|
Post by 4real on Aug 20, 2007 14:07:26 GMT -5
Ok...still a lot of development going on...am just settling on the circuit design, it is very close, so I will be getting to the install with the above posted superswitch idea.
However...any ideas on changing the value of a push pull switch to 1k?
Will keep you updated but presently the circuit looks like being a very compact 35mmx3mm or so and about 10mm thick. That a battery, suitable switching scheme and the driver coil on an existing pickup and you are in sustain heaven...sound good?
pete
|
|
gunther
Apprentice Shielder

Posts: 25
Likes: 0
|
Post by gunther on Aug 20, 2007 17:05:28 GMT -5
Let me know when i can order one!
|
|
|
Post by 4real on Aug 21, 2007 4:58:47 GMT -5
Sure...I am very encouraged by the interest and have spent countless hours in the last few weeks. I think the circuit I have now is adequate for the MKI version.
I am working on the supply side of things to get the costs down for the first batch.
Very soon, I will be working on the installation side of things. I'd like to use a push/pull pot for the harmonic function but this would need to be 1k for the drive control...otherwise, I will be using the super-switch to operate it as per the type of diagram on the previous page.
However, this is just one option, you could use a 4PDT switch and a DPDT switch and the pot is optional (but very desirable) as there is a trim pot for this function on the circuit.
There will be some beta testing required and I will be supplying at a reduced cost to those with suitable guitars to test this on and are prepared to help with ironing out any installation problems. The eventual cost will probably be half the cost, size and complexity of the present units and several additional advantages, keeping the neck pickup choice and passive nature of the guitar and requiring less modifications.
So, the state of play at this point is that I have a basic driver design, and the machine to make it and a working improved circuit that is substantially smaller and easier to work with.
Only after a successful installation and a supply of components and wire can be established can I really do much and that is a fair amount of work yet...but it is coming along and seems to be a good start.
It will still be an aid to experimenters and give people a really good start to those holding back from playing with this project (it can get a little addictive). I already have people interested in developing their own circuitry designs, I even have plans for a MKII version. These could be plugged directly into the driver and installation. Similarly, this circuit could be used by people wanting to develop their own driver designs.
At this stage, I can only offer a simple single coil pickup adaption coil. This seems to work well for single coil pickup designs, but it may need some tweaking of a few different sizes, though I think this coil will be pretty universal.
If all goes well, an HB design may follow, though this will require two coils and a more elaborate pickup cover kind of thing.
How extensive I will need to make the "kit" still needs to be decided...will this simply be a coil and circuit or should I find a way to provide switches and other components (battery boxes, etc)...I really don't think this will be practical however. I will need to condense clearly the whole installation procedure for a standard type.
Any feedback on expectations for such a "product" should speak up while development is in play.
So...a lot of work to go, but tremendous progress in a relatively short time... pete
PS...I will be encouraging people to post their experiences with the device on forums like this and I hope it will encourage more people to explore the potential of their guitars.
|
|
|
Post by CheshireCat on Aug 26, 2007 21:22:11 GMT -5
Sure...I am very encouraged by the interest and have spent countless hours in the last few weeks. I think the circuit I have now is adequate for the MKI version. I am working on the supply side of things to get the costs down for the first batch. Very soon, I will be working on the installation side of things. I'd like to use a push/pull pot for the harmonic function but this would need to be 1k for the drive control...otherwise, I will be using the super-switch to operate it as per the type of diagram on the previous page. However, this is just one option, you could use a 4PDT switch and a DPDT switch and the pot is optional (but very desirable) as there is a trim pot for this function on the circuit. There will be some beta testing required and I will be supplying at a reduced cost to those with suitable guitars to test this on and are prepared to help with ironing out any installation problems. The eventual cost will probably be half the cost, size and complexity of the present units and several additional advantages, keeping the neck pickup choice and passive nature of the guitar and requiring less modifications. So, the state of play at this point is that I have a basic driver design, and the machine to make it and a working improved circuit that is substantially smaller and easier to work with. Only after a successful installation and a supply of components and wire can be established can I really do much and that is a fair amount of work yet...but it is coming along and seems to be a good start. It will still be an aid to experimenters and give people a really good start to those holding back from playing with this project (it can get a little addictive). I already have people interested in developing their own circuitry designs, I even have plans for a MKII version. These could be plugged directly into the driver and installation. Similarly, this circuit could be used by people wanting to develop their own driver designs. At this stage, I can only offer a simple single coil pickup adaption coil. This seems to work well for single coil pickup designs, but it may need some tweaking of a few different sizes, though I think this coil will be pretty universal. If all goes well, an HB design may follow, though this will require two coils and a more elaborate pickup cover kind of thing. How extensive I will need to make the "kit" still needs to be decided...will this simply be a coil and circuit or should I find a way to provide switches and other components (battery boxes, etc)...I really don't think this will be practical however. I will need to condense clearly the whole installation procedure for a standard type. Any feedback on expectations for such a "product" should speak up while development is in play. So...a lot of work to go, but tremendous progress in a relatively short time... petePS...I will be encouraging people to post their experiences with the device on forums like this and I hope it will encourage more people to explore the potential of their guitars. Definitely put me down for one and I would be thrilled to help with the beta testing. One suggestion would be to make a special thin coil for tight spaces, about the width of a single bobbin from a single coil spaced humbucker, like what you would find in a duncan mini humbucker, such as the lil' 59 or the JB Jr.
|
|
|
Post by 4real on Sept 7, 2007 1:14:08 GMT -5
Just a bit of an update. Turning a good idea into a prototype is one thing, going the next step to refine it and make the gear to make them on mass, finding suppliers and such is quite another. I am still progessing and putting a lot of work in at the moment.
For now, I have left the circuitry. This had got to the stage of a working design and the board and components have been colected to make a few for testing. This circuit measures 37mmx22mmx10mm.
The coil is proving a little more difficult. Obviously I can make them, but can I make them efficiently enough and to the kind of "finish" people would be willing to pay for and make it worth while.
I am on my fifth jig at the moment and been winding lots of coils with quite a few disappointments. Hopefully this new jig will do the trick.
It would be a lot easier if I could build them into covers...but I suspect not all single coils will fit a generic cover...hmmm
This brings me to a question. Could people measure any single coils they may have around or on guitars. I am making the core 5.5mm wide by 56mm long and the bobbin 15mm wide by 66mm long (max).
This seems to be pretty standard for a neck positioned pickup, let me know if there are any major anomalies out there that I should consider.
Well...I am getting a bit of interest, but it is taking a while as I said.
I have a design for making an HB version, but this will be quite a bit of an undertaking and be more expensive to get right. I don't see a rail version being made however, unless the pickup itself were rebuilt with a driver incorporated.
