is a 5mm thick standard and I imagine that I could be 'rebuilt' using a cut up graphtech nut in ivory...that might be the best if I were to do it again.
Although all 'shiny' now, being polished, this will again 'oxidise' to a dull sheen..interesting the oxidisation that aluminium experiences protects it and creates a harder surface. Does not help much where there is wear, but it is a great material and for this kind of thing, an excellent material to work with.
...
So, yes, thought about it but like a lot of things when you are trying to make something a bit 'different' or custom you can see things after the fact that might have been slightly better, but there was every chance it would not have turned out so well and all this was made from left over scraps. Having 'proved' the design, it is always a lot easier to replicate and make improvements.
These kinds of threads are kind of like a demonstration of the process and to test out a bunch of ideas and concepts and raise 'questions' and produce something interesting, slightly familiar but also a re-imagining of an instrument to suit a particular kind of play (though it is likely quite a versatile set of features.
What can one achieve if you don't have to rely on the availability of known parts and concepts or designs and work from the music out and for your own playing style and ambitions.
For instance...besides being a cheap project made of bits'n'pieces...
"Tone woods" Is that a requirement for a decent guitar, this is entirely plastic back and sides (nicely shaped with a slight bowl back but flatter edges than say an ovation), impervious to scratches and dings. The top 1/8" moulded pine ply...is this 'no good' or more perfectly good material, just as a 335 is made and extremely 'stable' and strong. How much are the pickups an element of producing a good sound as an electric.
'Hybrid' How much can one preserve enough acoustic tone, decent enough for practice (no practice amp required) or even mic-ing (it sounds a lot better than I had anticipated, at least this far). What if one looked at the piezo/electric thing as a whole sound of the guitar, not trying to be one or the other.
Can one have a fast electric neck, no 'heal', the advantages of bolt on, 15 frets clear of the body, a straight through string pull from tuner to tail for tuning stability without looking 'weird'. Can one have a thin 'electric' style string spread at the nut end and an almost 'classical' string spread at the bridge to better accommodate a finger-picking. style.
Can you make an acoustic 'compact' and more comfortable than traditional given that in any kind of performance such guitars are always going to be amplified.
'Ergonomics' I've done some thought and experiments with these kinds of aspects. Does one really need to go all "klein" to make a nice comfortable guitar to play. The arch top and wide bridge and relatively thin body but thick enough to have your right hand naturally sit in the playing position. The body large enough to sit up in one's lap. but not so big you are 'hugging' the thing like a flat top or big jazz guitar. Tilting the neck back brings the playing fretting positions closer to the body as if the guitar is wrapped around the player...subtle things, but a lot of guitars don't always 'feel' so good to play.
In fact the pickup on this was salvaged from a guitar I put together in 1983 that was a similar shape when I was playing a bit of 'jazz' and wanted something that sitted up more in the 'lap' than my Les Paul.
...
You get the idea, it is a 'concept' guitar. Perhaps it is not for everyone (that is not the intention) but perhaps it will make one think about such things and start projects with less of the mojo and fad or fetish and more taking the best bits to suit the player and the purpose over tradition and convention...but not have to make something that looks 'weird' and experimental.
...
The tail-piece is ordered and really excited about that prospect and this is a new 'look' Trilogy and perhaps a novel way of mounting the thing. It will be the only application on an acoustic instrument that I have seen and am determined to make it work and the guitar a good ambassador to that concept.
I've always avoided everything but standard tuning for various reasons, but the ability to detune the guitar easily and explore the unfamiliar may well inspire explorations outside the comfort zone and that can be a great thing. It is designed for my new musical directions and a lot of great music has been created with alternate tunings so it will be very interesting the effect the instrument will have on my playing.
...
The Hex thing will be interesting. In my tidying up yesterday I found at least two basic pre-amps already built that will be fine to at least test the low impedance tape head concept.
There is a huge amount of potential for many besides the application that I have for it and the concept is already getting a bit of interest. It could become my new "sustainer" though I hope it does not run away like that concept did and people will take the way forward and run and share where these things might go.
