tom
Meter Reader 1st Class
 
Posts: 51
Likes: 0
|
Post by tom on Aug 27, 2009 19:44:15 GMT -5
Good, as tremolo ( Amplitude Modulation) is not an effect realizable in an electric guitar. It is usually found in an amplifier, often erroneously called vibrato by Fender. Vibrato ( Frequency Modulation) however, is an effect often found in electric guitars, but never in non-DSP based amplifiers. What's the difference between a Bigsby vibrato, a Floyd Rose vibrato, a Floyd Rose tremolo, and a Fender tremolo? None other then the manufacturer's perennial lack of understanding, they're all vibratos. They all do the same thing...... Gotcha !!  It's like the patella "tendon". . . Tendons attach muscle to bone. Ligaments attach bone to bone. The patella (kneecap) is a bone attached to the tibia, one of the lower leg bones. However, the patellar ligament is invariably and erroneously referred to as the patellar tendon by the majority of higher functioning hominids ! The patellar "tendon" does not exist (like a unicorn)  . . .the correct terminology is patellar ligament.  Now that that's out of the way. . .let's come full circle (a full circle must have 360 degress, right ??)  For clarification sake. . . Is it fair to say that SOME licensed Strat replacement necks with the "appropriate" specs/measurements (length, heel, etc.) designed to fit a Strat body with the corresponding "complementary" specs/measurements (neck pocket, bridge routing, etc.) MAY need to be tweaked (ie, shimmed) to attain the proper fit (providing that all of the obvious "adjustments" have been explored) ?? IOW, this can be considered a "normal variant" ?? If so. . .I feel like I am standing at the 359th degree and will start reading up on the proper way to shim a neck. ;D ;D Tom
|
|
|
Post by D2o on Aug 28, 2009 13:51:06 GMT -5
Good, but don't overthink it ... just dive in!You can use anything that will not erode over time as your shim material. I use children's construction paper for my shims - because: 1) I can buy a tablet of sheets of various colors, so hopefully I can choose a somewhat invisible color blend 2) It is thick enough that I am not cutting paper for very long, and 3) It has a bit of a rough-ish texture which helps to keep everything that I have piled positioned where I want it I just trial and error it on the basis that the neck is about 25" long and the neck pocket is a little better than 10% of that. If I want the strings over the neck pocket to be 1/2" "higher" than they are now, that height must be created at the neck pocket, but the effect of the shim will be transferred back to the headstock - one of the places the strings actually contact the guitar. So, if I want to create 1/2" I might try a shim of 1/16" - or about 1.5 mm. I try this by placing the shim in the pocket and setting the neck upon the shim, but I don't screw it in yet. I hold it firmly in place, as best I can, and run a thin piece of string from the tuners to the saddles (which I would lower to my desired height), see what it looks like, and add to or take away from the shim accordingly. ... bear in mind, Tom, this is exactly the same way I would do surgery on both the patella and the nutella! Good luck, D2o 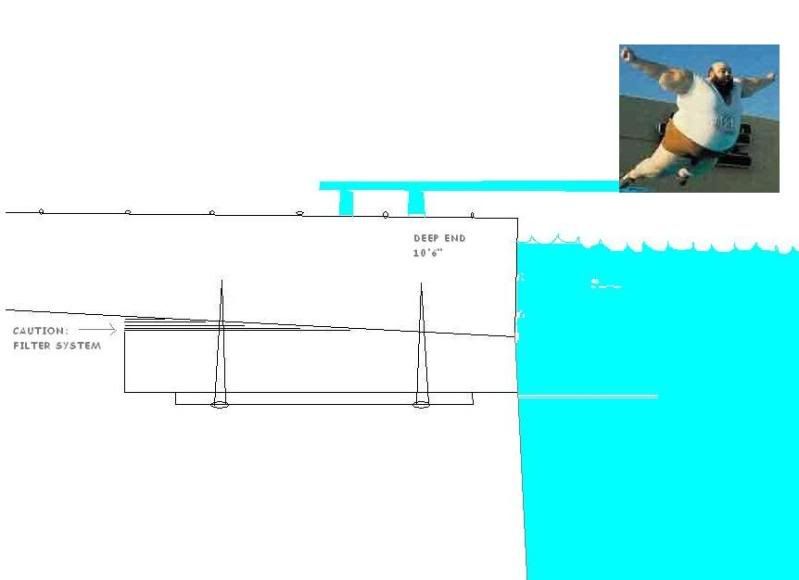
|
|
tom
Meter Reader 1st Class
 