I can see where you are going with the "narrow" thin driver but there are design limitations. I did make things like this in the past, but I really don't see a "market" for them at this stage. Perhaps if this version is a success it can fund further developments...if not, well I'll have to leave it at that I imagine.
A major reason for this thing being as cost effective is that my idea exploits the magnets and cores already in the guitar and minimizes modifications. There is a lower material cost and labor involved with the widest appeal with my present scheme, so that is where my energy should be spent.
Anyway...the sustainer thread had a mini-meltdown for a bit there, but I think it is back on track. Various people, chiefly myself are going in different directions perhaps...which could be a good thing (covers more ground). The whole thread really needs to start again or even find a new home and if my venture is successful, it could be the catalyst for a new beginning using this version as a starting off point.
Having a ready made coil and circuit built will allow a lot of people to get involved who otherwise wouldn't and there would be less of the threads involving why things don't work, to how they could be made better, and utilized more effectively. Rather than kill off experimentation, it should open it up as once such a guitar is equipped successfully, it is quite simple to swap out a circuit of your own design or something someone else may have come up with to use with the driver, or to use the circuit to run a driver of your own design.
Anyway...just an update as I say and if people have a mind two, check out the pole spacing of thier SC pickups for me...
cheers... pete
|
|
|
Post by captainstrat on Dec 5, 2007 23:50:00 GMT -5
I like the way you wound the driver on top of an existing single coil! I was trying to figure out a way of keeping the neck position pickup and you just gave me the perfect solution - the other one would have been to wire up a preamp for the driver, but the results would be iffy at best tone-wise... Would that work on a Dimarzio Virtual Vintage? (I have some copper wire being shipped in a few weeks) I'm still trying to figure out a way of adding appropriate spacers to keep the driver coil in the top three millimetres (is there a reason for this?) ... My DIY version's going to be a whole lot 'rawer' than yours...no harmonic mode or anything, just gimme the controlled feedback (I'm still aiming for that Steve Hackett sustain  ) and I'm happy! Thanks for posting man, I was wondering what the principle behind the sustainer was!
|
|
roger
Rookie Solder Flinger
Posts: 19
Likes: 0
|
Post by roger on Feb 25, 2008 6:42:23 GMT -5
4real, Hi, i'm also new here in the forum. Cool sustainer you have. First, can you explain how the system works, i'm a slow learner and not highly technical but have some tiny guts  Second, is there a difference between Fernandes and your sustainer in design and in sound? Cheers, Roger
|
|
|
Post by ashcatlt on Feb 27, 2008 16:45:33 GMT -5
4real doesn't come around much. You'll notice his last post was in September.
I'll try to answer the basic questions there.
First, it works by taking the output from the pickups, amplifying it, and then sending it through a coil of wire. This creates an oscillating magnetic field. In a lot of ways, it's the same thing you'd find in the voice coil of a speaker*. In this case, though, that magnetic field exerts a force on the metal strings, pushing and pulling them and causing them to vibrate.
Since the signal that is causing the vibration is actually coming from the string to begin with you get a feedback loop, and the string will sustain forever after a very small initial excitation force is applied.
4real's been through a number of different designs with different goals, and I can't say for sure exactly where this one ended up. In essence, though, it's the same thing as the Fernandez version. The main difference is that while the Fernandez is meant to replace one of the existing pickups - and be used as a pickup when it's not in sustainer mode - this one is meant as a retrofit. The coil itself actually just goes on top of an existing SC pickup, so you can use whatever fancy boutique hand-wound special thing you've chosen for its tone. It's a little less invasive to install.
As for sound, I'm not sure that it will be much different. I know 4real has worked in a "harmonic" mode, which causes it to feedback an octave higher. I'm not sure if Fernandez has that, but the e-bow does.
I know that he was working very hard to get it to play nice with adjacent pickups. That is, he wanted to be able to, say, put the sustainer coil on the mid pickup and be able to switch it on while playing through the neck or bridge without causing unwanted EMI interference or feedback. Not sure where he's at with that on this one.
He's also done a lot of experimenting with evening out the response so that the higher strings (with less mass to be affected by the EM field) will react as strongly to the sustainer as the fatter, lower strings. I think with this version it's a matter of filtering in the amp section of the circuit. Just basically amplifying higher frequencies more than the lower ones.
Anybody got any other insights?
* Of course, in the case of a speaker, the voice coil, connected to the cone, sits in a gap within the magnetic field of the big magnet hanging off the back. When electrons start flowing through the coil, the EM field created causes the coil to move in relation to the magnet, which is fixed in space. The coil in the sustainer is fixed in space, and so can’t move. The strings can, though, and they do.
|
|
|
Post by flickoflash on Aug 12, 2008 15:51:51 GMT -5
I would like to make a driver in a traditional strat pickup though in a 7 string version. I have purchased a sustainiac stealth Pro system to opereate it. Is it possible to make a driver that looks like a vintage PU.( Believe I have seen a early Fernandez sustainer that was made this way ) Any suggestions 
|
|
|
Post by flickoflash on Aug 16, 2008 22:22:04 GMT -5
I would like to make a driver in a traditional strat pickup though in a 7 string version. I have purchased a sustainiac stealth Pro system to opereate it. Is it possible to make a driver that looks like a vintage PU.( Believe I have seen a early Fernandez sustainer that was made this way ) Any suggestions  The guys at sustainiac were kind enough to send me a small shield plate that is put on the side of the driver close to the middle. It is use & adjusted its location to deter feedback when using a angled pickup in the bridge. Anyone have any idea why this is ?