There will be people who may seek to use it with some kind of DIY midi controller perhaps, other's may want to explore things like 'hex fuzz' for a heavy sound without intermodulation, some may seek to process some strings separately form others, some may seek to run a mre 'stereo' like sound with bi amping...there is a lot to explore.
On this guitar, the ambitions I think are more modest and achievable. A supporting 'shadowing' sound, doubling bass notes as was the initial idea, but equally other strings to produce equally valid effects. The more I have thought and imagined the possibilities with thing that I already have at hand, the more exciting the idea may be.
There are a few limitations for carrying this over to conventional guitars, though not something that can't be overcome.
For instance, measuring my tape deck here, the head is 11mm wide. I designed this bridge to accommodate this spread and it only just works on this neck without the strings falling off the side of the fret bevels...so very close though. Fortunately, a wide string spread at the bridge is my preference and one of the reasons that I like Kahlers in that it allows one to adjust the spread, not just height and intonation.
I am sure that there are much smaller heads about, and I do not know the spread of the cheap source of heads I have located, but finding a specific sized head could be problematic. It is also a type of pickup that must be aligned with the string and so will need to be very close to the bridge as is typical of hex devices. How this will 'sound' when it is picking up such a high harmonic-ly rich signal...hmmm...could require filtering.
An interesting aspect of this pickup is that the coil runs transverse to the string (across the string) and will be primarily reading the vibrations from side to side rather than a conventional pups reading of an up and down vibration. In that way, it should be a new kind of thing that is perhaps a mix or piezo-like and mag sound in itself.
In these days of modelling, not available when these kinds of pickup ideas were originally explored, there is a lot of potential to get such a hex system to produce a decent sound...look at what a variax can do with a piezo signal for instance without getting into midi and synths.
...
This guitar is the perfect candidate for this kind of thing. The nature of the design is that there is a huge space between the top and strings at the bridge...plenty of room to construct something that can be surface mounted with this technology without drilling into the guitar. I did carve an 'invisible' channel into the bridge bass plate that will will allow wires to invisibly enter the guitar. In the development phase, everything can be tested externally. The string spread is generous. Plenty of room inside the guitar for electronics and such. A cohesive, not to ambitious application for such a system.
I have two cheap (sub $100) digital modelling effects boxes, a lot of people do and there are any number about that could be put to new use for processing.
For my application, I can hear a big range of cool effects possible. My korg AX1G for instance has an amazing sitar simulator, an old zoom 606 quite a decent little acoustic sim. Both have the usual array of amp sims, EQ, limiting and compression as well as digital pitch shifting.
Even common effects like delay or chorus or even more extreme effects like distortion could be combined on selected strings and not others. An auto volume swell could produce an interesting 'strings' effect if used with a lush delay and chorus behind selected strings
Regardless of where others might take the concept and technology (i hope all that is shared as an open source thing btw) I think that aspect will be very interesting and forward thinking.
The important thing in this project and recent things I have done, is to make a valid instrument in of itself, something that is aesthetically and functionally working and building on a tradition while reaching forward. So, I think I have learned a little and try and steer away from 'pure research' concepts and sharing them openly.
I have no doubt at all that the things will produce a signal...but this is a low impedance novel pup concept and people should not be thinking that they things will sound like a conventional pup...but then perhaps that is part of the the point too.
...
Parts are still in the post of course, a few more weeks at least, but a lot more to do on the project and that aspect is last on the list.
The electronics will require a bit of assistance I am sure, but first the guitar needs to be working well before that kind of thing need to be considered.