Posts: 51
Likes: 0
|
Post by tom on Aug 28, 2009 15:15:16 GMT -5
|
|
|
Post by D2o on Aug 28, 2009 15:33:50 GMT -5
So. . .I guess a good place to start would be to "set up" the saddle heights, bridge screws, bridge height, bridge springs, etc., according to the suggested Fender "specs" and personal preference (to be in the ballpark) before removing the neck and starting the shimming process ?? (that's not converting a girl to a guy, is it ??)  That is what I would do, but I would also be interested in the opinions of others ... especially about the trans-gender question.  Reason #4 for the construction paper, it's easy to screw right through - which is what I do (but you have to keep everything well pressed together while doing so, or the pile of shim material will resemble a pile of shi ... um, it will end up all over the place. Cool! Let us know, too - if you would be so kind.  Good one! I think trying to fit that gut in that pool has something to do with that whole space-time-brane thing. LOOKS very painful ... as in it is very painful to look at that guy! Have a great weekend. D2o
|
|
|
Post by D2o on Aug 28, 2009 15:38:39 GMT -5
I forgot, whether you drill holes or blast right through the shim does depend on the material used ... if you use wood as your shim material, you should drill holes (and I am only guessing that you are best to use plywood, to avoid splitting the tiny shim?)
D2o
|
|
|
Post by cynical1 on Aug 29, 2009 0:59:26 GMT -5
One thing I've done for years is to use the 1" maple veneer on a roll. It normally comes with an iron-on adhesive, but soaking your strips in some Klean-Strip After-Wash, or any similar strong solvent, lifts the adhesive backing is about 5 minutes.
Light sand them to remove any glue residue and start stacking them in the neck pocket until you get the angle right.
The maple veneer strips are tough enough to drill through and won't compress over time like masking tape or paper.
Happy Trails
Cynical One
|
|
tom
Meter Reader 1st Class
 
Posts: 51
Likes: 0
|
Post by tom on Aug 29, 2009 9:09:00 GMT -5
These are all good ideas, thanks !
I pulled out a book that I bought in 1987 called "Build Your Own Guitar" by Bill Foley (didn't know I still had it!) and he recommends using sanding screen.
These are all good options with different qualities in terms of ease of use, longevity, etc.
I'll have to see what I can get into tomorrow!
|
|
tom
Meter Reader 1st Class
 
Posts: 51
Likes: 0
|
Post by tom on Aug 30, 2009 16:31:31 GMT -5
Hey Guys. Quick question before I set up the saddles and take the neck off. . . When I strung the guitar for the first time, I set the saddle distances (from the nut) according to Fender "spec". I noticed that in those recommended positions, however, that the high E and D strings have more than one contact point. Because the those two saddles are closer to the nut, the angle of the string as it comes through the bridge plate causes it to rest against the front of the bridge plate opening. Additionally, as it passes through the opening in the saddle itself, it rests against the front edge of that slot. And then finally, of course, it makes contact as it breaks over the top of the saddle. I "intuitively" thought this was kind of strange thinking that it doesn't seem to be good for tuning stability to have that many friction points. Then after I read that link to Callaham's site, I noticed that it was mentioned that the slots in his saddles are longer, presumably to avoid this. I wish I would have known about these before. Is this something you just have to accept as a "flaw" in the Fender vintage "tremolo" system as moving the saddle further away from the nut will affect the intonation ??  Tom
|
|
tom
Meter Reader 1st Class
 