|
|
|
Post by 4real on Aug 17, 2008 4:13:46 GMT -5
Hi flicko.... I don't get over here that much, I just drop in occasionally and recommend it to others because it is the best forum anywhere on wiring ideas... To answer your question, the idea of that little plate seems to be to reduce some of the electromagnetic interference that can happen with the driver between the source/bridge pickup and the driver. They seem to be suggesting that it has something to do with the angled bridge pickup as on a strat...this may be so, but the patent also suggests that it is to help high string drive by focusing the field and mounted uner the high strings (which is in fact further from the bridge pickup when it is angled)...so it is a bit debatable what the real reason is. Often it is not used, kramer had one the full length of a rails styled driver...I don't use these things at all typically. Generally, the PG sustainer thread is the place to ask as I don't get email notification here and to keep the bulk of things in one place. .... For people who enjoy statistics, the PG sustainer thread has now been going since 2004 and has 4037 posts and had 173,292 visits in all that time! In the last week or so it has attracted over a thousand visits...do I get a prize! A lot of new visits have been in response to my new guitar which people here might enjoy... A thread on the guitar is here for more details... projectguitar.ibforums.com/index.php?showtopic=37370 The Blueteleful Telecaster Project... 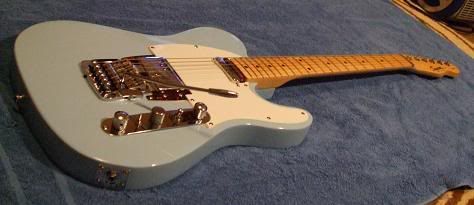 This was a squier 25th anniversary model and everything but the neck and body have been replaced with premium parts or custom made components...even the paint is new! Of interest here may be the controls... 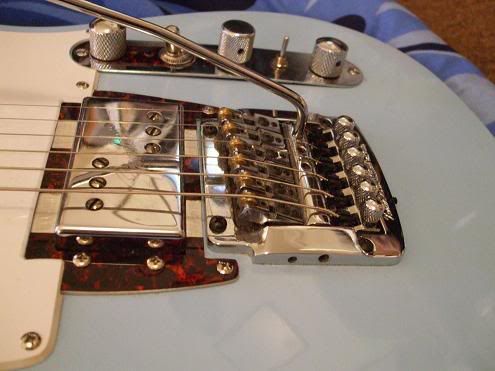 And the pickups...  The guitar has my latest sustainer and on this guitar is working amazingly well. The driver surface mounts next to the neck pickup with double sided tape to the pick guard without modification.  I know you guys like wiring...so this is how I fitted all this into a tele... 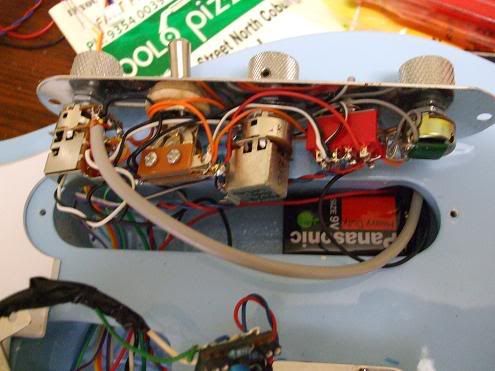 I angled the switches and pots so that they slightly overlapped and achieved a better switching angle than straight up and down anyway...plus a kind of symmetrical arrangement. It worked out neat and I was even able to put the sustainer battery in there for easy access...the tiny circuit sits under the bridge HB. I have put the volume up front within easy reach and out of the way of the tremolo arm. The back pot is a tone control. The middle knob controls the drive amount and the mini toggle the sustainer on and off/bypass function. These pickups are amazing...a real vintage "wide range" Hb and a 2008 SCn neck pickup...both totally silent. The selector chooses N~N/B~B as you would expect but by lifting the volume up, the pickups are out of phase and you get a very nice quacky sound...possibly aided by the large size of the WRHB in the bridge...one of my fav sounds on this guitar. The drive control lifts for the sustainer harmonic function. So...even though I had been giving the sustainer a rest for a while...as always interest and then...well I get sucked back in. So...for tele lovers, this is one amazing sounding and playing guitar and looks great too... pete/psw/4real!
|
|
|
Post by newey on Aug 17, 2008 7:47:46 GMT -5
4Real- No prize for another forum's thread, but this thread here now runs to 7 pages and you just hit 100 replies. Don't know if that's a record for us Nutz or not, but certainly merits a +1! And also for the Tele which is gorgeous. Very pristine wiring job and a nice refinish. I'm not a big Floyd Rose fan, but a nice bit of routing to get that into a Tele. Some backside photos to show all that would be nice as well. And don't be a stranger . . . 
|
|
|
Post by 4real on Aug 17, 2008 16:21:33 GMT -5
Thanks Newey... 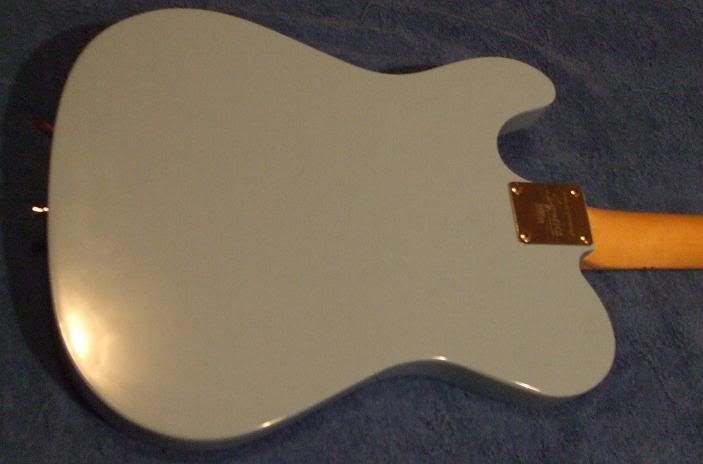 It's not a floyd but a Kahler Hybrid. A small screw at the back of the bridge can convert it to a fixed bridge. It is a cross between a full floating tremolo, but has a feel a bit like a bigsby. The strings roll over a fixed bridge while behind there is a cam mechanism. The design means that tuning will not go ut with string damping like a fulcrum strat and when using the bar, the strings stay level with the pickups and frets instead of rising with the bridge saddles as on a strat. The rout is small, about 1" deep and less than 2" into the top only. So...nothing going on in the back.  The real surprise was the great sound you can get with these pickups out of phase with each other. The pickups sound great and the guitar has a really bright fender tone and definitely sounds like a telecaster, but also quite a unique sound with a bold Kerrrrrannng like tone to the bridge pickup. The fender "wide range" HB sounds nothing like a typical HB and is significantly bigger with wide flat coils and magnetic adjustable poles. 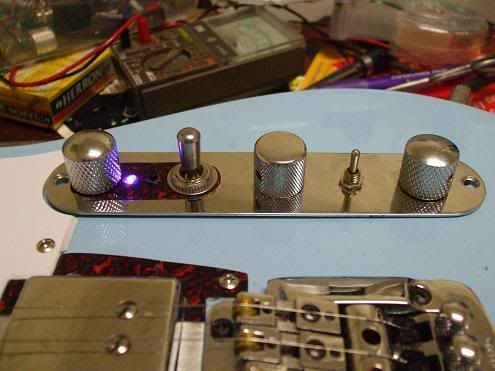 I used some tortoiseshell sheet to cover the switch slot and above you can see the light that comes on when the sustainer is switched on. I had to make the HB mounting "ring" from a sheet of aluminium sheet with "racing stripes" of tortoiseshell. I even had to make the drive control pot...it is 1k so I took apart a 500k switch pot and inserted the guts of a compatible 1k to get the required value. I am very happy with it obviously... pete 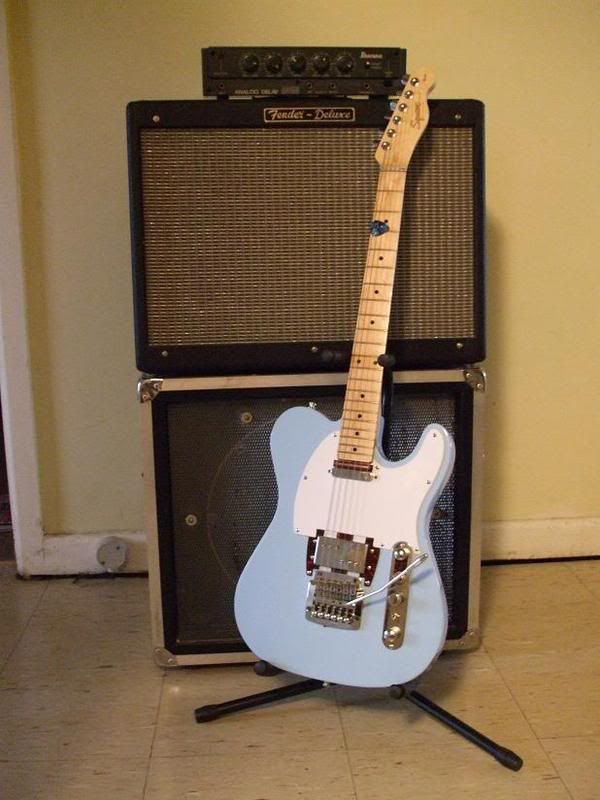 Oh...Above, the amp rig I run it through, fender hot rod deluxe with a 15" ported bass box and my AD100 delay.