I'm really pleased of the interest and think that this will be a really interesting set of features that will be inspiring for some years to come from people with a huge varied interest.
|
|
|
Post by 4real on Oct 24, 2011 1:49:11 GMT -5
Got a few things happening here, but the Heads came in today for the Hex system and this aspect of the project has so much potential and already some interest and wider applications...I've started a thread on that aspect alone... guitarnuts2.proboards.com/index.cgi?board=wiring&action=display&thread=6014I have to say that this forum is one of the most welcoming and enough 'out there' to entertain such a thing and contribute to it, that I am pleased to be able to share it here and direct people to that thread (and so this forum) for information about it. There are some really exciting possibilities in teh concept and initial testing is extremely positive...so go nutz! 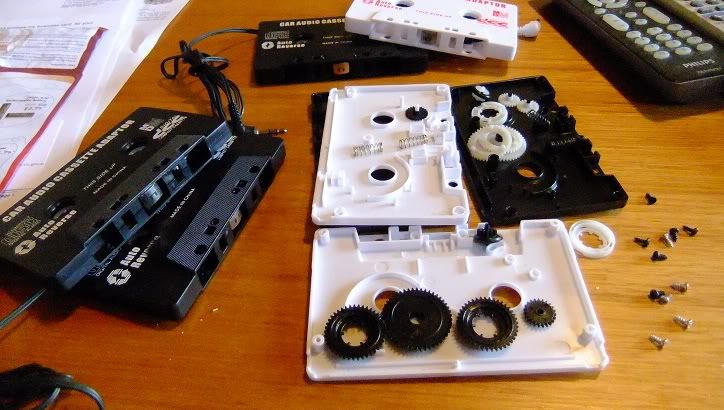
|
|
|
Post by 4real on Oct 25, 2011 20:24:33 GMT -5
Hmmm...packed up for the 6 mounthly house inspectin and a new agent...didn't turn up...this has happened every single time! Oh well, got a clean house and a little time to tinker...so HB ReWire from 2 to 4 conductor wiring...The HB for this project is an old gibson I got in a market in the early 80's or late seventies (possibly a victim of