Posts: 51
Likes: 0
|
Post by tom on Sept 3, 2009 9:14:46 GMT -5
Hey Guys. Quick question before I set up the saddles and take the neck off. . . When I strung the guitar for the first time, I set the saddle distances (from the nut) according to Fender "spec". I noticed that in those recommended positions, however, that the high E and D strings have more than one contact point. Because the those two saddles are closer to the nut, the angle of the string as it comes through the bridge plate causes it to rest against the front of the bridge plate opening. Additionally, as it passes through the opening in the saddle itself, it rests against the front edge of that slot. And then finally, of course, it makes contact as it breaks over the top of the saddle. I "intuitively" thought this was kind of strange thinking that it doesn't seem to be good for tuning stability to have that many friction points. Then after I read that link to Callaham's site, I noticed that it was mentioned that the slots in his saddles are longer, presumably to avoid this. I wish I would have known about these before. Is this something you just have to accept as a "flaw" in the Fender vintage "tremolo" system as moving the saddle further away from the nut will affect the intonation ??  Tom I guess I'll look at as a "flaw" !  After I posted this message, I took the neck off and tried out a couple of shims that I made with 2000 grit sandpaper that has the "loop" of the Velcro on the back. I used what I thought was best after a couple of "trials" (probably about 1.5mm or less after being compressed) and re-bolted the neck and tuned up. It did get rid of the buzz, but the action is still a little high. Not awful, but I would prefer a little lower. And not to go all Eric Johnson on ya'. . .but I noticed that it made a very appreciable change in the tone !!  Not better or worse, just different. I'll assume it had something to do with the change in the effective "heights" of the pickups. (and a little "mass effect" from the shim, perhaps. . .who knows ??  ) Again, if this thing were hanging in Guitar Center and someone pulled it off the wall and started playing it, they probably wouldn't think twice about the action, playability, or sound (maybe that's not saying much !!  ). I've seen and played a LOT worse ! But I guess when you're a "GuitarNut". . . So, I took it over to one of the very few techs/luthiers in my area to see what he thought. Part of me was hoping that he would say, "Man, this thing is great !! It doesn't need any adjustments !!" ;D . . . but I was more realistic than that . He did have a lot of praise which was nice, but after taking a quick look, (and I mean QUICK), he noted that it could use a little tweaking. He was kind of a "jumpy" guy and was all over the place while we were talking. He said that, in his estimation, the neck had an "S" shape to it and explained that there was more relief toward the headstock with more of a forward bow toward the body. He also stated that the frets might require some dressing. I've accepted the fact that the frets may need some tweaking (as I now understand that necks just aren't ready to pop on and play most of the time. . .), but I honestly can't see the curvature in the neck that he describes. Before shimming, the neck was pretty straight. After shimming, I can notice the change in angle (which I believe was the purpose of shimming) and a little more relief toward the headstock, but I can't appreciate any forward bowing of the neck closer to the body as he describes. I'll assume this guy knows what he's doing, as this certainly isn't my area of expertise and he's been doing it for years, but before putting blind faith in him and spending another $150, I'd like to get a second opinion from one of the other guys (custom builders) who I had some original contact with in the past concerning this project. Having said all of that, the original impetus for this whole project was to have this guitar ready for the 2nd annual Hoey cruise in November. And I've been thinking lately. . .does it make sense to have everything set up/adjusted, only to have it put on two 5 hour flights across the country ?? Would it need to be set up again after returning ?? Or would it be just be some minor tweaking that I could do myself at that point ?? My plan was to unbolt the neck and take it separately with the body as a "personal item" and carry on, respectively. I've never flown with an instrument an have been looking into all of the logistics. (I've heard some horror stories !!  ) Any thoughts ??  Tom
|
|