|
|
|
Post by billyluthier on Sept 21, 2008 1:50:33 GMT -5
how many watt does the sustainer amp produce? 1,5,10 or 20 watt. i'm always on quest to make professionally. almost there. will show you pic in due time.
|
|
|
Post by newey on Sept 21, 2008 7:23:34 GMT -5
Billyluthier:
Hello and welcome!
4Real has a long-running thread on the Project Guitar forums on his DIY sustainer. As he indicates above, it's best to PM him there with any questions as he only pops in occasionally here.
|
|
|
Post by 4real on Sept 22, 2008 22:53:01 GMT -5
Hi...sorry about not being around too often...this board does not send alerts to thread or PM postings...so hard to keep track. I hope this does not suggest as it reads...I have a long established prior art on my developments on this and there are plenty of patents already on the concept. I have been very generous in my sharing of my experiences and successes in this project, but I have and will resist those who wish to profit from it without any input. Fortunately, all that have tried to date have failed, but I certainly will not help willingly anyone with such intentions...obviously. With a post like this, and all the information (the main thread alone is 275 pages now) that I and many others have shared over 5 years on this project with people all over the world (spanish language forums seem to be a breeding ground for such activities for some reason, but I have spies)...it would appear that you have not yet grasped the basics of the concept or read even the most basic of material. Still...I may have misunderstood your use of the words "i'm always on quest to make professionally"...in which case, some clarification may be in order. It may be a translation problem and if so, my apologies. .... I am still working through some difficult personal things at the moment, but a semi commercial version of my work is planned and fairly well advanced. Over the last year all so, some of the more recent developments, circuit designs and coil construction details have been kept pretty well secret. The circuit in the tele is my own design for instance, the method and machine that winds the epoxy coils as well as the actual material used is also well secured. I spent $100 in epoxies to find something that would work satisfactorily, but in addition to not providingt this information, the method is not cost effective nor safe for DIY so there is no real need to encourage others to go down that road. Entirely satisfactory results are obtainable with conventional circuits and documented coil making techniques. A recent post at PG even had a new person make a decent replica of the tele driver concept with the normal wood glue method (if not as "professional" looking) that I suspect should work well. .... Since I am here...voting for PG's guitar of the month (GOTM) will be starting very soon...see the entries here... projectguitar.ibforums.com/index.php?showtopic=37712&pid=394620&st=0entry394620The blueteleful tele is the first guitar I have entered in 5 years there and is the showcase for the sustainer project. As there is no "sustainer or guitar modification of the month" I'd appreciate a vote if you have a mind to. The entries this month are varied and of very high quality...but you never know. Part of the idea is of course to help boost my confidence to do something to make this project more approachable by at least offering premade circuits and possibly pre wound coils....of which the tele is a prototype concept. I have also been contacted by a member here who looks like he might be embarking on this project too...so it will be good to get some varied feedback...hahahaha pete
|
|
|
Post by D2o on Sept 24, 2008 9:18:34 GMT -5
Pete, I was glad to see you make clear that you are not discussing your sustainer for the sake of charity. I had kind of wondered how all of that important behind the scenes stuff works, so I am glad you are closely guarding the real meat and potatoes. Anyway, you mentioned email notifications - I don't know if you knew about this. I hope it helps. Cheers, D2o
|
|
|
Post by 4real on Sept 28, 2008 16:41:07 GMT -5
Honestly...I don't know what I am doing...things just grew... My own "style" of playing (blues, motown/stax and solo arrangements) really does not need or lend itself to the sustainer at all...it is a fun thing to have though and has it's uses... This is one of the reasons I personally have tried to make the sustainer not adversely affect the performance of the guitar...I want my own pickup choice, be able to run without a battery if necessary (without the sustainer of course) and for it to run clean with an action and string gauge that I like... ... The secrecy thing, I have copped a bit of criticism over the years, the main thread has been running since May 2003! I tend to look at it like the "open software" thing. I provide information and encouragement and lessons learned (mainly from failure) to help others make their own. As things are DIY and each guitar and person is different, others will approach things in ways I wouldn't think of... In return...I get another "expert" to help with future questions and a different perspective and solutions to the project...as do others...so we all win! For example...Warmstrat recently emailed me direct (due to not being around as much and it is sometimes easier...or posting on the main thread is good too) with this project... guitarnuts2.proboards45.com/index.cgi?board=wiring&action=display&thread=3593There are a significant number of things here that will require some nutting out and on a forum of "new brains" to help with it. Already progress is being made in one of my pet areas...installation and switching issues...that is not fully covered over at PG. So...warmstrat gets a sustainer, you guys get to participate and nut out solutions...I have an answer next time someone asks how to install it in a complex wired guitar (something I have a project with too as it happens)... The "not for charity" thing is where people appear not to be wanting to "put in" or planning a particular project. There have been people who wish to take the idea, brand it as their own and take it to another forum for the brownie points associated with a remarkably long running and popular thread (normally they get egg on their faces because the first reply will ineveitably...have you seen this...and post a link to the PG thread!). There are others who see the popularity of the thread and $$ light up in their eyes...all this free info! It would never have got this far if I had not been given the support and encouragement to keep at it early on, and a lot of "my ideas" were inspired by others who contributed. There have been some things that I do keep guarded. My own circuit design I spent a lot of effort on and is not something I want to "give away"...what you can have is any number of generic workable designs. Some of my new epoxy coil things are not DIY and I would not want to encourage it, my wafer coils are particularly tricky and require a machine...also "secret". A DIYer wont need it to make a coil for themselves...so why share that? ... So...where the is a benefit to "the project" (ie myself and others) where someone is actually going to do the work...I can be as charitable as all get-out (it's my nature anyway)...but where it is a matter of me doing the work or there is no benefit...well, I think I deserve some more tangible reward! ... As I say, I really don't know what I am doing. I am sure that there are opportunities for people to "rip off" mine and others ideas for their own ends...but there will need to be some significant work on their part to get there for a commercial proposition and I am not in the "business" of helping them do that... ... The behind the scenes stuff...although I do a lot less of it now...is simply following through with an idea, taking the multiple knocks and failures...then posting the results. Even better, is when someone else takes on the "work" and knocks and failures and I just encourage them from the sidelines and help them avoid some of the "hits" I have taken in the past... I don't even know if that makes sense! I have learned to bookmark this thread though...so I should be notified in future and reply more regularly... pete
|
|
|
Post by billyluthier on Oct 4, 2008 3:12:26 GMT -5
i'm so sorry. for my typing that is. i meant i'm on quest to make guitar professionaly. professionally means one guitar every two month. on a quest means mastering the art of shining epoxy finish. will show you pic means i've made a superb double neck guitar. was thinking whether to add sustainer to it. i own and play in my restaurant so making guitar will not be my source of income. good wit my hand at handycraft but like is like a leper when it come to typing. ha ha. sorry again.