that era's trend to rip things out and replace it with the old muddy "super Distortion" pups...) My gain for a couple of bucks and looks mega cool with a worn gold cover and all, but of course, single core wired...so... 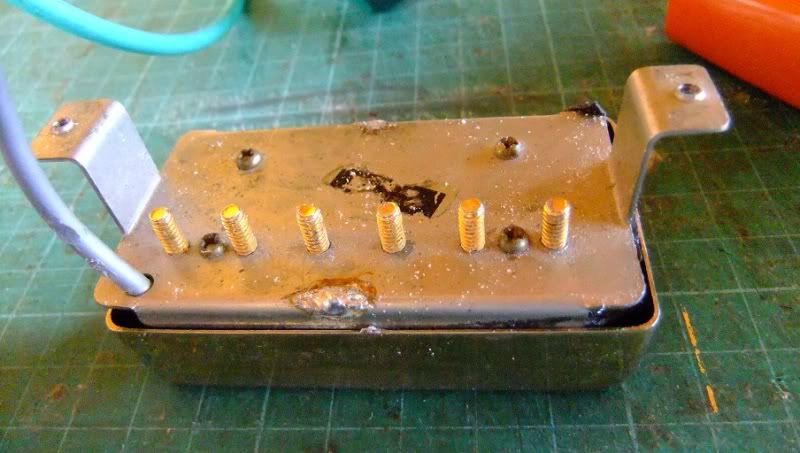 The cover was already off, possibly by me a long time ago, but to remove a bit of braided wire will soak up the solder holding the cover without fuss or too much heat....or having the solder dribble further into the join and even harder to remove. Un-soldered shield from cables work or you can have some special for your soldering kit.... 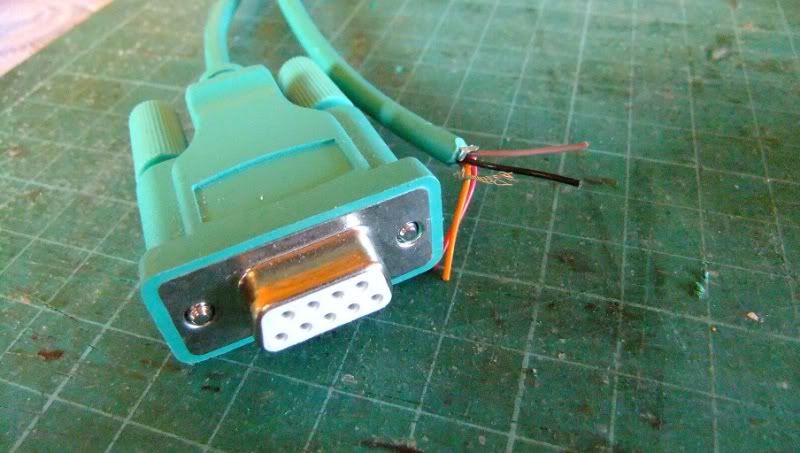 Not having a small enough 4 core shielded cable to suit, I found this computer cable is such a thing. Computer people may recognise what it is...shame about the colour, but quite good. 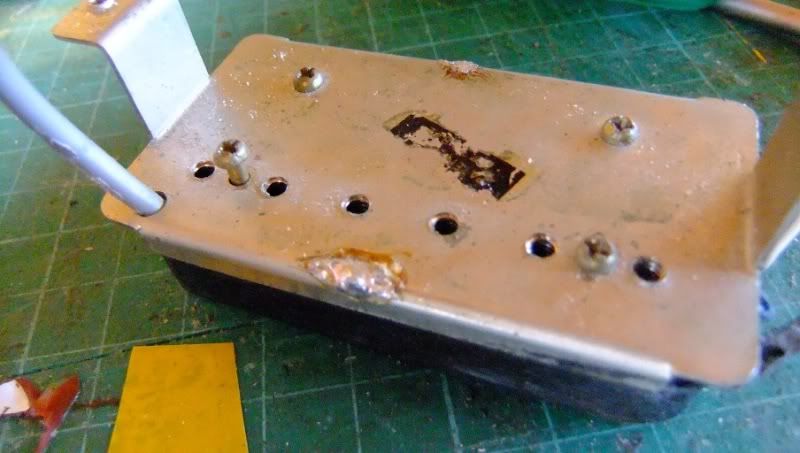 Take out the screw poles and remove the bottom two screws on that coil holding the bobbin on... 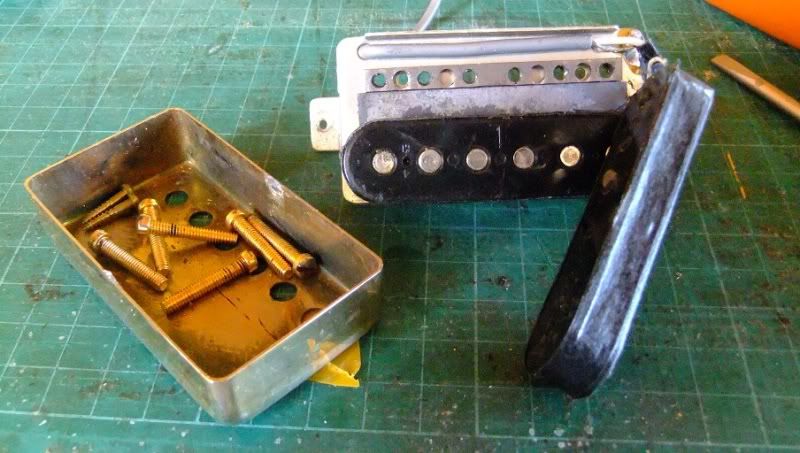 Don't loose any screws...the cover is good for this. This operation is what is required to flip the magnet as well. The cable is soldered to the base plate as is the other coil's ground wire and will need to be disconnected...again some soldering braid helps. Be very careful with the wires from the coil, these are short and connect to the actual pickup wires which are a delicate hair of wire...so excess heat may break or disconnect thing and you do not want to expose the coil itself. 