|
|
|
Post by andrewraharjo on Jul 21, 2010 12:23:09 GMT -5
somebody please tell me the tutorial to do this...please help me... I want to build this one..for a God Sake..Please help me...sent me a mail....
Thx....
|
|
|
Post by D2o on Jul 21, 2010 15:08:14 GMT -5
Hi Andrew, and Welcome to GN2  Yes, it is quite a cause for excitement! Have you gone through the whole thread? There are links to whatever resources the creator, 4real, wants to make available. He has been extremely generous in sharing information, but I am not sure there is enough information for anyone else to completely build this on their own - I believe some aspects of the project are well guarded (patents applied for, etc.). He does not come around on a regular basis, though has checked in recently. Some members had expressed interest in buying a unit - as built by 4 real. I don’t know if it ever got to the point that he is building and selling them. He'll likely be along at some point to respond to your plea. In the meantime, if you care to view his profile you will see an email address where he can be contacted … perhaps he can give you further direction on options for building or buying a unit. Good luck! D2o
|
|
|
Post by 4real on Jul 22, 2010 18:23:23 GMT -5
This thread is back again...didn't realize it was so long! 4real aka psw aka pete akaWell, things are personally a little tied up at the moment and the original sustainer thread is almost a decade old. The original 'sustainer strat, phaso-caster' still exists but I literally wore it out...it still works however. I have been corresponding with andrew above in recent days, language barriers and lack of experience is perhaps going to be an impediment. I'm helping a few people along, perhaps another 4 at the moment and the profile seems to be fairly similar... With this renewed interest and the time I am having to put into it, I might need to do something more public so people can learn from each other and perhaps make this material more succinct. ... The "skinny" is that it is a little deceptive in it's simplicity, but for this reason this seems to make it tricky for people to 'cut corners' which this thing won't tolerate too well with some basic principles. So, here's the scheme in a nut shell... An elongated coil (as per a pickup) wound to a resistance of 8 ohms with 0.2mm winding wire and solidly wound in glue (PVA recommended) to prevent any internal vibration in operation, and to a thin profile (3mm typical) close to the strings...produces a driver with the qualities (inductance, resonance, speed, application, etc) to sustain all the strings and generate harmonics with very simple amplification circuits. This is a tried and true formula and works, the wire in particular is important to arrive at the appropriate conditions. This can be implemented in various ways, as a stand alone driver or on the top of a pickup itself as per the "phaso-sustainer strat" and in other variations with more technology (such as the compact surface mount version on my tele or the 'wafer coils' which are even smaller and will convert strat pickups) Now, the driver is the heart of the thing meaning that any number of suitable simple amp circuits suitable for the application can be used. People seem obsessed with the circuit details. The requirements are a small power amp, the old standard LM386 chip amps have proven to be up to the task and I still use them and they can be found in things like practice amps and the eBow despite being quite old, they are reliable, tweak-able, readily available and cheap. You can often find kits of such circuits even, and this was what I used early on and in the phaso-sustainer-strato guitar. You also need a preamp or buffer that will accept a high impedance pickup signal and bring it down to something suitable in impedance for the amp to work with, it is vital also to prevent loading because the signal from the bridge pickup needs to be split between the circuit for the sustainer and the output of the guitar into the amp without 'loading' and loosing or colouring the tone of the guitar. Ok...so... bridge pickup -> buffer stage -> power amp stage -> driver The bridge pickup is an integral part and can come in a lot of varieties and power and tones. They all will work but the amp circuits may need to be tweaked a little and the character of the circuit can produce different responses. Pretty consistently, with an L386 type circuit I also use a 100uF output cap in place of what might normally be found (typically 220uF) as I like the sound and it provides a better balance to the strings and helps the difficult high strings to be driven well. I also like the harmonic "bloom" that is typical in the lower octave. But there is lots one could play with in tweaking circuits and filters and such to produce different responses and harmonic effects. To generate harmonics from any note is interesting. Basically all you need is a phase switch on the driver wires to reverse the signal and the driver will dampen the fundamental and drive the next highest harmonic which will vary with the fretted notes. ... Installation is a whole different thing... If there are any other pickups than the bridge on the guitar, these coils near the driver will work like a transformer in conjunction with the driver and currents will be induced in them creating noise or even squeal and interfering with the functioning. So, I have found it necessary to use a 4pdt switch to deselect both the hot and grounds, generally taking out the entire selector array, reconnecting the bridge pickup only and turning on the power. Driver leads and circuitry may need to be handled carefully as EMI may radiate out of these components but this is generally less of an issue and depends on the guitar....with the phaseocaster I rand the driver wires through the trem cavity so they would be away for other pickups for instance as the single coils were susceptible to picking up this noise. As a result of the many 'failures' that do occur through inexperience or cutting corners, (such as not using the wire specified or not being able to build or tweak a circuit, etc)...and even in my own work with these things...one should always build the basic components and test the thing so you know it works outside of the guitar and before one considers any modification. This means, taking a feed directly from the bridge pickup to the circuit and holding the driver over the strings, over the neck and well away from all pickups. Only then should one even consider modifying or installing these things. Unfortunately, modding a guitar is often the first thing people seem to do...hmmm ... Now this is the very basic working formula for such a device and seems to have stood the test of time. I have tried many other ideas and variations but this remains one of the more successful and can run, unlike commercial units, without complex circuitry and uses no power when off. It is also suitable for many to DIY but not really great if one thinks that wiring a guitar is difficult For my own work I have