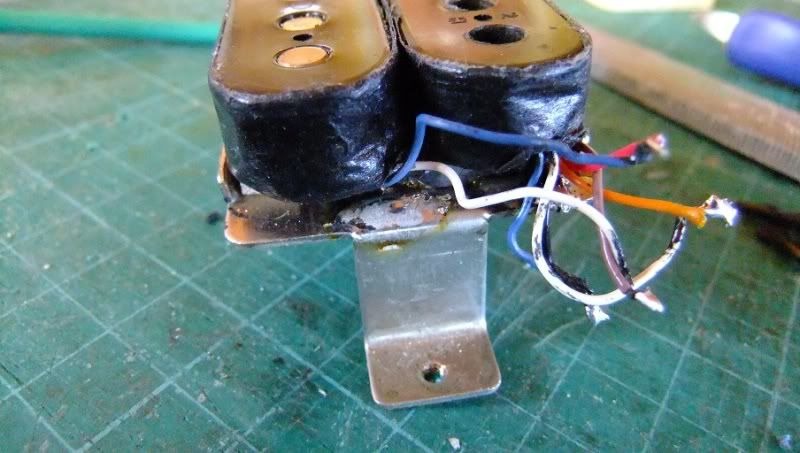 This shows the coil wires blue and white for each coil. One is connected to the first, the other two connected and another soldered to the base plate. With that last one, I snipped the wire as that is safer than de-soldering such a delicate connection. Remove the original 2-core wire. 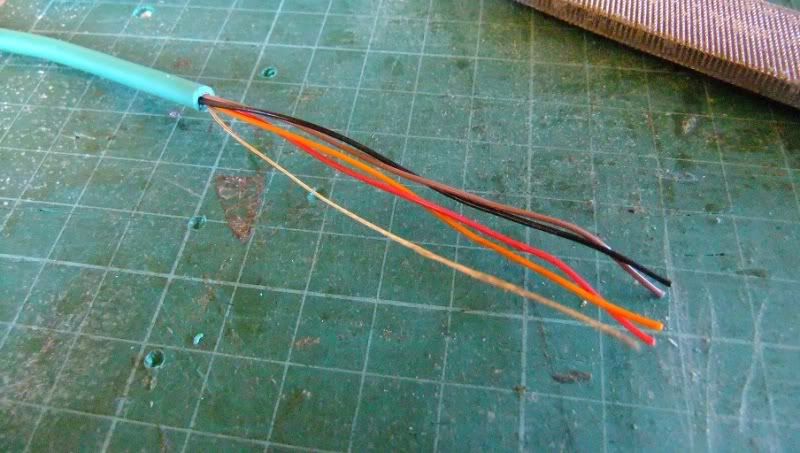 Wire stripped. This insulation was a little bigger than the whole and for the wire to sit well under the bobbin, so stripping it back to the hole is necessary... 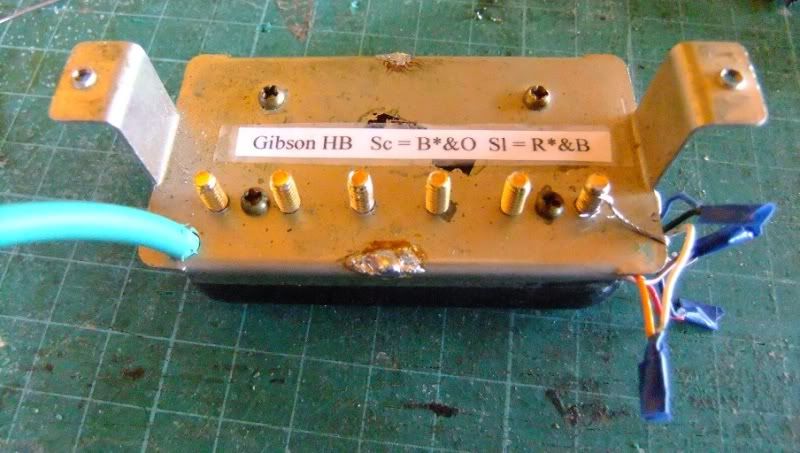 Connect the coil wires to the 4 cores, solder the shield wire to the base. I made sure the ground wire was tight to ensure that the other wires could be pulled or strained accidentally. Put PVC tape over the wire connections so no shorts can occur... IMPORTANT...if using an odd wire scheme, like with this cable, record the wire to coil scheme. in this case, red is hot, brown and orange connected for series and black for ground in the original series wiring...I typed a small code and taped it onto the back for reference. 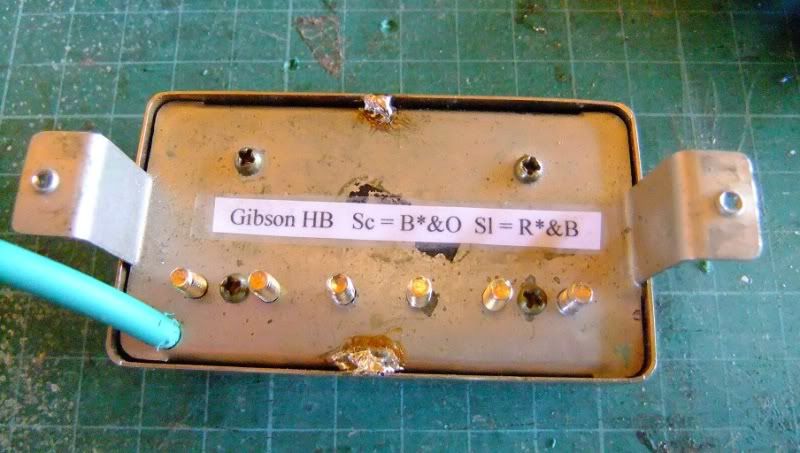 Solder the cover back together. Use rosined solder to help it flow, don't get excessive about it... 