an extensive list of necessary criteria for success that greatly influenced the design. It should also be noted that the entire thing is a balancing act and some of it is apparently counter intuitive. It works largely because of the efficiency of this kind of coil specifications. The windings will become magnetic when powered by the circuits AC signal, this is not a "microphonics" thing so much, it will actually try and vibrate and many poor drivers will audibly "sing" so the glue potting thing is vital, it has to be pretty solid and effectively damped. If the thing is squealing or perhaps high strings not responding too well...more power is only likely to make things worse! The analogy which is accurate is that you are creating a feedback loop. If you have a mic and a PA and you point them mic (pickup) directly at the speaker (driver) you are going to get squeal completely overwhelming it's function. Now, you can perhaps move away from the speaker till it stops screaming and or turn it down. The result is that for a given distance you can only apply so much power before oscillation feedback takes over. Now, the balance is to create a system where one can get the strings singling without squeal and with the restrictions of the distance between the pickup and driver enforced by the nature of the guitar. Bridge pickup, neck driver. The further apart, the better. One of the 'innovations of the design is to make the coil compact and so the range of influence of the driver is directly under the string and less along it to the pickup. So, the thing is to make something efficient enough to work with the power that you can apply to it to get the result required. The hurdle many have is that this will take a little ingenuity, lateral thinking, trouble shooting and 'arts and crafts' skills. The easiest way to do this successfully is to use an old single coil pickup, strip off the windings and 'block it up' leaving 3mm at the top, wind it exactly as shown in the tutorials with glue from the start with the right wire and to the right resistance and make sure it is neat and solid. ... Here is another tutorial of my design as well as a place for circuit software and a suitable circuit layout.... diy-fever.com/misc/diy-sustainer/It is in pictures much like mine has been, but apparently for many, including andrew above (although youth, inexperience and the language barrier is a problem), this is too difficult to follow. I can't see it being able to be made too much easier...you are aiming to build this... 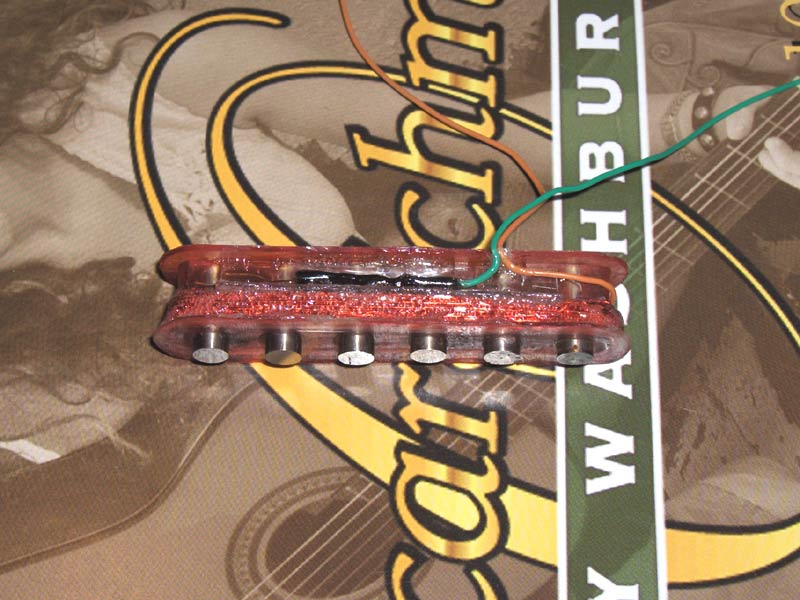 A perfect example, solidly glued, took about 15 minutes to wind, right wire, right resistance, neat. The 'blocking could just as easily be made with cardboard as once taped up and put in it's cover no one will know. ... Because most people who publicly post problems with their project are having problems with this thing, there has been some perception that it doesn't work or is too hard of the information is not available all the way to conspiracy theories that I have been withholding vital information. I don't mean to pick on andrew, he is one of many and typical of the people that I routinely deal with, I have sent 4 emails so far pointing to all the easy resources such as the link above and he seems not to understand that quite, this does not bode well. Here's another one that I have been 'helping along' with perhaps a dozen extensive emails over a couple of months and no language barrier... 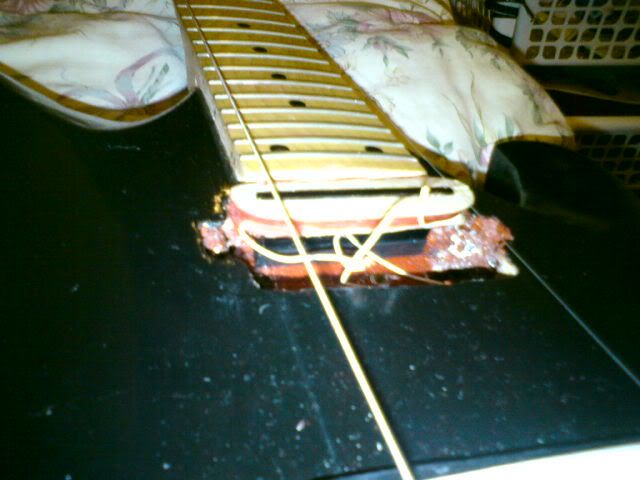 OK...balsa wood driver a bit scrappy, but it is glued pretty solid I believe and it's not the looks that count. For all the guiding along it is getting there. This particular person has for a year suggested it wouldn't work and failed on numerous occasions across three forums but fails on numerous areas. He started by taking a chisel to the guitar to fit things in it...so not building testing to success before installing as advised. Although explained many times and proven it to himself numerous times that not "any coil" will work and that the glue matters, he still is having a little trouble finding (in a local store!) 0.2mm wire and so using 0.15mm with predictable results. It is just producing with a lot of noise enough power and speed to drive the low e string. However, the reason it is not working is because of a fundamental refusal to follow the design and taking the attitude that "there are many ways to skin a cat"...however, this is not it and wishful thinking and over enthusiasm won't cut it. Ironically, so far, after finding out that originally he was using an unbuffered ipod amp kit that was not suitable and building something that was from the tutorial, and building at least a coil to the main specs, he is so close...for want of the wire! Unfortunately it can take weeks before some people even reveal what they are using because they think anything will do. Now, the other thing to note is that this is a 24 fret guitar, if it has super light strings, also a challenge, and probably a big powerful HB as well, pushing the tolerances to the max. The pickup is close to the driver and so the thresholds are reduced, thin high strings mean less metal for the driver to work with. Now...if you are going to push the design even further like this you are going to have to have a very efficient driver and there can be no 'short cuts' in construction or specifications. But he is so close...I am persevering here because his success may counteract all the bad publicity that came out of his fumbling and nativity. ... But you know, it has been about a decade this thing has been going on and I am happy to help, but people need to be realistic and be able to understand what they are getting into. Most people here are fairly adept at things and I expect little trouble, possibly improvements....but we also see soem very basic questions obout wiring a pickup and this is much more involved than that. I would suggest that if wiring a guitar seems daunting this project is not for you at this time or you will have a steep learning curve. ... However, for all the people who publicly diss the thing, and often publicly without ever even trying it (and in the last 18 months often personal attacks on me resulting in the forced closure of many threads at PG) there are many dozens of people who have built these things without any help and have emailed me to simply say thanks, worked perfectly! Unfortunately, the success stories don't get the profile and require only a simple post at best while others will hammer away for literally years. ... Some may be aware that I am considering reopening this thing publicly, but it can be a lot of work on my part and I think that the resources would need to be done over to be clearer and a 'core' of people that are interested and capable be involved to field such questions that may arise. So, considering... Otherwise, it needs to be kept in perspective. It is a great device and a fascinating project...it sounds like a really loud guitar, harmonics and sustain without the need of distortion or any volume and sounds much like an 'ebow' I suppose, hands free, multi strings...even in the most simplest incarnation. ... There are 'secrets' to some of my work. I do have my own circuit these days, mainly it is far smaller (about 1" sq) and has some limiting and an improved drive control. However, the system is much the same and sounds much the same as you can achieve with the simple DIY version. There were many new versions of drivers and how they were constructed, but still the design is pretty consistent in principle and these things are not really a DIY proposition regardless, so who really needs to know what I had hoped to be a "commercial" proposition (10 years work I have only lost money helping people!) You know, I am also considering releasing some things like circuits and possibly drivers, but it would have to be cost effective and subject to my time and the ability of the buyer to properly install and troubleshoot the things. The main reason that I stopped pursuing it is that it is not "simple" and the resulting hail of "it doesn't work" posts is simply not worth it when the failings are not in the design or my circuit or driver (all of which I test of course)... And, perhaps I will be opening up a public discussion about such things if there is a genuine interest and I am not going to open up a can of worms in it. ... And, you know...life's short and there are plenty of other things to work on besides 'sustainers'! GN2 has been invaluable to doing some wiring stuff and the 'experts' here are fantastic. I just completed the 20-dual scheme without problems (with GN2 help though!) on my new guitar and made lots of neat tweaks. I have plenty of other ideas, many to do with tremolo systems...I'm about to revisit b-bender ideas as well. Originally, I didn't intend for the sustainer thing to take over, I was actually embarking on some different kinds of pickup ideas and it just took over. Some of these things are perhaps even more exciting, especially to me these days, than a fascinating but useful, but in the end, an 'effect' like a sustainer.
|
|
|
Post by newey on Jul 22, 2010 19:04:57 GMT -5
psw-
+1 for the thorough elucidation of this project. You put in a ton of work, obviously, and it's a shame that you get attacked personally when someone's rashly-undertaken project goes awry. (And, we won't let that happen here!)
The cautionary tale is also a good thing. Certainly, you don't want to discourage folks, but anyone contemplating the project ought to know that this is advanced stuff.
I am unclear on your use of the word "blocking" with reference to the pickup loom cannibalized for making the sustainer coil.
One question you didn't address. I suspect the amp, and also its particular EQ settings, make a significant difference in the amount and quality of sustain one achieves. What amp and settings worked best for you with the sustainer?
|
|
|
Post by 4real on Jul 22, 2010 20:30:49 GMT -5
Ok...well the design calls for a thin profile coil up close to the strings. A normal pickup bobbin is likely to be say 10mm to wind on, so you want to "block up" all but the top 3mm of the bobbin to wind onto.
The good one in the picture was done with some plastic and is neat, but cardboard or wood or anything that blocks up the bobbin is fine.
You need to have 0.2mm insulated winding wire and the core in particular alters how many winds it is going to be, generally about 165 turns is about right but will vary quite a bit, so measuring with a multimeter occasionally is advisable. The amp expects 8 ohms but inductance changes with frequency, so I've found 7.5-8.5 works ok if it isn't exactly accurate.
The glue thing is important, some have doubted my strong suggestion of using PVA wood glue, but there are good reasons for it. My newer more advanced coils do use epoxy but this is expensive stuff and not the kind of thing you find in a hardware store to be successful. PVA is insulating (it's effectively liquid PVC tape when dry) and has fair filling properties (all wound round wires will have a fair bit of air in them)...it's cheap safe and reversible and cleans up with water...and it works. I am adamant to avoid such things as super glue as this kind of thing has no filling qualities, can strip the insulation, has no give, is unsafe...messy and non reversible!
You can see by the example shown that it is perfectly adequate to the task if done neatly and will re-insulate any points you need to scrape to take a resistance measurement from.
Yes, it can. But it depends on the kind of response you are after, the type of guitar and particularly the source signal pickup...so many variables.
Pretty consistently I have used LM386 designs, very much as per the data sheet for that chip for high gain mode to keep it stable, few parts, fairly indestructible and runs of a 9 volt happily and or over heat and shut down amongst other things. More distortion than many might want, but there are limits to these things. You can get a kit easily in oz called the CHAmp in most electronics stores and that's what is in the original circuit I used with few mods (it is essentially the data sheet circuit).
The main mod that I consistently do is to replace the typically 220uF output cap with a 100uF. This tends to balance out the easier to drive slow thick low strings and frequencies with the harder to drive high strings pretty well. It also tends to produce a lovely "bloom" where note in the lower octave (below say C on the fifth fret G string) in the fundamental mode. So, this is perhaps considered an EQ mode. More EQ controls could enhance this effect to create more harmonic effects, you could sacrifice high string response with the higher output cap, if really keen, make such mods switchable.
The idea of these things was to present the basics for what would work and hope that people would find their own modifications and responses and share them with others over time. There are a bunch of different circuits offered up, but not quite as I would have hoped. It isn't really for me to "prescribe" what others would want and there have been complications when I do...I know it seems perplexing that there isn't A Circuit or pete's circuit!
In the early days, I also modded simple preamp kits and various simple op-amp things. Generally I've found cleaner less power to be an advantage with most pickups. So, if you ahve a great honking HB in the guitar, then you are unlikely to need to add preamp gain as this will only add more distortion into the driver signal. A buffer will likely do. The less power to get the required effect the better.
As I have a bit of experience now, my drivers are very efficient but stick to the same design. I tend now to only use a buffer stage.
Now...I eventually learned enough to make my own circuits, and I do have my own circuit these days. However, it is not that different to what people can make for themselves. It can be a little expensive to make with SMD parts and high quality components, but there is no secret that it is still LM386 based.