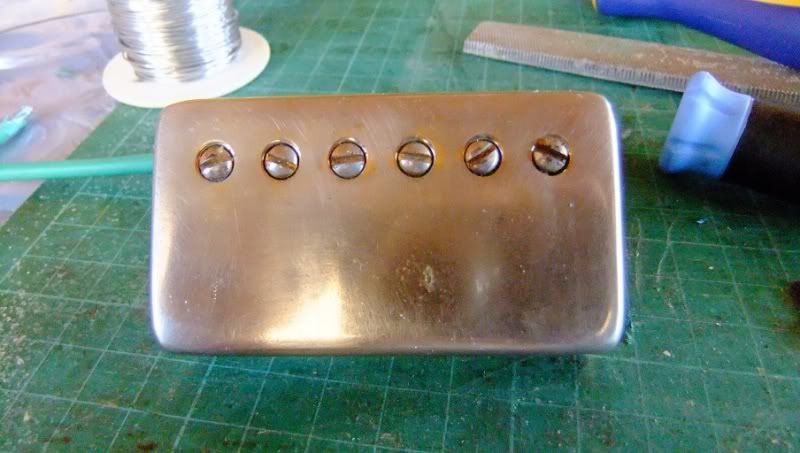 All done...when putting on the cover be sure that no wires are caught and all are tucked in neatly...and that the screw poles all line up well. Probaly worth checking the coil values too...3790k for the screw coil, 3750k for the slug... All good complete success for a conversion that will now allow for series/parallel/splitting/phasing capability. Some pick-ups split really well (my SD JB is well known to sound good split and this does seem to be the case on my strat). Phasing is usually problematic as the HB coils are so close there is a huge amount of cancellation...however perhaps the HOoP options might create an interesting flavour there. There are some great sounds for an HB to have partial splitting though something like a spin-split or spin-select control... Having some of the other coil can give a bit of hum cancelling plus power and body lacking in some split HB's...perhaps combine such a control into a tone control. ... For this project, I am thinking of including a series/parallel switch hidden into the F holes as this will give a lighter SC like sound without the noise of splitting. This is likely to be sufficient. Since I had the iron out, I took out the tape head pups, so I will add some pics at the hex pickup project thread linked above.
|
|