The difference in mine is that it also includes some limiting and power saving features and circuit protection and LED power on board and is very small. So, my circuit reduces or even cuts power momentarily and in short bursts as the strings momentum is enough. All these kinds of circuits tend to be limited by the power rating and particularly a battery supply, they can only produce so much power. This is itself a limiting factor that stops the feedback loop just growing and growing. My new circuits have a drive control and auto limiting kinds of things in it to use and enhance that a little more.
Still, the circuit is not the "secret" the driver is. Plus, if I were to even supply the tested components, many would have trouble working out just the install and it is very hard without the guitar in front of you to troubleshoot things.
So, there needs to be a level of skill and ability really. It's not that hard at all, there are wiring schemes that are far harder and more time consuming. However, you can see in this forum exactly how difficult it is. Even experts are going to make a few mistakes and have to work through to "fix' things from time to time. We can all need a bit of a helping hand, but we have all seen how difficult and how much time it takes to hold ones hand through the process and that seems to be all I get to do with this project these days. I can only imagine what would happen if I were to "sell" the things. Plus, you know...it was supposed to be a DIY project...and never would I have dreamed that it would still be going 8 years after this design was given out.
...
Anyway, I hope that helps a bit, I know that GN2 is a forum that perhaps the sustainer project would have a 'natural home' and accommodate it. But, it would need to be handled differently now that I know what it is and what people seem to need. The question is, do I have the time to put that together, and is there the "need" and interest to justify still further information and discussion.
Plus, things move on...but I'd be pleased to help anyone here that is seriously thinking of building the thing or being involved in the project. As I say, I generally have up to a half dozen people emailing me directly now and most of the information just seems to need repeating and explaining again and again which is time consuming and that advice is just lost into the ether!
Thanks GN2 fellow modders!
|
|
majorwoody
Rookie Solder Flinger
Posts: 11
Likes: 0
|
Post by majorwoody on Oct 26, 2010 15:13:09 GMT -5
I build sustainer to 4mm -using the 0.2mm winding ....and with LM386 amplifier - he is  (no drive top strings). Anyone know the better circuit? DIY Sustainer circuit on net....they are piss.
|
|
|
Post by 4real on Oct 26, 2010 15:38:38 GMT -5
Suggest you consider buying a commercial unit perhaps.
The LM386 needs a buffer or it will load the input, details of what you are using is nil. The quality of the driver, particularly the potting, it needs to be solid to prevent internal vibration...4mm can work, 3mm even better, again details of what you have actually done, nil. The type of signal going into the circuit, ie the pickup, can have a big influence. A mid range or bass heavy HB for instance is not going to drive the high strings as well as the whole thing will be bass heavy. To 'bias' a LM386 for more treble response and less bass...use the often repeated suggestion of a 100uF output cap instead of 220uF as I do, again details of what you have done, nil. Gauge of strings, even fernandes and sustainiac recommend 10's, if you use ultra light strings and or a poor set up, this will affect performance as there is not much metal for an electromagnet to work on the lighter the gauge, again, details nil. Self expression, also nil...likely capacity for success is...debatable
The fact is that dozens of 'sustainers' have been built to this model successfully with LM386 or other circuits and this model driver.
My guitars, in particular later models such as my tele that uses a 3mm driver of this design and an LM386 circuit will sustain all strings including the highest strings and highest frets in both harmonic and fundamental modes. So too my earlier models that are well known to have used a stock LM386 circuit, a 100uF output cap and a generic preamp...all from cheap and easily available kits. As this driver only requires any basic amplification to work really, it is likely not the 'circuit' that is the problem.
This project is not for everybody, perhaps it is not for you. There are plenty of commercially available units about that work well although installation can be complicated and crucial.
Anecdotal lack of success and the conclusion that 'he is piss' and it must be 'the circuit' seems a little OTT and does not bode well for success...but good luck anyway
|
|
majorwoody
Rookie Solder Flinger
Posts: 11
Likes: 0
|
Post by majorwoody on Oct 26, 2010 15:52:33 GMT -5
For the reply...thanks to you. Buy one?...no have dinheiro! Have facilities...make the thing. >> "Mr D.I.Y. Sustainer ;-) "All circuits  - do you ahve a circuit for here? I will sell. Peace.
|
|
majorwoody
Rookie Solder Flinger
Posts: 11
Likes: 0
|
Post by majorwoody on Oct 27, 2010 9:37:46 GMT -5
Mr 4real...you post at feet of your signoff...
>> "Mr D.I.Y. Sustainer ;-)"
??
Two parts any sustainer, wire coil & circuit (my 4mm wire coil ok, but circuit suck) ...you call you "Mr DIY sustainer" - so you has circuit sustainer for the forums?
|
|
|
Post by 4real on Oct 27, 2010 15:24:29 GMT -5
If you research you will find plenty of circuits, this one of Col's (all right's reserved)..."he is piss" also? Came from this very thread, and that's why you are here is it not, because I linked to it for that reason? You clearly don't know the meaning of DIY...Do It Yourself...just like I did. You also don't seem to have the capacity to follow the simplest of instructions and principles required for this project and this is why your project has or is failing...there are hundreds and thousands of words and yes 'circuits' for you to follow in related threads...me adding more will not help clearly as you lack the ability and will to understand...but as MY project is designed to run of any suitable non-loading poweramp effectively...there are thousands of generic suitable amplifier circuits available that can equally work...and many of those have been pointed out as well. If still you consider all this information "he be piss"...there is always the USPTO where you will find the circuits for Sustainiac, Floyd Rose, Fernandes and many others..."he be piss" also? Then there is always the DIY route, as this is a DIY project after all. No one told me how to approach this project, you are lucky that someone has...oh, that would be me...over the last decade. You could of course contact others who have offered up such a project about their circuits...oh, there are none...too bad! If you mean by "he be piss" you are referring to me personally...well then, why would you even want to know what I might have to offer...or think at all that anyone would want to buy one from someone like you? But, clearly you spend all your time trolling about contributing nothing like your cohorts and as a result can't find the time to actually read anything. If you don't know enough to construct a simple basic non loading amplifier, then this project is beyond your abilities. You could use kits that are very simple, as I did on all the early guitars in this very thread which dates back to 2007 if you had looked. Or you could wait till you grow up and learn enough to actually do something for yourself...as in DIY... But perhaps these words are all too much for you...so look up the internet term "Troll" and get a life and move on...
|
|
majorwoody
Rookie Solder Flinger
Posts: 11
Likes: 0
|
Post by majorwoody on Oct 27, 2010 16:06:11 GMT -5
English not my language (should be clear). Mod told me better not use the word now (learned English in a pub)
You very agressive...me just searching for a good circuit...lots no good (weak sustain on bottom frets ....top E & B strings) - nobody on net seems to have good circuit.
that circuit you showed me ...will not working properly either (no power IC chip...just operation amps?!!! Any others?
hello.
|
|